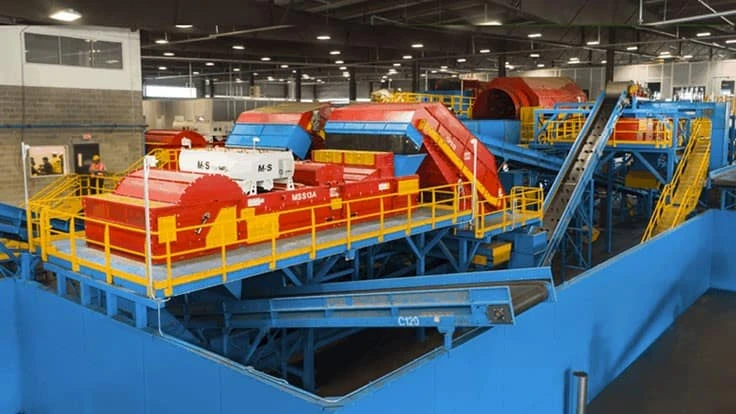

We are recyclers; operations is in our DNA. CP Group has evolved with the recycling industry and has consistently been at the forefront of innovation. This is due in part to our roots in owning and operating a material recovery facility (MRF) for over 25 years. We don’t just manufacture machines, we engineer solutions based on our firsthand experience. We understand commodity issues, we understand downtime and we understand ever-changing material streams. We relate to our customers because we live it every day in our MRF. That is the CP Group difference.
Beginning as a buyer and seller of scrap metals, Charles M. Davis founded the company in 1954. In 1977, he invented the world’s first aluminum can flattener. Since then, the company has engineered, installed and serviced more than 450 MRFs on six continents.
In today’s world of rapidly evolving material streams and increasingly stringent commodity specifications, CP Group provides confidence and security to customers. Owning and operating a MRF for more than 25 years, CP Group continues to advance MRF design, ensuring the highest possible recovery rates at the lowest possible cost.

A Future-Proof Approach
Our experience operating a MRF and developing them for customers navigates our future-proof system design. A core tenet to accomplishing that lies in our design principles to fractionate, liberate and separate.
By effectively accomplishing each of these phases, we can deliver higher recovery and stronger throughput with lower operating costs. Our machines have the latest technology, allowing for effective and profitable plant operation.
The CP Auger Screen is a game-changing tool for MRFs to fractionate material. Used as a primary separator, it cost-effectively reduces the presort load by at least 60 percent. This reduces the labor needed for presort and allows sorters to focus on the “big uglies”—large trash, rigid plastics, wrapping hazards and metals. It also enhances worker safety by reducing exposure to sharps and other hazards in the smaller fraction. The secondary Auger Screen is built with low-wear technology, and it maintains reliable sizing at high volumes. These machines are there to protect the people, not the other way around.
Through effectively segregating inbound streams into like fractions, our systems accelerate material liberation, allowing for more pure commodities. Our high-amplitude rubber and steel disc screens agitate materials at higher throughputs to remove the fluffy, high-volume 2D material from the rigid 3D material in the commingled middle stream. These machines are the lowest maintenance screens in the industry, with unmatched disc longevity. It’s not uncommon for our rubber CPScreen and AWScreen discs to run 2,000 or even 3,000 hours. Our steel GlassBreaker and OCCScreen discs run tens of thousands of hours.
From there, materials are presented downstream for separation that maximizes production levels and delivers higher recovery rates and superior purity. Our MSS optical sorters have the fastest belt speeds with the most square-feet scanned per second in the industry. These wider belts have high production with 96 percent typical purity rates. The MSS CIRRUS FiberMax™ optical sorter represents a true solution to increase recovered fiber quality. As our customers faced a changing market for recovered paper, we combined our top-of-the-line sensing capabilities with increased conveyor speeds to deliver high production and greater quality.
This systematic perspective ensures that greenfield plants and the most complex retrofit projects are managed, designed and installed in a way that boosts our customers’ return on investment. We manufacture machines that are extremely durable with low maintenance requirements.

In-House Reliability
As the industry has changed, CP Group has improved along the way to stay ahead of the curve. All our equipment is engineered and manufactured in-house. We have complete oversight from machinery design to production all under one roof. Our goal is to provide customers with high-quality, durable and low-maintenance equipment.
Additionally, our research and development team keeps CP Group at the forefront of technology as material streams evolve and the need for new equipment emerges. Our continuous advancements are rapidly integrated into our systems because of efficient testing on-site and in our MRF.
Delivering successful plants and retrofits that exceed customer expectations is core to our success. CP Group’s headquarters in San Diego, California, has 115,000 square feet of manufacturing space, and our MSS optical sorting division in Nashville, Tennessee, has 46,000 square feet. We have the capacity and flexibility to adjust our manufacturing to the speed of any project.
By using automation and state-of-the-art manufacturing, we consistently and cost-effectively deliver superior quality machines. We work to eliminate customer pain points and focus on lowest cost-per-ton solutions.
The investment in our shop is an investment in our customers and our future. We take pride in our work, and we stand by our solutions.
Innovation for the Future
From the earliest days of designing can flatteners and densifiers, CP Group learned that innovation must deliver operational efficiency to add value for plant owners. This disciplined approach has guided our research and development work. CP Group holds more than 50 patents, each one curated to deliver operational value.
The future of mechanical screening maximizes sorting efficiency while minimizing cost. Our latest development is the patented CP Elliptical Auger Screen that adds aggressive agitation to the sorting process, fractionates the stream and then liberates the material. This can be used for primary and secondary sorting. That dual action earlier in the process enhances downstream separation.
We make sure to stay on the pulse of ingenuity for our industry by enhancing and fine-tuning our solutions. Our real-world experience combined with our tribal knowledge guide the CP Group team in delivering advanced sorting systems that work hard for our customers.

