
Eriez expands Erie, Pennsylvania, plant
Eriez has completed what it describes as a major expansion to its Wager Road facility in Erie, Pennsylvania, approximately 15 miles from its world headquarters. The company says the expansion supports its strategic growth initiatives for global research and development (R&D), aftermarket repair and testing and recycling equipment technology. Eriez, which purchased the Wager Road building in 2011 and broke ground on this latest expansion in January of 2020, says the project is the largest investment it has made to date at this facility.
The company has added 38,000 square feet to the existing building, bringing the total square footage to 148,000. Eriez also added another manufacturing bay that has three distinct business purposes supporting key strategic initiatives, according to the company. Initially, a new Recycling Test Center will be established to provide large equipment demonstration testing capabilities, enabling full-scale evaluations of customer product streams.
Another section of the new manufacturing bay offers additional floor space for the Aftermarket Repair Center. The footprint of the new repair center will double in size as a result of this expansion, Eriez says. The final section within the new manufacturing bay will be a new R&D area that will support global product development programs.
This expansion also includes a new Electronics Lab that will house the company’s next-generation electronics product development activities. This new lab will include a main product test area, an electrical hardware development lab, a magnetics testing and materials lab and a software and circuit board development area.
Eriez – USA Vice President and General Manager Tim Gland says, “The expanded repair, testing, demonstration and R&D areas will allow us to complete even bigger projects and pilot tests, speed up and enhance product development activities and offer additional aftermarket repair capabilities with faster turnaround times.”
Eriez provides separation technologies that include magnetic lift and separation, metal detection, fluid recycling, flotation, materials feeding, screening, conveying and controlling equipment. Its equipment is used in the process, metalworking, packaging, plastics, rubber, recycling, food, mining, aggregate, textile and power industries.
Shred-Tech announces dealer agreement with Pronar
Shred-Tech, Cambridge, Ontario, has announced it has entered into an exclusive North American strategic dealer agreement with Pronar, a recycling machinery manufacturer based in Narew, Poland.
Shred-Tech is now the exclusive distributor for Pronar’s single- and double-shaft slow-speed primary shredders.
Pronar says it has grown exponentially and consistently over the last 30 years to be a leader in recycling, agricultural and municipal machinery manufacturing on a global scale. With more than 2,200 employees and seven factories and facilities totaling 574,000 square feet, Pronar reports that it sells more than 5,500 machines annually.
The company also is known for manufacturing and supplying pneumatic and hydraulic components for trailer axles and steel side wall profiles and for producing 60,000-wheel rims every month that are distributed globally.
Industrial Magnetics acquires Walker Magnetics
Boyne City, Michigan-based Industrial Magnetics Inc. has acquired Walker Magnetics Group Inc., which was founded in 1896 in Worcester, Massachusetts.
According to a news release from Industrial Magnetics, Walker Magnetics is North America’s “oldest industrial magnet manufacturer.” The company was founded on the invention of the electromagnetic chuck by Oakley S. Walker and has since grown into a provider of custom and standard magnetic products for work-holding, lifting, material handling, scrap magnets and separation applications.
“The acquisition of Walker Magnetics marks Industrial Magnetics’ next step in expanding our permanent, electromagnetic and electro-permanent magnetic technology and systems for industrial applications,” says Dennis O’Leary, chief business development officer at Industrial Magnetics. “It also broadens our industry-best roster of lift magnets and establishes Industrial Magnetics as a leader in the work-holding segment with a complete lineup of permanent, electromagnetic and electro-permanent magnetic chucks.
He continues, “With strong brand recognition and highly complementary products, we are excited about the opportunities to grow both businesses while maintaining our industry-best lead time, reliability and quality. Industrial Magnetics intends to be a thoughtful steward to the Walker Magnetics legacy, history and brand with continued investment in its long-term growth.”
Industrial Magnetics was founded in 1961 and provides permanent and electromagnetic solutions.
