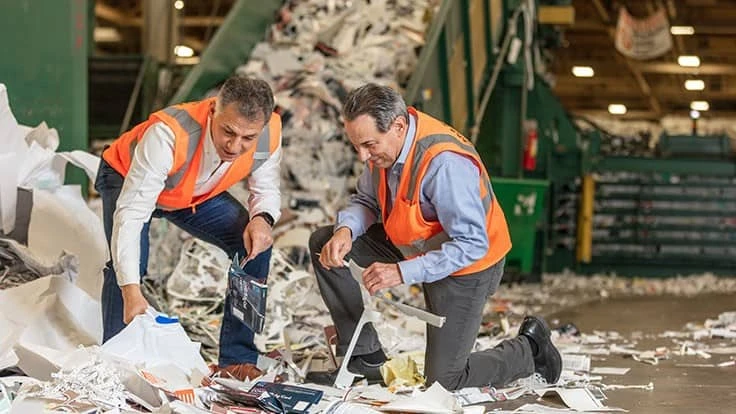
Daniel Motta Photography

Texas Recycling is a well-known presence in the recovered paper industry. For nearly three decades, the Dallas-based processor has focused on buying and selling scrap paper, primarily high grades such as sorted office paper, deinking grades and bulk grades. The company also buys and sells bulk grades such as old newspapers and old corrugated containers (OCC).
Stan Litman had worked for many years as a traveling sales manager for a large industrial chemical company. But at age 52, he made a career change and started working for a Dallas-based paper and rag business called Daltex Waste Material Co.
Stan eventually purchased that business. Both of his sons, Joel and Craig, joined him at Daltex in 1984 and 1989, respectively.
In 1992, Stan and his sons wanted to start something new. Stan sold Daltex, then with Craig and Joel as co-owners, launched a new paper scrap business known as Texas Recycling/Surplus in a 30,000-square-foot warehouse that they leased in Dallas.
“We did not have one pound of paper when we started Sept. 1, 1992,” Joel recalls. “We were like, ‘Now what?’ But we just started moving. We were confident we could get this going.”

Founded on paper
Pound by pound, Joel says, the company developed its scrap paper business, eventually outgrowing that 30,000-square-foot building in 2001. Texas Recycling expanded the facility to 50,000 square feet that year by moving into an adjoining building. About six years ago, the company reached a point where it needed to move entirely to a new and larger facility.
“We were operating in nearly 140,000 square feet of space spread out over four to five buildings,” Craig says. “It was so inefficient going from one building to the other and to the other.”
Part of the reason for moving was to accommodate the diversification of the business. The company became involved in document destruction by starting Action Shred of Texas in 2003. Since its inception, Action Shred has expanded its services to include hard-drive destruction and, most recently, product destruction.
Craig adds that the company also needed space to accommodate higher incoming volumes of OCC.
“We have always been more of a high-grade operation. It’s kind of our niche market,” he says. “But that was one of the reasons we moved—we were missing opportunities with OCC, a prominent grade in the paper industry, and we really couldn’t handle it the way we were set up in our old facility. We weren’t able to take large loads of loose OCC. [Moving] allowed us to do everything so much more efficiently.”
Stan died in 2003, having retained his stake in the business up to that point. For the company’s next chapter, Joel and Craig say they wanted to see Texas Recycling grow its metals processing business. Getting a bigger space helped when adding equipment for this segment of the business.
“The paper business is a mature industry. We asked ourselves, ‘How else can we grow?’” Joel says. “A lot of folks were getting into MRFs, and we thought that really wasn’t what we wanted to do. We then went to metals. We had dabbled in it and knew people in it. We saw opportunities in metal that we really thought would spur growth.”
Moving into metals
For nearly 25 years, Texas Recycling focused a good deal of time and effort on growing its paper recycling services. Although the company handled used beverage cans at its buyback center, becoming more focused on scrap metals processing required Texas Recycling to invest in new equipment and to gain knowledge.
Because neither Joel nor Craig had much experience with ferrous and nonferrous processing, Craig says it was important to hire the right people to expand in that area.
“You sometimes get into a comfort zone, where you’re handling the same thing over a number of years,” Craig says. “But then you push your limits a little, move into a new area, find experts and let them do what they do best. We hire people that have the expertise because obviously Joel and I can’t do everything. … You want to rely on people to do what they do best.”
After relocating to its new site, Texas Recycling hired Bill Prager, whom Joel and Craig knew and had worked in the scrap industry for nearly 40 years, to lead its metals processing division. He has helped to grow that business from the ground up.
“When I got [to Texas Recycling], the only metals business they had was in connection with paper or cardboard accounts—like litho plate aluminum from the printing process—but no straight metal accounts,” Prager says. “I started with virtually zero accounts,” he adds.
