
Staying tuned into the latest technology is a crucial task that today’s material recovery facility (MRF) operators face. While these facilities are designed to last many years, it’s becoming increasingly important to design with flexibility in mind right from the start because retrofitting a MRF is no small feat.
Toronto-based GFL Environmental Inc. Vice President of Recycling Steve Miranda says MRF design is “all about adding value.”
He adds, “When designing or even retrofitting, we’re trying to think years in advance of what is the norm today.”
The decision to upgrade or retrofit a MRF can be based on various factors. “Ultimately, we’re service providers and will behave the way our customers want us to behave. So if our customer wants a certain outcome, we will go and achieve that outcome for our customer,” Miranda says.
Regulations, technology innovations and demand for higher quality recyclables are growing, and Miranda says those factors typically lend themselves to more technology integrations and decisions at the MRF.
“Retrofitting is expensive, you’re moving extremely large pieces of equipment, and you have to look at the process as ‘how long will this do what I need it to do,’” says Joaquin Mariel, chief operating officer at Austin, Texas-based Balcones Resources. Mariel says many plans need to start five to seven years out before implementation, and you’re usually looking at $5 million or more when it comes to the investments.
In addition, Jake Hansen, general manager of Sarasota, Florida-based Single Stream Recyclers, a Balcones company, explains that the retrofit process he was involved in was challenging, as it is with most already-established facilities. “You have to make sure all the different pieces of the puzzle are lining up completely to get [all the equipment] in properly.”
He says designing a MRF from start to finish is preferable to retrofitting a facility, particularly when robotics are involved.
Relying on robotics and opticals
Single Stream Recyclers operates an artificial intelligence- (AI-) powered MRF that includes 14 robotic sorters. Hansen says he has been involved in almost every aspect of Single Stream Recyclers’ operations over the years and worked closely on the implementation of the MRF’s robotics. He also is involved in the general maintenance of those units, he says.
Hansen says it would be tough to operate a MRF today without using optical sorters and robotics. “They make a cleaner, more efficient product than humans ever could.”
Single Stream Recyclers operates robots at its MRF to increase sorting efficiency and the quality of recovered recyclables. “The end goal is to recycle as much material that can actually be recycled,” Hansen says. “A lot of people look at whether it’s polymer type A or fiber type B as to how material can be sorted during processing operations, but the dimensions of those products that enter into a facility also directly affect the recovery of recyclables and the quality after they are recovered, ultimately meeting the demands of our end-market customers.”
He adds, “Technology has greatly assisted in advancing the ability to recover these products with great quality versus traditional mechanical operations.”
While using more automation can enhance the productivity of human labor, MRF operators don’t see technology as a threat to the workforce. “You will never be able to get rid of humans in this industry,” Hansen says. “There are too many variables, and there is always important maintenance to be done.”
Rather than serving as a replacement for personnel, Miranda says automation can be viewed as a companion to the people who staff a MRF.
“I don’t know that there will be an elimination of manual labor in processing facilities,” Miranda says. “It will change the approach and the way people utilize their labor force in operations. There will always be a need for labor. I don’t envision one of these facilities running without any labor; I just don’t think that’s possible.”
He adds, “But the use of technology is definitely an important complement to manual labor to further advance recovery processing and in-depth understanding of our operating efficiencies.”
A look ahead
“Every, couple of years there’s a new [technology] that we might get to look at integrating if we happen to be designing or retrofitting, whether it’s an upgrade to technology or brand new technology,” Miranda says. “But when you look at the past decade or even the past two decades, what a MRF looked like 15 or 20 years ago is really different than whatever it might look like today.”
While humans will remain integral to the operation of successful MRFs, Hansen says he would like to see systems refined to the point that they would greatly reduce the need for human labor.
“It’s still all new technology, even though it’s been a couple of years. [Robotics and artificial intelligence are] still new to the industry, and they’re still developing, and they’re still going through all the different hiccups that they’re going to experience,” Hansen says.
And, while the focus at Single Stream Recyclers has been on robots, Hansen says he personally would like to see advancements when it comes to optical sorters, which prove to be very valuable to Single Stream Recyclers’ operations, he says.
“I wouldn’t necessarily say just robots in general will be evolving. My favorite technology that we have are optical sorters, and they are the most efficient technology we use by far,” he says.
While Hansen says robots lend themselves better to quality control applications, optical sorters outperform robots in terms of volume of material processed.
Dealing with data
With the sophisticated technology comes something of perhaps greater value: data. Operators running these machines know they are able to collect and analyze data from all stages of their operations.
“Because we can depict the quality of material we’re producing, we’re able to use that information to show our buyers right away,” Hansen says.
Data can help operators fine-tune the design of their MRFs. “With operations, you will absolutely need to know the composition of your stream to help you design properly,” Miranda says. “If you don’t know what you’re feeding a system, how are you going to know how to optimize?
