
“A major win for the scrap industry.” That is how the Institute of Scrap Recycling Industries (ISRI), Washington, characterized a Surface Transportation Board (STB) ruling in April 2020. This ruling was in response to presentations to the board by rail shippers concerned with rail service and charges.
In the midst of and in spite of COVID-19, did the scrap industry see a major win with the railroads in 2020? What are some of the issues shippers of all products faced that drew a hearing by the STB? While demurrage in general was a major driver for the April 2020 ruling, several issues have been of growing concern to customers:
- demurrage charges increasing;
- changes in demurrage rules reducing the time to load or unload before charges begin;
- a decline in operations service;
- increasing freight rates;
- growing inaccuracy of demurrage and freight bills;
- poor response from carrier customer service and sales; and
- excessive charges for canceling unit trains within a 48-hour window.
With the STB’s April 2020 ruling, it might seem odd that issues and changes have surged suddenly. Recyclers might be wondering what remedies have been proposed and enacted since this “major win,” as ISRI calls it.
Basics of rail shipping
The rail freight network in North America is one of the most capital-intensive industries in the world. It is self-sufficient in that the arteries through which its commerce run are owned and maintained by the railroads themselves.
Although it has oversight from agencies such as the STB and the Federal Railroad Administration, much of how the rail freight network operates is governed by its own organization that is managed and run by Class I rail executives, the Washington-based Association of American Railroads.
Government oversight, if done for the common public good, can require changes of a significant financial magnitude that the carriers must pay for themselves. Most recently, positive train control (PTC) was required on specified freight and passenger railroad route miles. Carriers had to implement this technology at costs originally estimated at $10 billion.
As a result, the rail carriers seek to drive efficiency into the network to remove costs and improve service. In the last few years, the late railway executive Hunter Harrison initiated a new way to operate and manage railroads: precision scheduled railroading (PSR). The stated goal of PSR is to benefit customers by providing consistent, reliable and predictable service. When successful, fewer rail cars are needed, planning is enhanced along the supply chain, costs are reduced, freight rates can be adjusted and everyone is happy.
If we look at a full cycle of how a rail car ships, it involves three players: the shipper, the rail carrier and the customer or consignee. Each player has a role in creating the desired efficiency, and how they each manage their segment impacts the whole. While not exhaustive, here are some of the actions each party controls:
- Shippers properly manage car orders (or private fleets); ensure clear and safe track capacity for cars when placement is needed; order cars for placement; load promptly upon placement; release shipments and issue bills of lading upon loading; and ensure switch crew access to pull cars safely.
- Carriers keep shippers and consignees informed of rail car status, including any demurrage accrual; supply all required rail cars as ordered and on schedule; process, release and create waybills promptly and accurately; pull and place rail cars on schedule and consistently; move cars through the rail network from origin to destination safely, reliably, consistently and on schedule; issue accurate and timely freight bills; issue accurate and timely demurrage or other accessorial bills; communicate any issues clearly and promptly; and resolve any delays or schedule deviations quickly.
- Consignees ensure clear and safe track capacity for cars when placement is needed; order cars in upon arrival (if closed-gate); unload promptly upon placement; release empty upon unloading; and ensure switch crew access to pull cars safely.
For the rail customer, whether shipper or consignee, the key question is how well the carrier is managing all the time it is in its care. Another way to put it is how good is the service that the carrier has claimed is improving specifically because of PSR.
A C+ at best
In an article written by Jim Blaze and published in Railway Age in February 2021, the author looks beyond the rhetoric of the parties involved and offers some data. The very title of his article provides a clue to his conclusion: “Railroad Service Improvement Perhaps a C+.” Blaze writes, “The benefits that PSR was to eventually give as cost savings to customer supply chains are floundering. The improvement isn’t always continuous.”
The goal of PSR is to deliver consistent, reliable and predictable service. And if that service includes at least all the items listed under carrier responsibility, how well have they delivered that service?
Union Pacific reports its carload performance for 2020 by quarter as 64 percent, 76 percent, 72 percent and 74 percent. Intermodal was reported as 85 percent, 82 percent, 77 percent and 83 percent. CSX reports its carload performance as 81 percent, 80 percent, 73 percent and 75 percent and its intermodal performance as 96 percent, 94 percent, 87 percent and 84 percent. Is there a major win in these numbers? Hardly. These give some indication of the overall improvement or lack thereof.
In the spring 2020 STB ruling, the primary issue addressed was demurrage. In response, most Class I carriers made some adjustments to tariff rules and rates to ease the burden. Providing visibility with online tools for shippers is of great value. They potentially can monitor status throughout the month, contact the carrier via means provided to address discrepancies as they occur and take action as needed to keep cars moving to avoid charges. If the carrier makes billing updates, responds to questions and disputes and corrects erroneous bills promptly when identified, we have progress and improvement.
COVID-19 must be considered when evaluating how well the carriers respond to requests. When an issue or problem is identified, every delay in response creates a potential delay in the consistent, reliable and predictable service. With many if not most carriers’ customer service forces reduced from PSR and most contacts still working from home, the problem is exacerbated. This critical area has a significant impact on the goal of streamlining the process. As digital as the world has become, business still relies heavily on the most valuable resource: people. A great deal of room is left for improvement here.