In the metals segment, Prager says he has focused only on industrial accounts. To date, the company has about 100 industrial accounts, which Prager says is “not bad for five years.”
Starting from scratch also meant working with new equipment. “All of our trailers and roll-off trucks are brand new,” Prager says. “That gives us an upper hand.”
Since starting the division, it has focused on processing busheling on the ferrous side and stainless steel and some aluminum scrap on the nonferrous side, explains Prager, who says he has enjoyed building Texas Recycling’s metals business.

Combining under one roof
In late 2015, Texas Recycling leased and moved into a new facility on the east side of Dallas that was a former auto assembly plant. It is bout 14 miles away from the company’s original location in northwest Dallas and is big enough to house all its divisions under one roof. The plant has 260,000 square feet of interior space and more than 3 acres outside for rolling stock.
Although many companies process scrap metal outside, Joel and Craig are doing so indoors. “We were moving to the core of the city,” Joel says. “We had to have everything indoors to get this space. City zoning regulations didn’t allow us to have scrap outside.”
He adds that storing and processing material indoors also would be preferential from a quality standpoint, and it provides community relations benefits.
“[T]hat’s been part of being a good neighbor,” Joel says. “We’re located in a residential, light-industrial area. The neighbors didn’t want to wake up and look across the street and see cranes and piles of metal. We wanted to be good community citizens.”
Hillary Litman Freed, Joel’s daughter and the communications manager at Texas Recycling, adds that the four-to five-week move from the old site was challenging, ensuring all the equipment was delivered to the new site safely, all the while keeping the day-to-day operations running. She also describes the experience as bittersweet, watching the family company outgrow where it started.
“That had been our location for nearly 25 years. But, in order for the company to grow, the move needed to happen,” she says. “It’s been nice now that we’re all under one roof.”
Brian Morley, operations manager at Texas Recycling, says having all the company’s operations inside has helped in times of inclement weather. He adds that operating inside also helps to keep workers a little cooler in the summer months. “Where I’ve worked in the past, the majority of operations were outdoors, and there are often slowdowns due to weather. Here, it doesn’t happen that way.”
”We saw opportunities in metal that we really thought would spur our growth.” – Joel Litman, president, Texas Recycling
Another perk to the new location is that it features indoor rail. Morley says having rail inside the facility is “very convenient.”
With all the business units under one roof, Kathy DeLano, vice president of sales at Texas Recycling, says it has given the family-owned company even more of a family feel and made it easier for the different business divisions to communicate.
“All of our divisions work well together, and our customers like that we’re a one-stop shop for whatever they need,” she says. “Everybody says we’re like a family.”
Prager adds that Texas Recycling works to treat its customers like family as well, focusing on providing a high level of service. “Service is paramount in our business; it makes us different than the average bear. We provide customers great next-day service, and we’re transparent. We don’t have any surprises.”
Working through an odd year
In the past year, Texas Recycling faced many unknowns associated with the pandemic, much like other companies. Joel and Craig say the pandemic’s impact on commodity markets was among those unknowns in 2020.
Joel says recovered paper markets were poor heading into the pandemic. “On the paper side, 2019 was the worst market we’d ever experienced,” he says. “Then in January and February 2020, activity perked up for paper. But, then the pandemic hit, and things went south again,” Joel continues.
Adding to the pandemic-related uncertainty, DeLano says securing ocean freight and trucking have been challenging since the latter part of 2020. “But trucking has been an issue for years, and you work through it the best you can since it’s one of those things that is out of your control.”
However, she says, logistics, particularly in Texas, faced additional challenges after a brutal winter storm in mid-February led to power and water outages across that state and snowy roads, which made driving very difficult for one week. Texas Recycling had to stop operations for more than a week because of the inclement weather, which was the company’s longest period of downtime in its history.
Fortunately, Joel adds, the pandemic never shut the business down. Being deemed an essential business, Texas Recycling was open, though with some limitations. Some services were scaled back in the past year—Joel and Craig decided to shut down the buyback facility for one month as a safety precaution. Since reopening, it has only accepted paper and cardboard from the general public.
Throughout the pandemic, Joel and Craig say they have continually stressed safety with employees.
“We want them to be safe and healthy, not only because they’re part of our business family, but also for when they go home to their families,” Craig says.
He adds that the company paid employees if they had to take time off work for COVID tests, regardless of whether the tests came back positive or negative, and if they had to quarantine at home. Overall, only about 10 percent of the company’s employees were infected with the coronavirus associated with COVID-19 since the start of the pandemic.
Joel and Craig say they are now working to make sure Texas Recycling’s employees can get vaccinated.
