
In late April, nearly 12,000 waste and recycling industry professionals and 600 exhibitors gathered in Las Vegas for WasteExpo 2018, where they looked to the future of the industry. The event, organized by information, event, commerce
Passing it down
A considerable number of waste and recycling companies are run by families who pass the responsibilities of owning and operating their businesses onto the next generation. The panel discussion A Family Affair: Transitioning to the Next Generation addressed what families can to do ensure a clean transition between generations.
Brian Jongetjes is the president of John’s Disposal, Whitewater, Wisconsin. His son, Dan, is the company’s general manager.
While it can be difficult to step back and let the next generation take over, Brian said, it’s important to be able to listen to a successor and to take him or her seriously. After he and his brother took over John’s, Brian said his dad wouldn’t adhere to instructions they gave him. “I want to make sure my kids tell me what to do,” he added.
Dan emphasized that family members should work from the bottom up as part of the crew rather than going straight to the top. In the beginning, he said, he took the “rough jobs,” such as cleaning garbage cans and the office. This experience allowed him to respect the work his employees put in while also earning their respect.
Joe Garbarino of Marin Sanitary Service, San Rafael, California, also “started at the very bottom of the can,” he said. “I was always a proud garbage man,” Joe added. “You pass that on.”
“You need to work hard and gain the respect of your employees the old-fashioned way,” said Patty Garbarino, Joe’s daughter and president and CEO of Marin Sanitary Service.
The Garbarino family emphasized the importance of passion and experience over
Patty, who is a past-president of the California Reuse and Recycling Council, implemented the council’s Next Generation Course. The course addresses the history and evolution of the solid waste industry, effectively managing day-to-day operations and human resources, financing, risk management and safety and leadership topics. She said several hundred participants have graduated from the program so far.
The
Robots on the rise
In addition to leadership, another factor that affects the success of a recycling company is the efficiency of the capital equipment it employs.
Given today’s difficult market conditions for some postconsumer recyclables, using technology to identify the composition of the feedstock that is coming into material recovery facilities (MRFs) can helps operators create cleaner end products more cost-effectively, said speakers in the session titled Rise of the Robots: The Role of Artificial Intelligence (AI) in the Waste Industry.
Speakers pointed to various reasons to use robots and AI in MRFs, including reliability, high purity and consistent and accurate identification of targeted materials.
“It’s important we realize the importance of artificial intelligence in recycling,” said speaker Charles Yhap, founder
CleanRobotics’ flagship product, the TrashBot, uses advanced robotics and AI to sort recyclables from waste, increasing recycling yield and improving quality by reducing contamination, according to the company.
Matanya Horowitz, co-founder
AMP’s two-part system consists of a robot and a vision system. The system is installed over a conveyor belt and can learn to recognize all the materials that pass through
Session speakers agreed that the goal of this technology is to bring MRFs some of the capabilities and control
Rich Reardon, managing director of Max-AI for Bulk Handling Systems (BHS), Eugene, Oregon, described the work it took to build the neural network, or the library of memory recognition, used in the company’s robotic and AI technology. “You can’t go to your local Walmart and buy a neural network,” Reardon said.
BHS had sold more than 50 units, with seven installations completed, as of late April.
“It’s just the beginning for robots,” Horowitz said, adding that picking robots will evolve over time.
Reardon and Horowitz said their robots have a 95 percent accuracy rate, while CleanRobotics’ Yahp said Trashbot is 85 percent accurate.
Keeping safe
Recyclables must arrive at
With these issues in mind, panelists addressed how haulers could work more safely during the Best Practices for City Collection session.
Julia Kite, director of strategic initiatives at the New York City Department of Transportation, said its Vision Zero program has been instrumental in helping cut down on collection-related driving injuries and fatalities.
Vision Zero, which first was implemented in Sweden, was adopted in New York City under Mayor Bill de Blasio’s administration four years ago. Kite said the program has been successful by changing the way people relate to collection accidents.
Vision Zero is a multidisciplinary policy that includes expanded enforcement of dangerous moving violations, such as speeding and failure to yield to pedestrians; new street designs; public outreach and communication campaigns to better educate citizens; and harsher legislative penalties for dangerous drivers.
Since New York City adopted the Vision Zero initiative, Kite said accidents and fatalities have fallen sharply in the city.
“In the four years that Vision Zero has been the official policy in New York City, we’ve made phenomenal progress,” she said. “While the rest of the country has seen an increase in road deaths, particularly in pedestrian deaths, New York City has found a 28 percent decline in all fatalities and a 45 percent decline in pedestrian fatalities. So, what we’re doing is working, and, more importantly, we know other cities can do this, too.”
Liam Tanelli,
“I think the last two years, the national driver shortage has been getting louder and louder, and I think everyone in the industry has felt the pain of that. I think this has a direct correlation between safety and safety procedures,” he said.
The reality of this shortage is that waste companies are more likely to hire drivers with spotty driving records to keep up with demand, Tanelli said. To help mitigate this issue, Voyager has placed a renewed emphasis on driver training, he said. The company also has reinvested in equipment, such as disc brakes, tire monitoring systems and reverse flood lights, to help cut down on preventable accidents.