_fmt.png)
GK acquires Cyrus Schwingtechnik
General Kinematics (GK), a vibratory equipment manufacturer and system integrator headquartered in Crystal Lake, Illinois, has acquired German company Cyrus Schwingtechnik. Cyrus provides modular vibratory machines for conveying and screening technology.
According to details on the Cyrus website, the company was founded in 1976 and currently employs 25 people. Its website states that it creates “mechanical and system solutions in the field of vibration technology for foundries and the metallurgy, forging, recycling, raw material and commodity sectors.”
According to a news release from GK, the addition of Cyrus will complement its portfolio of vibratory solutions. The product range covers the foundry and forging sectors, the recycling industry, raw/base materials and the feed/food industries. GK says Cyrus will remain in Recklinghausen, Germany, and will operate as a separate brand under General Kinematics Europe.
“It is exciting to add this well-respected brand to our European organization,” says Thomas Musschoot, president of GK. “We have had great success combining the offerings of both companies in the past, so it made sense when the opportunity arose to build on that success as one integrated company.”
Davide Gado, managing director for Europe, the Middle East and Africa at General Kinematics Europe, says GK and Cyrus have worked together as partners and have been “friendly competitors.” He adds, “The relationship allowed us to become familiar with a group of very talented people, which is the heart of every company.”
Gado continues, “We grew to appreciate their portfolio of products. Cyrus’ offerings complement GK’s current product lines and allow us greater flexibility in our approach to different customers and industrial sectors.”
Michael Schulte Strathaus, managing partner of Cyrus, says, “I express my pleasure in the acquisition of Cyrus Schwingtechnik business unit by General Kinematics. The merger combines the heavy-duty technology of General Kinematics with the light- and middle-duty product range of Cyrus. It is the best solution out of two worlds and a professional win-win situation for all clients.”
In 2020, GK celebrated its 60th business anniversary.

Machinex supplies large-volume C&D sorting system
Plessisville, Quebec-based Machinex Technologies Inc. has supplied what it calls a turnkey recovery facility for construction and demolition (C&D) materials to USA Hauling & Recycling at a facility in Wilbraham, Massachusetts. USA Hauling began operating the facility in early 2021.
The objective for the Enfield, Connecticut-based company, which Machinex calls one of the largest independently owned and operated waste management companies in New England, was to process its own materials and obtain high purity levels in light of the rising cost of waste disposal.
“As a company, we have been processing construction and demolition materials for over 25 years. This new system allows us to expand our reach further into Massachusetts, helping our customers meet their own recycling goals, increasing recycling in our state and, most of all, having a positive impact on the environment by removing materials from the waste stream and reusing them in new products,” says Jonathan Murray, director of postcollection operations at USA Hauling & Recycling.
The 50-ton-per-hour system is designed to sort recyclables, such as cardboard, metal, wood, aggregates and fines from discarded construction and demolition materials.
The system includes an Action Taper-Slot vibratory finger screen, a Mach trommel screen and two cross-belt magnets. Finally, a CBI AirMax separator removes light materials from heavy ones. The ability to manually pick wood at multiple sorting stations makes recovery of a large quantity of wood possible, and the dense-out units “are excellent at removing lightweight contaminants and allowing for easy quality control of the heavy material,” according to Machinex.
“Machinex distinguished itself for its responsiveness and quick results with an impressive layout, thanks to its installation and startup teams, who finished earlier than anticipated,” Murray says. “We really appreciate Machinex’s work and flexibility to deliver the system ahead of time. The team at Machinex was a pleasure to work with from design through installation and startup.”
Get curated news on YOUR industry.
Enter your email to receive our newsletters.
