
Quality is king when it comes to the output material recovery facilities (MRFs) are being called on to generate these days. Faced with shrinking global end markets, MRF operators are using advanced technology to help cut contamination rates and improve the overall quality of their baled commodities. Two types of equipment that are on the frontline of this battle are optical sorters and artificial intelligence- (AI-) equipped machines that incorporate robotics.
While optical sorters have been used in MRFs for years, robotics
Choosing the right equipment
Adam Lovewell,
“It’s important to note that optical sorters and robotic sorters
Reardon says automating the QC process fully automates the fiber and container lines and allows MRFs to run all day without adding more labor.
“One should take into account all relevant operating parameters, including but not limited to feedstock quality and composition, throughput requirements (low, average and high throughout the day and year) and end-product quality requirements,” Egosi says. “From these, an assessment of the efficiency increase(s) and cost implications can be determined and a decision can be made on where or how to start [incorporating new equipment].”
He says operators should ask themselves the following questions before deciding to implement new optical sorters or robotics:
- What am I trying to achieve?
- What are the risks of doing nothing?
- What are the potential rewards (e.g., operational, financial) of making such a change?
- What conditions must be met to give the best chance of success?
Understanding differences and applications
_fmt.png)
The industry’s latest robotic sorters incorporate some of the same technology that has been used in optical sorters for years. While both systems feature high-speed, high-resolution cameras, three-dimensional sensors
Optical sorters are still 10 times faster than robotics (capable of roughly 600 picks per minute compared with the 60 picks per minute capacity of most robots), according to industry sources, while both are accurate. A primary difference between the two is that robotic systems use complex algorithms and more sophisticated programming that allow for improved sorting performance over time. In effect, these machines learn how to be more efficient the more they are used. Although robots can be programmed to be more sophisticated in the materials they pick, the speed differential between the two types of systems confines their use to certain roles in
Lovewell says operators should weigh the strengths of these machines when considering potential applications in their MRFs. “Optical sorters are best suited for fiber sorting and container sorting in medium- to high-volume plants,” he says. “Robots will be best suited for sorting containers in low-volume plants, maintaining quality control of ejected containers (from an optical sorter) on the container line and for the recovery of missed recyclables on the final residue recovery line.”
Because of their differences in capacity, operators must come up with a plan that best allows these machines to target materials in the recyclables stream for optimal efficiency.
“For a
Chris Hawn, the CEO of Machinex Industries’ U.S. division, Machinex Technologies, High Point, North Carolina, says, “Robots are never going to replace optical sorters by any means. When volume and picks are high, optical sorters are going to be the machine of choice.”
Hawn says robotic sorters are best employed in QC positions or to perform additional sorting tasks that optical sorters are not well-suited to perform. Because robotic sorters are not limited to analyzing and sorting by material composition and color as optical sorters are, they enable
“An optical sorter can identify material composition and color,” Reardon says, “which is important for higher volume sorting, but it can’t make six sorts in one location. The AQC can,” he says of BHS’ Max-AI AQC (autonomous quality control) unit, which is used to sort container streams following an optical sorter. “For example, in one location, the Max-AI AQC can identify and sort PET trays, aluminum, HDPE (high-density polyethylene), PP (polypropylene), mixed plastics and residue, also identifying and leaving a clean PET product.”
He also mentions the ability to sort PET thermoforms from PET bottles using robotics. “In another example, Max can tell the difference between a food-grade HDPE bottle and a nonfood-grade HDPE container,” Reardon adds.
Robotic sorters also can sort according to an adjustable hierarchy, Reardon and Hawn say.
“We work with our customer to determine what they need
Getting the most out of this equipment takes intricate planning in system design so as not to overwhelm it with
“For heavy volumes of a few related commodities (i.e., plastic containers),” Clark says, “the optical sorters would be located closer to the front end of the MRF, potentially following an initial separation of light materials versus heavy materials and/or two-dimensional items, such as fiber and paper, from three-dimensional items by other equipment, such as a screen or drum.
“In general,” he continues, “a robotic sorter would likely perform better anywhere in the MRF where there is some presorting to spread material evenly across the belt and remove oversize and bulky material or two-dimensional material like paper and foil that can obscure the targeted material(s).”
Whether to employ a robotic sorter is a question of labor availability and cost in the area the MRF operates, Hawn says. “Do you have the labor available and at what wage?”
Reardon says robotics
Weighing the options

Once an operator makes the decision that new equipment is needed, the process of shopping for the right solution begins. Although cost is a major factor that will influence an operator’s purchasing decision, it shouldn’t be the only consideration.
Clark advises reading up on system information via trade publications, inquiring about system performance from other operators and talking with experienced consultants and vendors.
“Allow companies to come into your facility and make an initial assessment, review data you may have on material volume, material changes and percent recovery and residue [and], then, request a written report,” Clark says. “That report should include
He suggests sending a representative material stream sample to potential vendors’ test facilities to gauge the equipment’s effectiveness. He also advises operators to visit facilities currently running the equipment under consideration to see how it operates.
Lovewell says it’s important to know the company you’re buying from when investing in equipment. He advises choosing providers that will be able to offer parts and service support throughout the life of the equipment.
Planning for the future
Equipment is always changing and becoming more technologically advanced. Although it is impossible to “future proof”
“It is easier said than done, but operators should always plan for future equipment,” Lovewell says. “If you do not have the capital to add optical sorters or robots during the initial design/installation phase, make sure you have adequate room to add down the road,” he says.