John Sliwicki is vice president of risk management at Morton Grove, Illinois-based Lakeshore Recycling Systems, a provider of recycling and waste diversion services. He said comprehensive coordination among the industry, government, associations and the public was needed to change the narrative on safety in the collection industry.
“I think everyone here gets it; we can put in [onboard cameras], we can do data analysis, we can do regression modeling, but collaborations and industry outreach are really key to getting the issue of safety, crashes and fatalities addressed,” he said.
As these WasteExpo sessions indicate, waste and recycling industry executives have no shortage of important topics to consider as they plan for the future of their operations.
Get curated news on YOUR industry.
Enter your email to receive our newsletters.
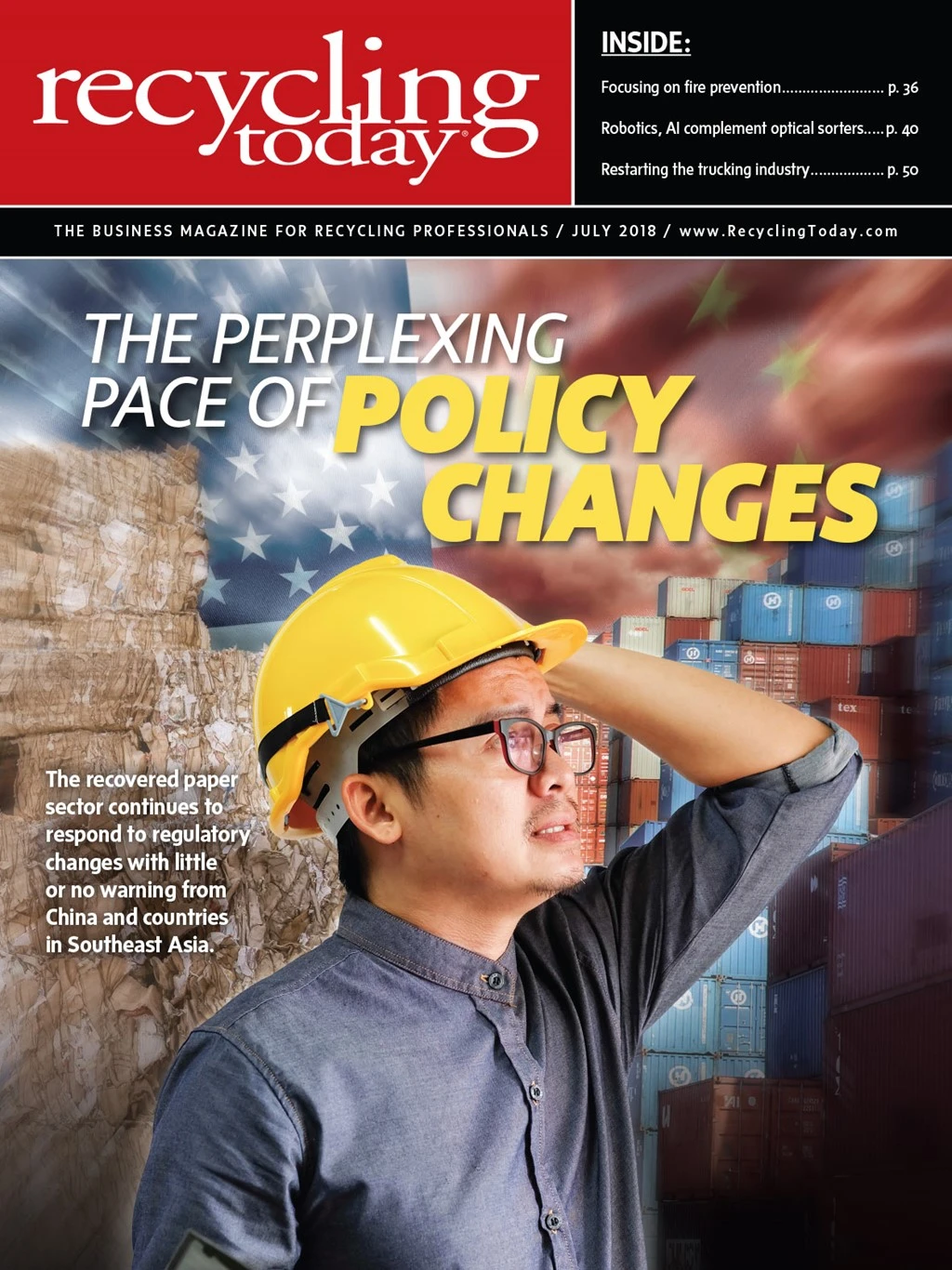
Explore the July 2018 RT Issue
Check out more from this issue and find your next story to read.
Latest from Recycling Today
- Astera runs into NIMBY concerns in Colorado
- ReMA opposes European efforts seeking export restrictions for recyclables
- Fresh Perspective: Raj Bagaria
- Saica announces plans for second US site
- Update: Novelis produces first aluminum coil made fully from recycled end-of-life automotive scrap
- Aimplas doubles online course offerings
- Radius to be acquired by Toyota subsidiary
- Algoma EAF to start in April