VDRS to equip FCC’s Houston MRF
FCC Environmental Services recently received the contract from the city of Houston to design, finance, build and operate a material recovery facility (MRF) that will sort and market the city’s recyclables for 15 years, extendable up to 20 years. FCC Environmental Services is The Woodlands, Texas-based U.S. environmental services subsidiary of the Spanish company FCC Group.
FCC has partnered with equipment supplier and system integrator Van Dyk Recycling Solutions (VDRS), Stamford, Connecticut, to install the MRF’s high-capacity sorting system, which incorporates some of the most advanced technology on the market, according to VDRS. The previous collaboration between the two parties, FCC’s Dallas MRF, received the National Waste and Recycling Association’s (NWRA’s) Recycling Facility of the Year Award in 2017.
Because the city of Houston is allowing glass and film to be added back into its recycling program, the new MRF will feature a glass cleanup system as well as a 13.5-foot-wide elliptical separator to screen out film plastics. VDRS says the system is similar to FCC’s Dallas plant (which screens out film plastics at twice the national average) but will contain additional optical sorters to maximize fiber quality and to automatically recover plastic film.
“Van Dyk is excited to partner again with FCC for this new project and
FCC’s Houston MRF is scheduled to be completed in the spring of 2019, VDRS says.
The expected value of FCC’s Houston contract is more than $250 million, including the sale of recovered recyclables processed from Houston as well as from third parties.

Newell Equipment finds receptive market in China
Scott Newell Jr., chairman
Among the recent installations is one in the city of Anyang in Henan Province, China, that features three infeed conveyors to supply feedstock in steady amounts to an 11,000-horsepower shredder. “When shredding, there are plenty of times when the plant is operating at 500 or even 600 tons per hour,” he says.
Newell adds that his company has orders for three more such 11,000-horsepower shredders in China and has orders for “11 of our 6,000-horsepower machines, three of our 4,000-horsepower models and one of our 3,000-horsepower plants.”
Newell, whose father was an auto shredding pioneer and who now has several decades of shredding equipment sales and installation experience himself, says of the 11,000-horsepower super-sized plants, “It is difficult to imagine the necessity of feeding the equivalent of 10 automobiles into the infeed chute every minute (or one every six seconds). That is the beauty of having three infeed conveyors. It provides space for three to six cranes to be feeding the shredder at any given moment.”
McNeilus creates refuse business unit
McNeilus Truck and Manufacturing Inc., an Oshkosh Corp. company based in Dodge Center, Minnesota, has refocused its structure to create a new Refuse Collection Vehicles business unit. Jeff Koga, whose previous experience includes vice president of Integrated Product Support for Oshkosh Defense vehicles, leads the unit.
In his role as vice president and general manager of McNeilus Refuse Collection Vehicles, Koga will lead all initiatives of the business unit, including product development, production
The appointment of Koga is part of a new corporate structure that includes three distinct business units: Refuse Collection Vehicles, Customer Support Solutions (formerly Aftermarket Parts and Service) and Concrete Mixers. This structure simplifies the business, concentrates focus on customers and products and aligns resources to deliver service and performance, according to McNeilus.
“This new organizational structure allows the company to leverage decades of experience and renew its focus on delivering specific products and services vital to the success of our customers,” says Brad Nelson, president of Oshkosh’s Commercial Segment and McNeilus Truck and Manufacturing. “We have equipped each of these three business units with the resources necessary to ensure their independence and success through end-to-end accountability. These resources include human resources, finance, sales, marketing and operations functions.”
Koga brings extensive experience with severe-duty vehicle production, lean manufacturing processes

AMCS secures investment
AMCS, a leading supplier of integrated software and vehicle technology for the resource management, waste collection
The investment will be used for continued product development in AMCS’ suite of software as a service (SaaS) products and related technologies; to further accelerate the company’s growth in North America, Europe
“Today’s announcement represents a major milestone for AMCS,” says Jimmy Martin, CEO
Under the terms of the funding, Euan Menzies, senior advisor at Insight Venture Partners; Henry Frankievich, vice president at Insight Venture Partners; and Robert Schnittger, investment director at ISIF will serve on the AMCS board as nonexecutive directors.
