
Many people who work in the waste and recycling industries have firsthand experience dealing with fires in their daily operations. The causes of these fire incidents include traditional hazards, such as propane tanks, aerosol cans, fertilizers and household hazards, as well as technology hazards, such as lithium-ion batteries.
Over time, the focus on fire safety has shifted from issues of compressed natural gas (CNG) tanks and hot loads on trucks to processing facilities, where more than 1,700 fire incidents occur annually.
At waste and recycling facilities, dealing with these incidents is considered “part of a day’s work.” Therefore, the only incidents to get reported usually are those that get past incipient or early flame stages to the point where the authorities are called.
In the 12-month period ending April 2018, news organizations reported 347 fires in waste and recycling facilities in the U.S. and Canada compared with 277 reported fires in the previous 12-month period. More alarming still is that in the first four months of 2018, the rate of reported fire incidents has been 93 percent higher than in the same period in 2017.
While these yearly increases could be part of the normal cycle, they are perhaps indicative of an ever-growing number of lithium-ion batteries in the waste and recycling streams, hotter/dryer environments and the increased volume of material being processed domestically in light of China’s recycling restrictions.
Combating the problem

Combating the risk posed to recycling operations by batteries begins with education and awareness. The major shift that must take place is perceiving fires as inherent in the type of work we do to seeing them as operational issues that can be fixed with better processes and procedures.
Leaders in the waste and recycling industries have changed their stance on fire incidents from one of
Rumpke Waste & Recycling, headquartered in Cincinnati, is one of these companies working to educate the public on fire prevention best practices. Rumpke, which notes on its website, www.rumpke.com, that it experienced more than one dozen fires at its Cincinnati and Columbus, Ohio, recycling facilities in 2017, says the main culprit is lithium-ion batteries.
After the source of a recent fire at one of its facilities was discovered to be a battery, a local news station shared advice from Rumpke’s website at www.rumpke.com/for-your-home/battery-disposal with viewers: “Placing batteries—specifically lithium-ion batteries—in your recycling and trash containers causes a dangerous situation. When batteries break, they spark fires, putting people—employees and the motoring public—unnecessarily at risk.”
By sharing these types of struggles with the public, we begin the much-needed process of changing behavior.
Not only are these batteries a fire hazard, they also are a source of contamination. Brent Bell, vice president of recycling operations at Waste Management, Houston, wrote a blog titled “The Battle Against Recycling Contamination is Everyone’s Battle” on the company’s website. In it, he writes, “It all boils down to recycling the right items the right way. This can be done by following a few simple rules: 1. Recycle all empty bottles, cans, paper
Operational best practices also must be put in place. No operator is immune from dealing with fire hazards, but things can be done to mitigate risks.
Brent Shows, director of recycling for Advanced Disposal, Ponte Vedra, Florida, shared a number of operational best practices in a fire safety session April 23 at WasteExpo. They included complying with the regulatory authority, not parking equipment near a potential heat source, implementing a
By observing these practices, educating staff and investing in technology, Shows says Advanced Disposal has reduced the number of fires the company has seen compared with three years ago.
When it comes to investing in safety technology, it is sometimes easier to continue to do only what is required, especially in the fire safety space where minimum standards are mandated by the National Fire Protection Association (NFPA), Quincy, Massachusetts. In the waste and recycling industries, bare minimum safety measures might not be enough to proactively protect against everyday hazards. For example, problems can arise in an operation that is housed in a warehouse with 30- to 70-foot ceilings where fire protection depends on radiant heat triggering a sprinkler head. This is a reactive solution that typically does not begin to work until the incident has had time to develop. This traditional solution also requires cleanup, resetting of the system and several other hassles and headaches following an incident.
Many waste and recycling facilities also have outdoor operations to consider that typically have little, if any, fire protection equipment in place.
For these reasons, new technologies are required to address fires at the source.
At Fire Rover, Southfield, Michigan, we’ve moved our focus from technology that’s designed to contain fires to early detection and cooling. This includes the integration of new applications of military-grade thermal detection, remote human verification and on-site remote targeted application of the system’s cooling agent.
The system is currently being used to protect tipping floors, system
Combining methods
With the risk of fire increasing, facilities must develop and install solutions to mitigate fires as early in the process as possible—especially when the materials handled in the waste and recycling industries are becoming increasingly volatile and unpredictable. Using a combined approach predicated on protection, education and refined operational procedures can transform a reactionary company into a proactive one. These are two different approaches with two vastly different outcomes.
Get curated news on YOUR industry.
Enter your email to receive our newsletters.