More recently, Joel explains that markets have improved for paper and metals grades—particularly as businesses have opened up from pandemic-related restrictions and since the winter storm-related issues are behind them. “Manufacturing has picked up and the economy is improving,” he says. “The lights on the path are looking brighter.”
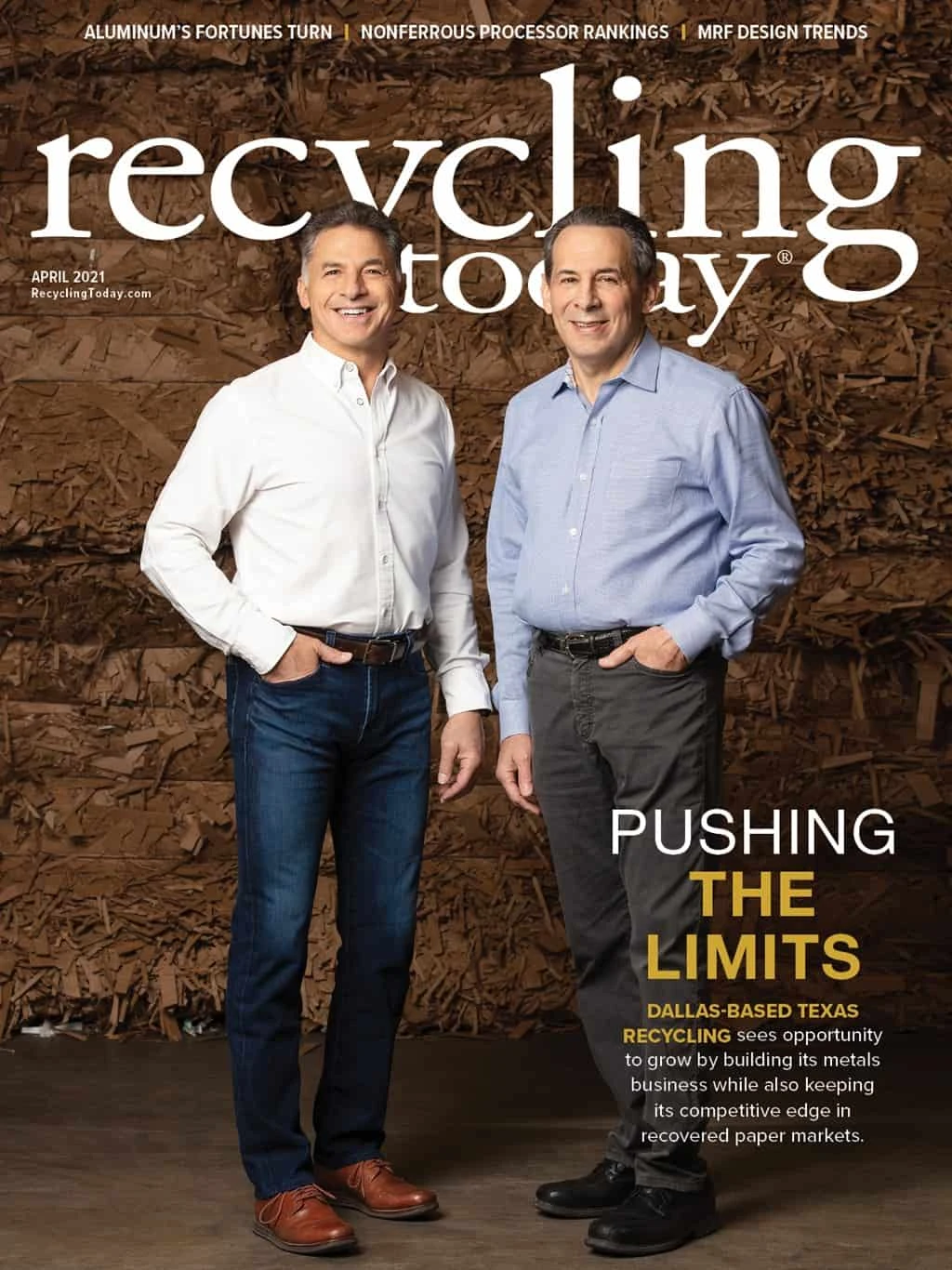
Explore the April 2021 Issue
Check out more from this issue and find your next story to read.
Latest from Recycling Today
- Ferrous price hikes may be poised to pause
- BIR prepares for Spanish exhibition
- Copper exempted from latest round of tariffs
- Interchange Recycling's EPR stewardship plan approved in Yukon
- Making the case for polycoated paper recovery
- Novolex, Pactiv Evergreen finalize merger
- In memoriam: Danny Rifkin
- BIR adds to communications team