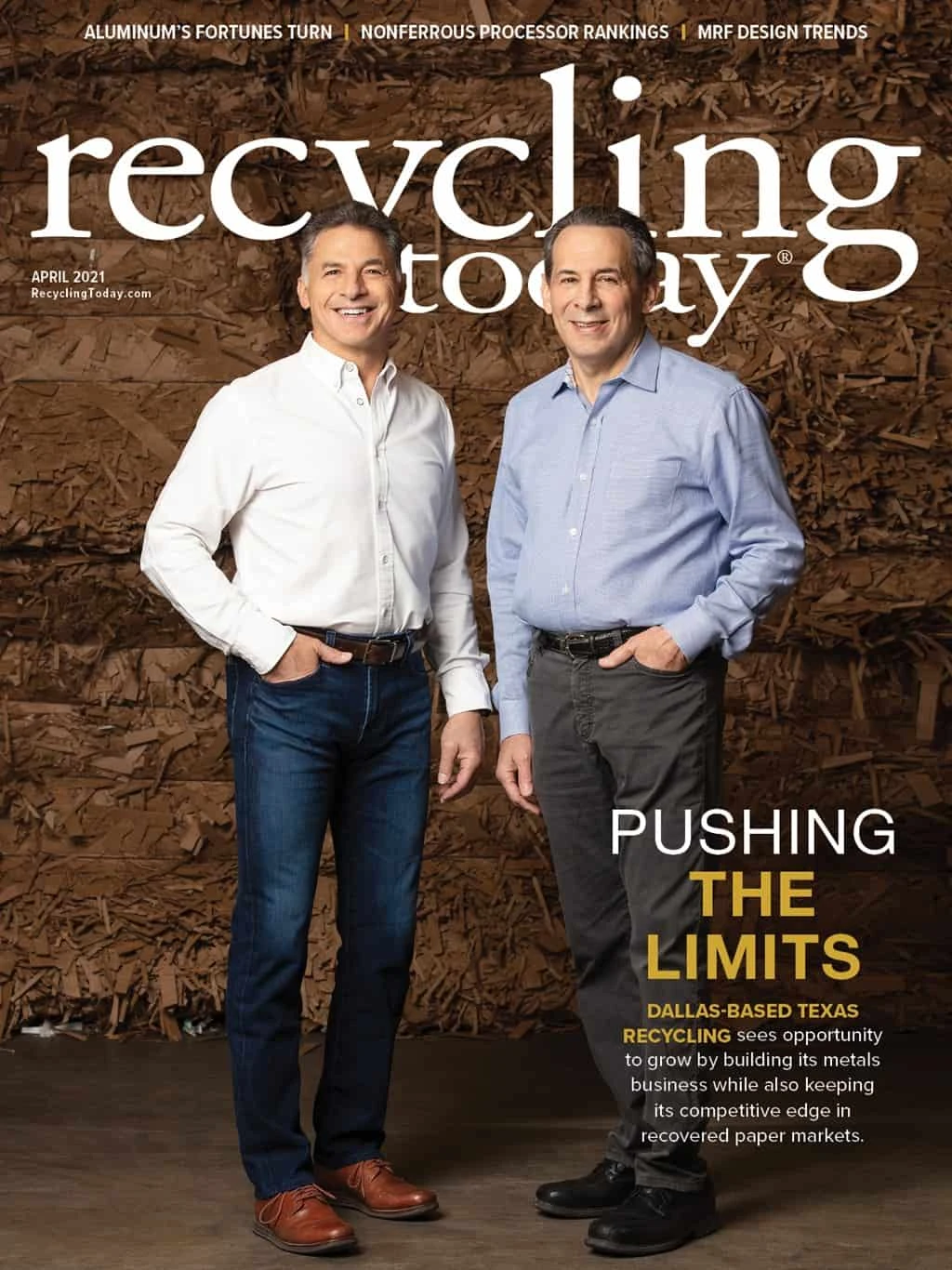
Explore the April 2021 Issue
Check out more from this issue and find your next story to read.
Latest from Recycling Today
- Green Cubes unveils forklift battery line
- Rebar association points to trade turmoil
- LumiCup offers single-use plastic alternative
- European project yields recycled-content ABS
- ICM to host colocated events in Shanghai
- Astera runs into NIMBY concerns in Colorado
- ReMA opposes European efforts seeking export restrictions for recyclables
- Fresh Perspective: Raj Bagaria