Because incoming material composition and output demands are ever-changing, Egosi advises choosing equipment and a site that allows flexibility.
“For new MRF builds, bigger is better. As technology advances and the input compositions continue to change, equipment retrofits and upgrades are always inevitable, typically within a 10-to-15-year period of time—often even sooner,” he says. “Allowing room for reconfiguration is a best practice.”
Egosi says upgrading existing MRFs can be challenging but not insurmountable. “Knowing your business is vital to making the best decision possible. If tonnage is expected to increase or remain static but the demand for higher quality bales is expected, greater separation and quality control efficiencies are an absolute must,” he says. “Investments made in operational efficiency, whether technological or nontechnical, will enable MRFs to manage materials effectively and efficiently under a variety of operating conditions.”
As optical sorters and robots become more sophisticated, MRFs will continue to realize greater purity and more opportunities for diversion, which is
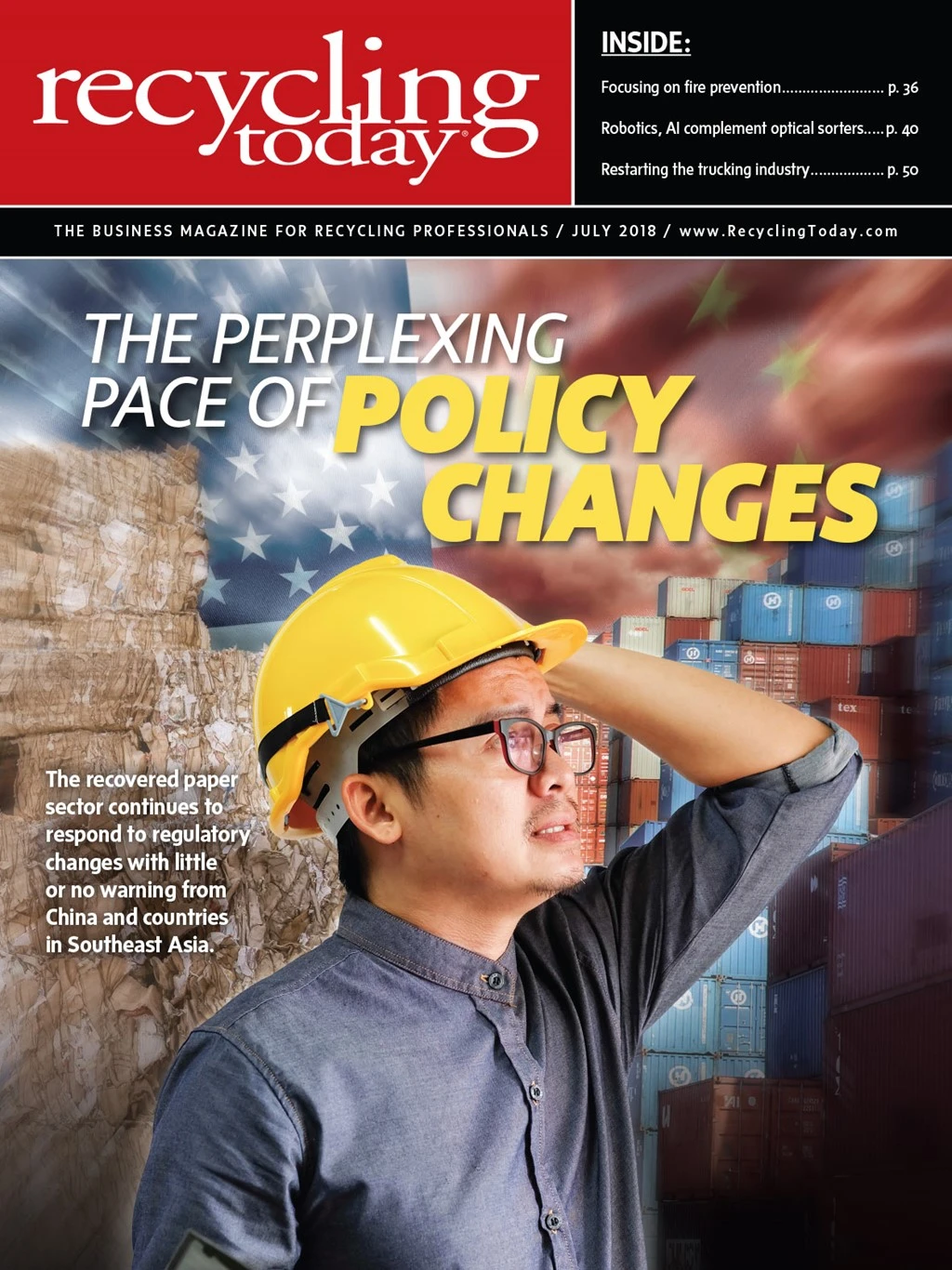
Explore the July 2018 RT Issue
Check out more from this issue and find your next story to read.
Latest from Recycling Today
- ReMA board to consider changes to residential dual-, single-stream MRF specifications
- Trump’s ‘liberation day’ results in retaliatory tariffs
- Commentary: Waste, CPG industries must lean into data to make sustainable packaging a reality
- DPI acquires Concept Plastics Co.
- Stadler develops second Republic Services Polymer Center
- Japanese scrap can feed its EAF sector, study finds
- IRG cancels plans for Pennsylvania PRF
- WIH Resource Group celebrates 20th anniversary