A few years ago, the buzzword within the rail community was “first mile-last mile,” the recognition that the carriers do a fair job of getting cars moved hundreds of miles from origin to destination. But getting those cars placed for loading and unloading, pulled and handled locally for shipment (i.e., local switching) were the areas in need of the greatest improvement. Most of the focus on PSR has been on major and broad changes—removing hump yards, declassifying intermodal as a separate business to be operated differently, etc.—with less emphasis on the first and final mile involved. This is where demurrage surfaces, service schedules are missed and frustration builds. Without due consideration and emphasis on this, can shippers see a major win?
Finally, shippers and consignees, the railroad customers, do have control over key areas that can influence whether the rail industry is consistent, reliable and dependable. Anything less than rigorous attention to their areas only will lead to more frustration, poorer service and higher costs.
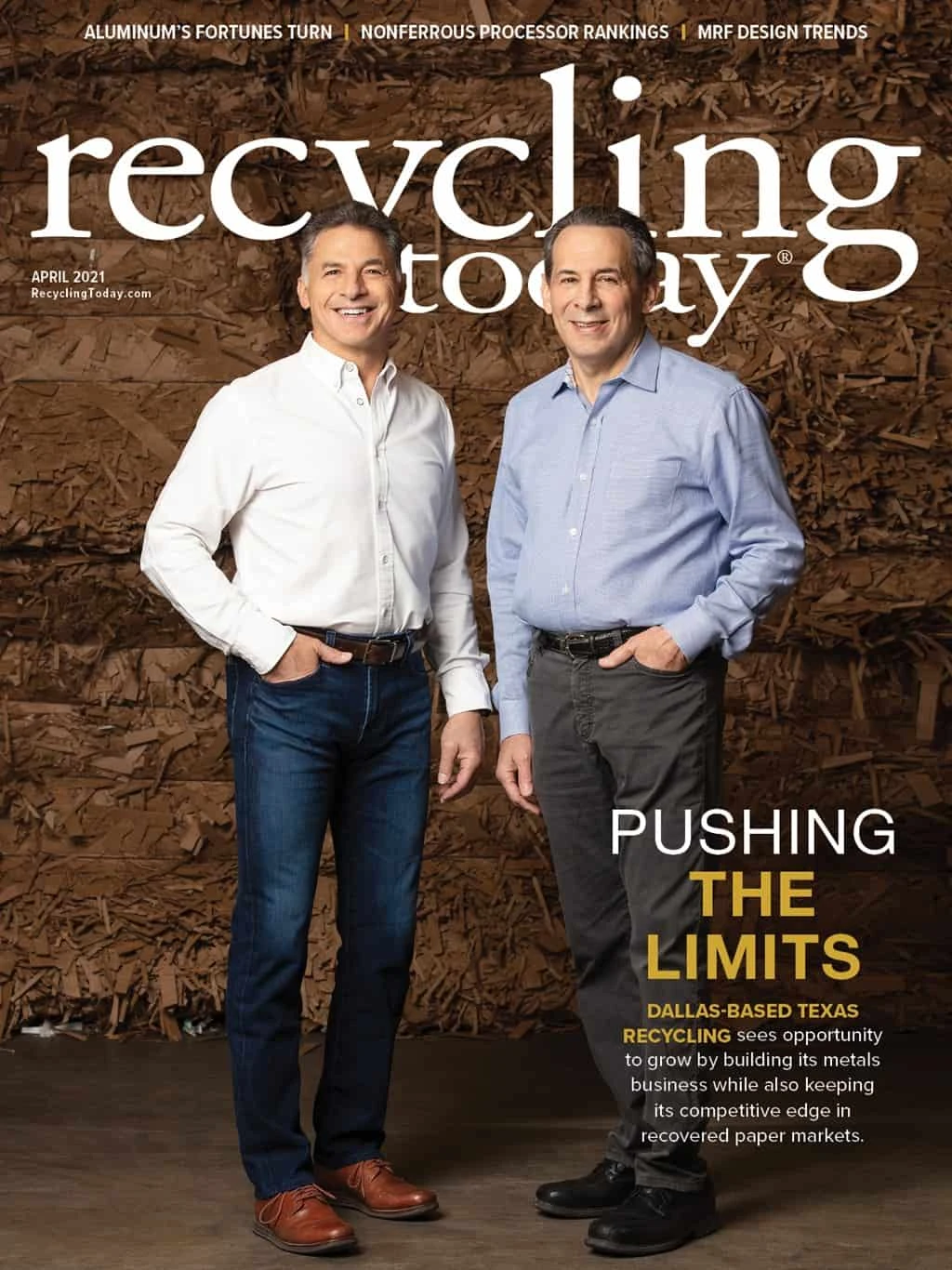
Explore the April 2021 Issue
Check out more from this issue and find your next story to read.
Latest from Recycling Today
- Unifi launches Repreve with Ciclo technology
- Fenix Parts acquires Assured Auto Parts
- PTR appoints new VP of independent hauler sales
- Updated: Grede to close Alabama foundry
- Leadpoint VP of recycling retires
- Study looks at potential impact of chemical recycling on global plastic pollution
- Foreign Pollution Fee Act addresses unfair trade practices of nonmarket economies
- GFL opens new MRF in Edmonton, Alberta