He continues, “I think it’s important for us as an industry to continue to look to these technologies and support them however we can. It only helps all of us. It helps the industry achieve the common goal of recovering all the recyclables that we can and producing a quality that end markets can use to put these materials right back on the shelves.”
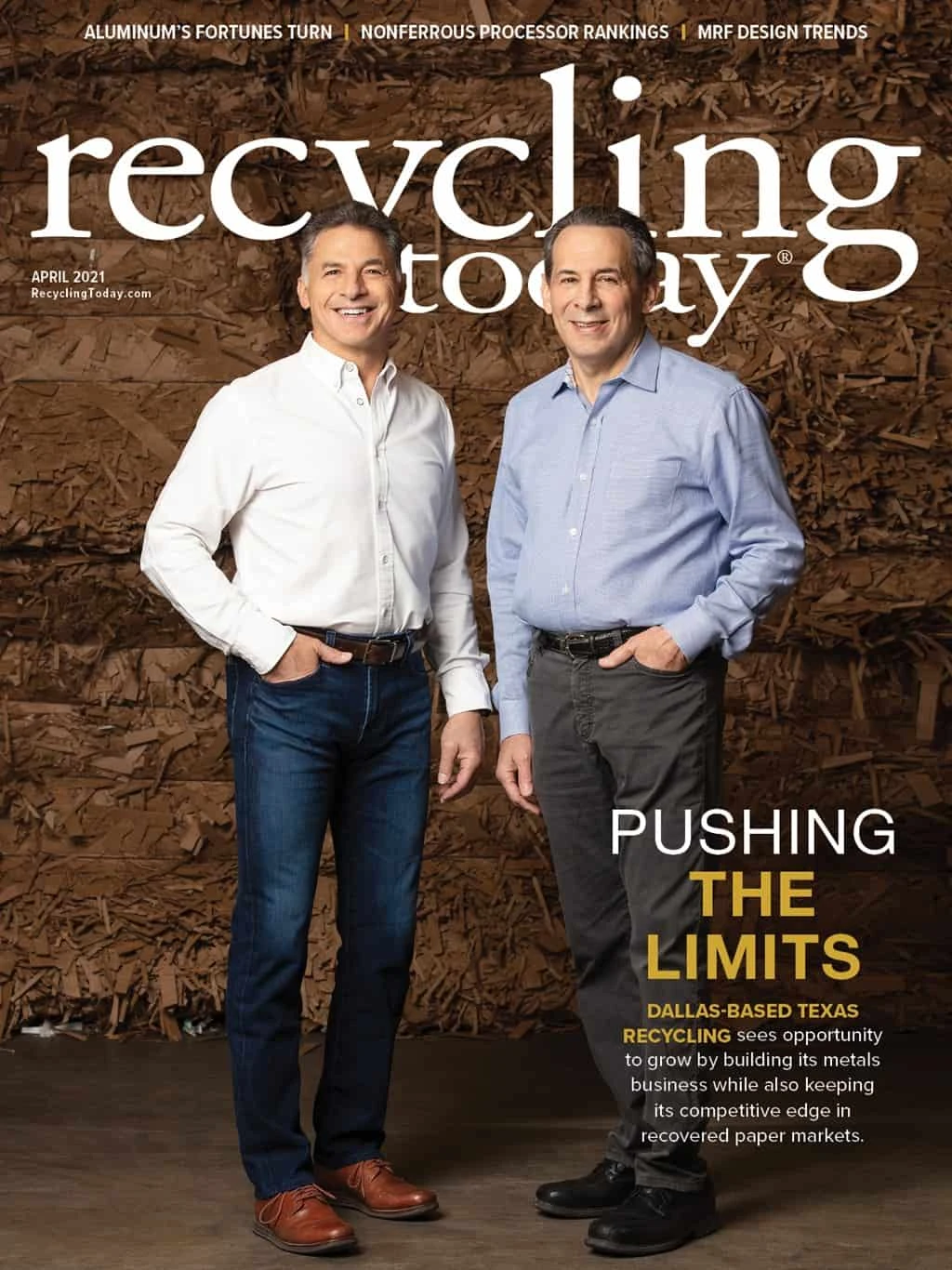
Explore the April 2021 Issue
Check out more from this issue and find your next story to read.
Latest from Recycling Today
- LumiCup offers single-use plastic alternative
- European project yields recycled-content ABS
- ICM to host colocated events in Shanghai
- Astera runs into NIMBY concerns in Colorado
- ReMA opposes European efforts seeking export restrictions for recyclables
- Fresh Perspective: Raj Bagaria
- Saica announces plans for second US site
- Update: Novelis produces first aluminum coil made fully from recycled end-of-life automotive scrap