
1. Should the magnet be powered on when I am lowering for a lift?
This is a definite no. If the magnet power is turned on before coming in contact with the scrap pile, not only will it cause premature heat, but it will also prohibit the magnet from saturating the scrap pile, thus reducing lift.
2. After I drop my scrap magnet load into a rail car, truck or other transport vessel, would it be best to turn the magnet back on right away to get it ready for the next lift?
This is also a definite no. When a magnet is turned on, it is generating heat whether it is carrying a load or not. So, turning the magnet on will definitely increase heat, exceed the duty cycle beyond design parameters and it will eventually cause premature magnet failures.

3. Why is duty cycle so important when operating my magnet?
Duty cycle is time on vs. time off, and it is generally measured in 10-minute intervals. A magnet is designed to help dissipate the heat that it generates, but when you exceed the duty cycle of the magnet, its ability to dissipate heat is diminished. This also causes damage to the insulation. When the insulation is subjected to heat beyond its temperature rating, it may cause turn-to-turn shorts in the magnet windings, and this will often put the magnet on the road to premature failure.
4. Will excessive mechanical abuse affect the life of my magnet?
Yes, it certainly will. A magnet is built to endure the rough environment of scrap processing applications, but excessive mechanical abuse will eventually cause cracked welds or damage to other mechanical components of the magnet. A cracked weld or other damage can cause moisture to enter the magnet cavity, and this will cause damage to the insulation, which will certainly shorten the life of the magnet. In addition, mechanical abuse can also cause damage to the conductor, which is the most costly component of a lifting magnet.
5. What simple things can be done to extend magnet life?
Yes, there are many simple things that can be done to make your magnets run longer and avoid catastrophic failures. One of the most critical yet simple things that can be done are daily visual inspections. Identify possible areas of trouble by inspecting leads, chains, chain pins, lifting lugs, look for cracks in the case and bottom plate. Another thing that can be done is simply monitoring magnet amperage. Be sure your operators are trained to understand what happens when a magnet heats up, how that affects amperage and when to get your maintenance staff involved. A magnet meter package in the cab is also a very useful tool here.
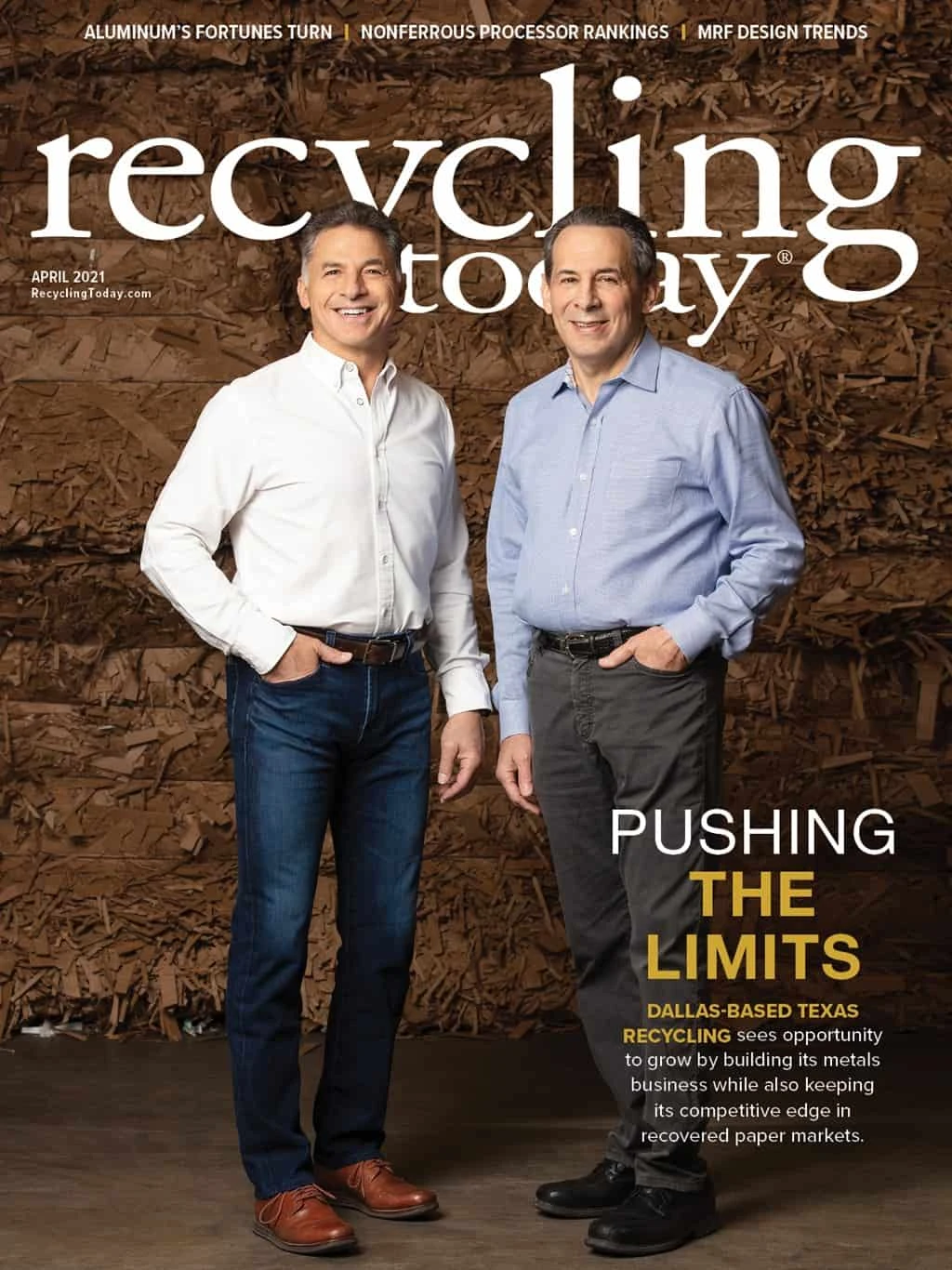
Explore the April 2021 Issue
Check out more from this issue and find your next story to read.
Latest from Recycling Today
- LumiCup offers single-use plastic alternative
- European project yields recycled-content ABS
- ICM to host colocated events in Shanghai
- Astera runs into NIMBY concerns in Colorado
- ReMA opposes European efforts seeking export restrictions for recyclables
- Fresh Perspective: Raj Bagaria
- Saica announces plans for second US site
- Update: Novelis produces first aluminum coil made fully from recycled end-of-life automotive scrap