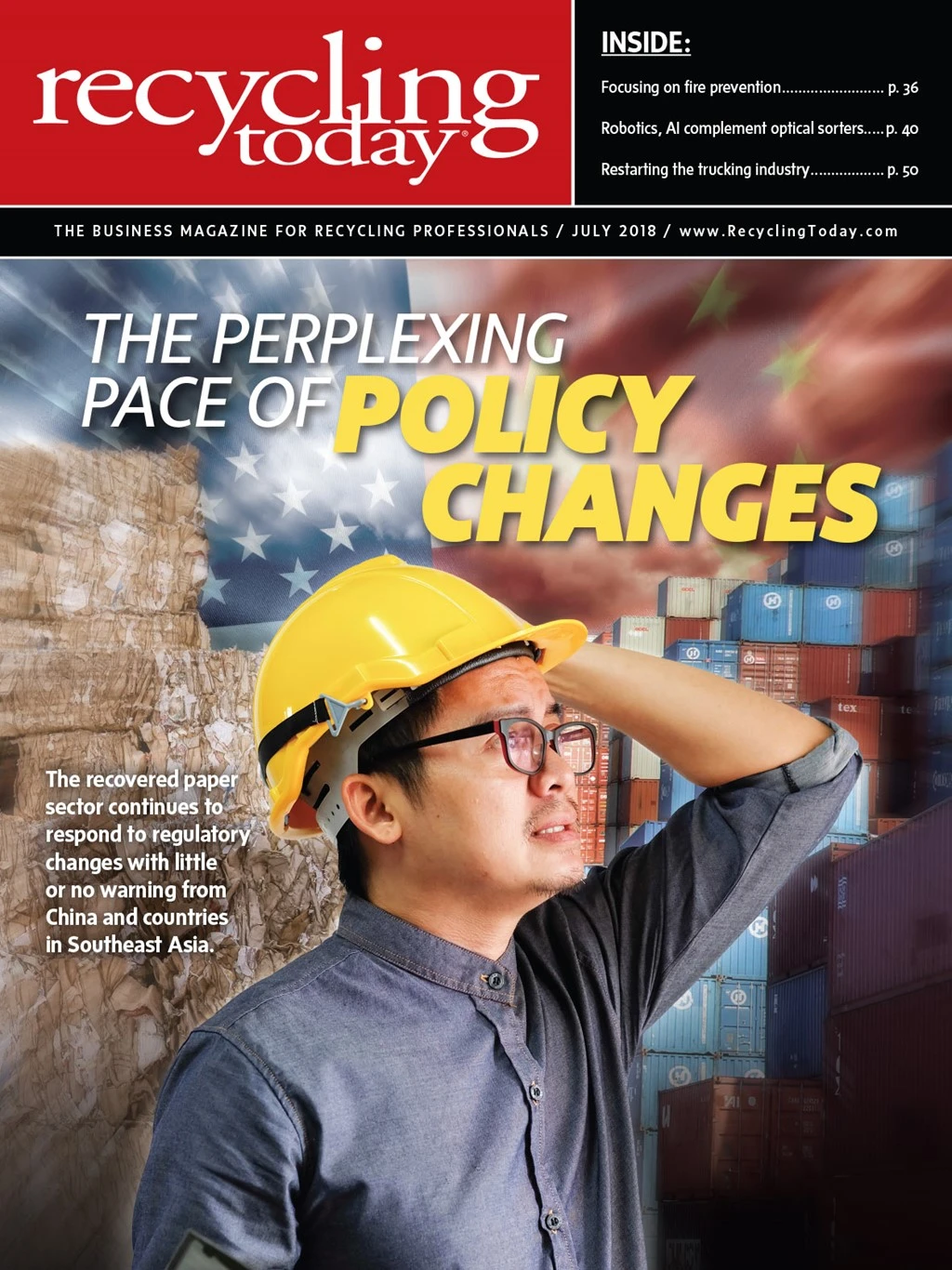
Explore the July 2018 RT Issue
Check out more from this issue and find your next story to read.
Latest from Recycling Today
- Call2Recycle Canada launches program in Alberta
- The history of SAS Forks: Celebrating 50 years
- SAS Forks partners with NED at Green Recycling in Houston, Texas
- DRKhorse’s RCC series at Gorick Construction in Endicott, New York
- Balar Equipment to operate under Enviro-Clean Equipment name
- Li-Cycle reports 2024 financials
- Wisconsin Aluminum Foundry acquires Anderson Global
- PureCycle, Landbell Group working to advance PP recycling in Europe