“Since our initial investment in 2015, Insight Venture Partners has taken pride in the growth and success of the AMCS team,” says Menzies, who will assume the role of board chairman. “As the clear leader in technology solutions for the recycling and waste management communities, AMCS has continued to establish their stake in the ground across geographies. We look forward to their continued international growth.”
The investment comes as AMCS closed out a record 2017, according to the company. AMCS experienced more than 50 percent growth in the adoption of its SaaS solutions by the world’s most successful operators in waste collection and recycling and also announced the completion of its acquisition of Brady Recycling Solutions, a global provider of trading, risk management and settlement solutions to the energy, commodities and recycling sectors. The purchase extends AMCS’ portfolio, enabling the company to provide a suite of software offerings designed specifically for commercial scrap metal recycling operations.
To accommodate AMCS’ rapid growth, the company says it will open a new global headquarters at City East Plaza in Limerick, Ireland, in late summer 2018. The additional office space will support the company’s continued expansion as it creates 100 new jobs in product development, sales
_fmt.png)
NGR to supply plastic recycling lines at two US plants
Next Generation Recyclingmaschinen GmbH (NGR), headquartered in Feldkirchen, Austria, with a U.S. sales and support office in Atlanta, has announced two upcoming projects in the U.S.
Sigma Plastics Group, Lyndhurst, New Jersey, is increasing its recycling capacity with the addition of four new high-output recycling lines from NGR. The four S
The Green Line Polymers subsidiary of Advanced Drainage Systems Inc. (ADS) also has commissioned a new plastics recycling line from NGR at its facility in Pandora, Ohio. NGR says the plastics granulating line is the largest such piece of machinery it has ever produced.

The equipment manufacturer indicates the model being installed can convert more than 4,000 pounds per hour of a diverse type of plastic scrap, including industrial polyethylene, into what it calls a high-quality recyclable plastic granulate.
The recovered granules will be used to manufacture drainage pipes and hoses for ADS, which produces a variety of thermoplastic pipe and hose products used primarily in the construction industry.
The Sigma Plastics Group was founded in 1978 by Alfred Teo and is the largest privately owned film extrusion group in North America. The company has 42 manufacturing facilities producing an annual throughput of more than 2 billion pounds of resin and employs more than 4,700 people. Sigma manufactures a variety of flexible packaging products for the industrial, agricultural, food, medical, retail
The new recycling lines represent an investment of nearly $3 million and will be installed at Sigma plants in Pompano Beach, Florida; Spartanburg, South Carolina; Jacksonville, Florida; and Nashville, Tennessee. With the new NGR lines, these Sigma plants will be able to get the highest possible value from their film scrap by using the reprocessed material directly into new film production, the equipment supplier says.
The Sigma Group has more than 40 NGR recycling machines operating at its plants in the U.S. and Canada.
NGR has supplied more than 1,200 machines worldwide.
_fmt.png)
Goodyear adds to its total solution package
The Goodyear Tire & Rubber Co., Akron, Ohio, has expanded its total solution package for waste haul fleets with a new retread product, a new commercial tire management program and other additions.
Goodyear’s total solution consists of products, services
“Goodyear is committed to helping waste haul fleets lower their operating costs, which is why we are strengthening our total solution,” says Evan Perrow, the company’s senior product marketing manager.
Goodyear’s total solution for waste haul fleets includes a number of new elements:
- The Goodyear Endurance WHD retread complements the Endurance WHA, Goodyear’s longest-lasting waste haul tire. Designed for the drive axle, the Goodyear Endurance WHD contains a dual-layer tread compound for slow wear and low rolling resistance; a 32/32-inch tread depth for enhanced miles to removal; self-cleaning grooves to help evacuate mud and snow; and other features.
- The Goodyear Tire Optix commercial tire management program, through which trained Goodyear tire technicians use a special scanning device to electronically capture tire data, such as air pressure and tread depth. This information automatically uploads via Bluetooth to a cloud-based platform in real time for password-protected storage and easy access. Data can then be downloaded through the new Goodyear Tire Optix App for immediate viewing by waste haul fleets.
Goodyear employs 64,000 people and makes its products in 48 facilities in 22 countries. It has Innovation Centers in Akron and Colmar-Berg, Luxembourg.
Get curated news on YOUR industry.
Enter your email to receive our newsletters.