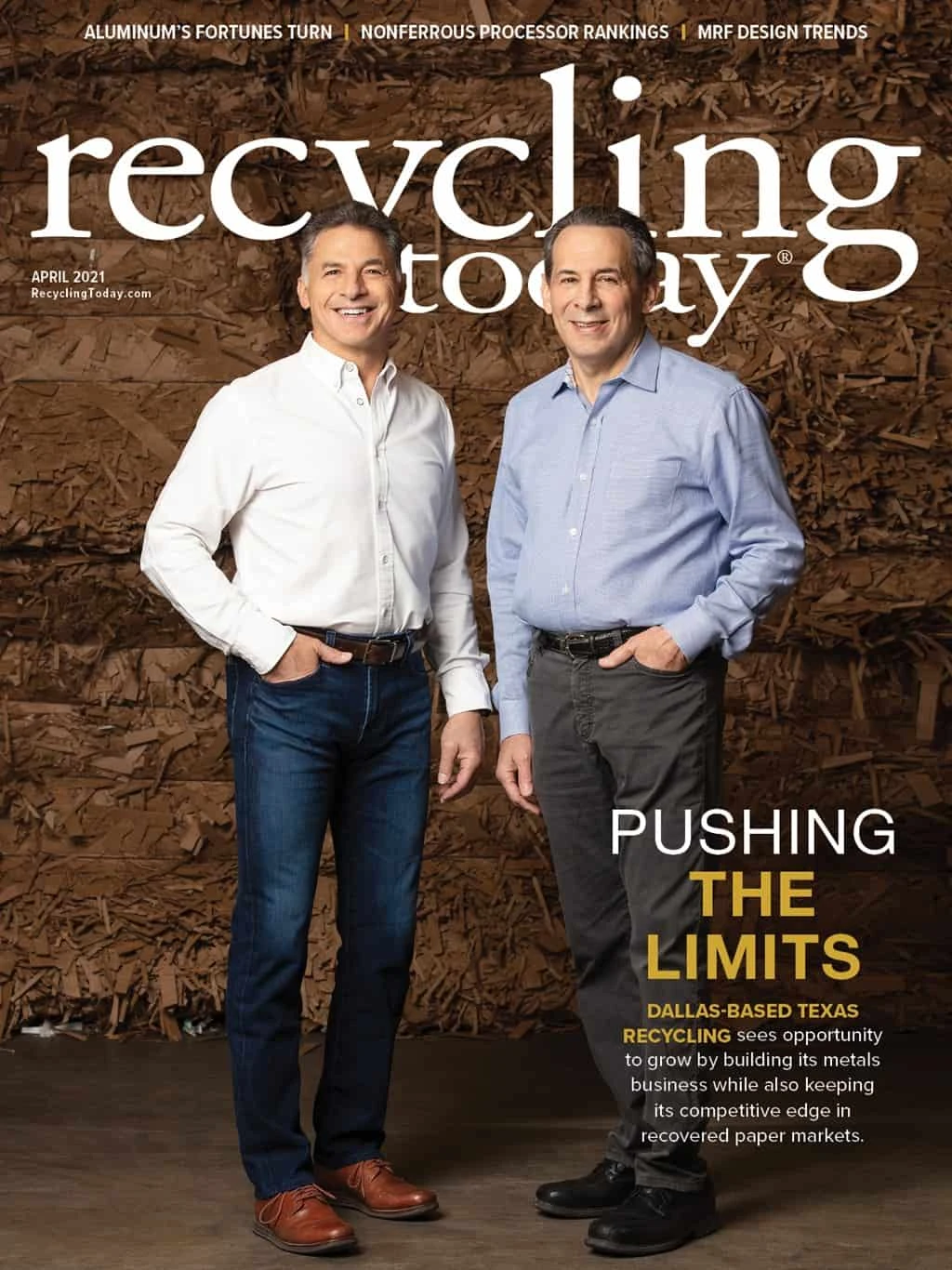
Explore the April 2021 Issue
Check out more from this issue and find your next story to read.
Latest from Recycling Today
- Tariffs likely rising on inbound steel, aluminum and copper
- CMC suffers losses in late 2024
- Nonferrous recyclers: Where do you rank?
- DTG Recycling faces $3.3M penalty from Washington Utilities and Transportation Commission
- Nippon, US Steel respond to Biden’s prohibition against US Steel purchase with lawsuits
- Recycling Today Media Group's battery recycling conference relocates in 2025
- IP amends DS Smith takeover bid
- Cleveland-Cliffs adds board member