
Bryce Stalcup
Recycling Operations Manager at Waste Commission of Scott County
Bryce Stalcup got his first taste of what it was like to work in the waste and recycling industry as a high school student at the Scott Area Landfill in Davenport, Iowa, which is owned by the Waste Commission of Scott County. The intergovernmental agency also operates a material recovery facility (MRF), a household hazardous material facility and an electronics recovery center in Davenport. Although he says he didn’t mind the work, Stalcup did not think it might lead to a full-time career.
In 2010, he received a Bachelor of Science in Conservation and Environmental Science and a minor in Business from Mount Mercy University in Cedar Rapids, Iowa. Just before graduating from college, he found out Waste Commission of Scott County was hiring a special waste coordinator for its household hazardous material facility. Stalcup says he applied and was offered the job.
Since accepting that position, he has taken on a few different roles at Waste Commission of Scott County. He was special waste manager for that same facility for a few years and also recycling operations manager in 2015.
"Build your reputation from action: Treat people right, provide adequate pay and benefits and listen to what people think and care about.”
“I would have never thought I would have gone back [to Waste Commission of Scott County],” Stalcup says. “But, today, I couldn’t imagine myself anywhere else. The mission, values, community and people here have kept me in this industry.”
Recycling Today (RT): What technologies are featured at the Waste Commission of Scott County MRF?
Bryce Stalcup (BS): In 1995, we opened as a dual-stream facility and processed that way until 2015. In 2016, we upgraded to a single- stream MRF, completely removing our old equipment [and] installing new equipment, and expanded our building. To move forward with this project, we had to have 15,000 tons to process, which we did secure. This year, we will process nearly 40,000 tons, operating two shifts.
In 2019, we added a dual optical sorter, separating 3D fiber and [polyethylene terephthalate, or PET] from the stream. Late 2020, we installed a dual-compactor setup to maximize run time. And in early 2021, we installed a new, larger baler to keep up with our throughput.
RT: What are new MRF technologies that excite you the most and why?
BS: Artificial intelligence and robotics. I really like the idea of the system being able to recognize how it is running, what it is missing and how it can adjust itself to provide the purest product. Since people are so hard to find, I do think we will see an exponential increase in investments like these.
RT: On the topic of people, what are good recruitment practices?
BS: I think you need to focus on improving your culture and reputation. You don’t go and just say you are a great place to work; you actually have to be a great place to work. Build your reputation from action: Treat people right, provide adequate pay and benefits and listen to what people think and care about. Invest in your teams with training and provide growth opportunities internally, even if it means more of a time commitment of upper leadership.
Meet monthly within your leadership teams and talk about leading—the good, the bad and the ugly. We all make mistakes just like anyone else, and sometimes we can get wrapped up in operations. You need to be able to check yourselves and regroup.
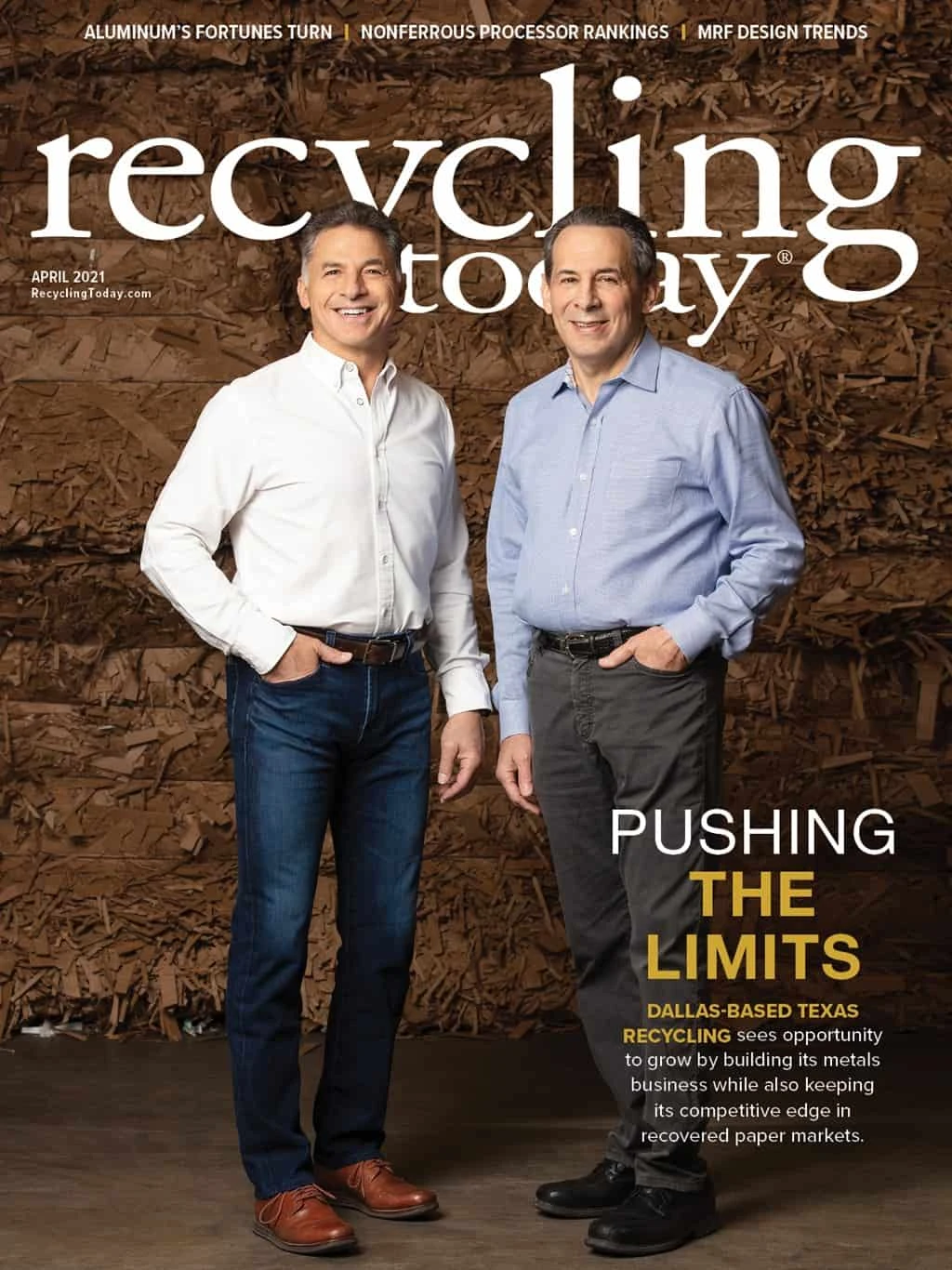
Explore the April 2021 Issue
Check out more from this issue and find your next story to read.
Latest from Recycling Today
- LumiCup offers single-use plastic alternative
- European project yields recycled-content ABS
- ICM to host colocated events in Shanghai
- Astera runs into NIMBY concerns in Colorado
- ReMA opposes European efforts seeking export restrictions for recyclables
- Fresh Perspective: Raj Bagaria
- Saica announces plans for second US site
- Update: Novelis produces first aluminum coil made fully from recycled end-of-life automotive scrap