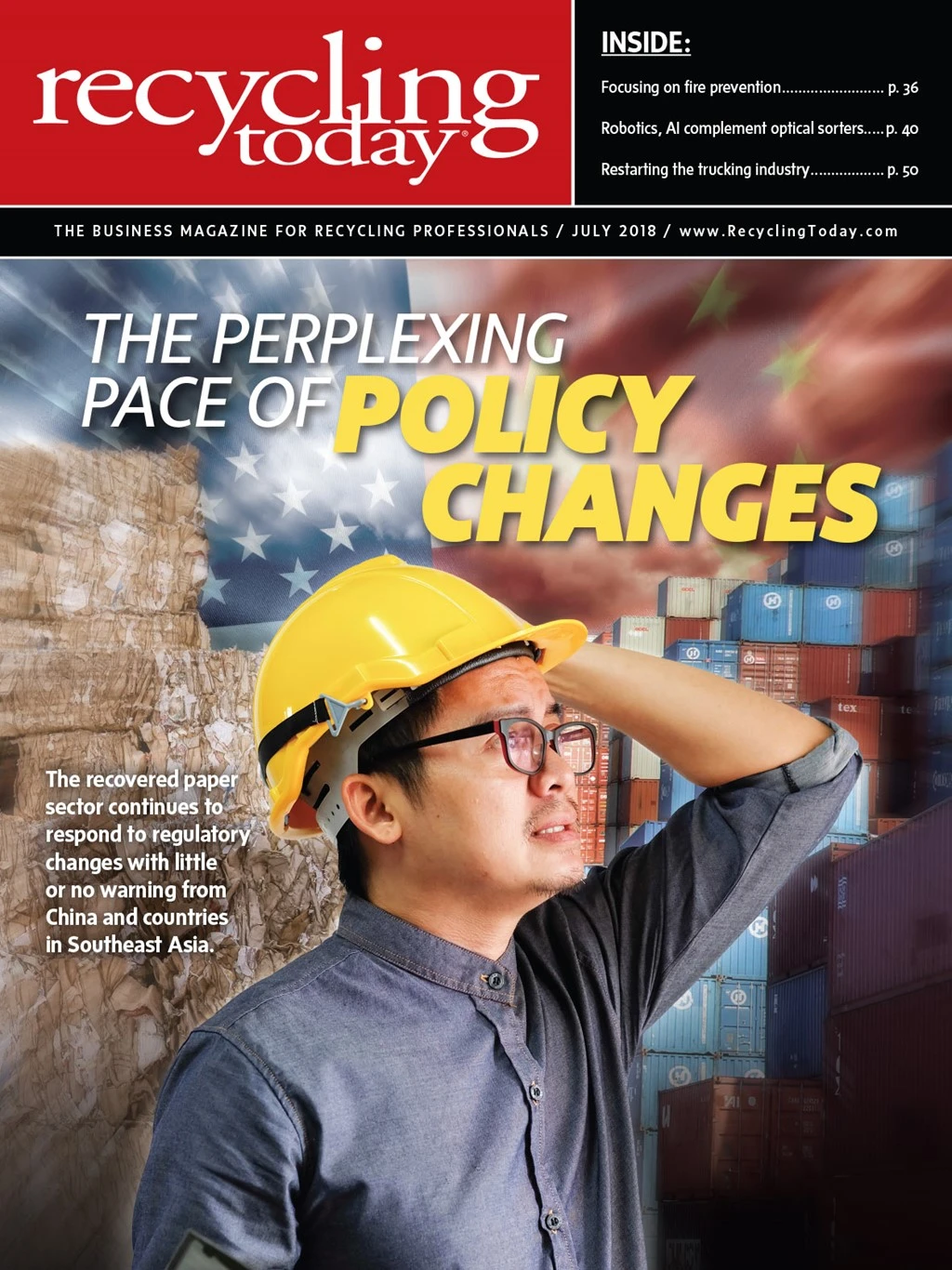
Explore the July 2018 RT Issue
Check out more from this issue and find your next story to read.
Latest from Recycling Today
- Astera runs into NIMBY concerns in Colorado
- ReMA opposes European efforts seeking export restrictions for recyclables
- Fresh Perspective: Raj Bagaria
- Saica announces plans for second US site
- Update: Novelis produces first aluminum coil made fully from recycled end-of-life automotive scrap
- Aimplas doubles online course offerings
- Radius to be acquired by Toyota subsidiary
- Algoma EAF to start in April