
Photo courtesy of Aurubis
Wood Mackenzie, based in London, says the world cannot decarbonize through electrification without the use of copper, but repositioning critical minerals supply chains outside of China would result in inefficiencies that could increase the cost of finished goods and delay the energy transition. The country dominates copper mining, downstream processing (smelting and refining) and semi manufacturing; however, with demand for copper expected to rise by 75 percent to 56 million metric tons by 2050, substantial investment will be required to enable new supply chains outside of China.
According to Wood Mackenzie's “Securing copper supply: No China, no energy transition,” replacing China’s copper smelting and refining capability to meet the rest of the world's demand would require nearly $85 billion.
“A scenario without China for the copper supply chain would require a substantial increase in processing capacity to meet energy transition targets,” Nick Pickens, research director, global mining at Wood Mackenzie, says.
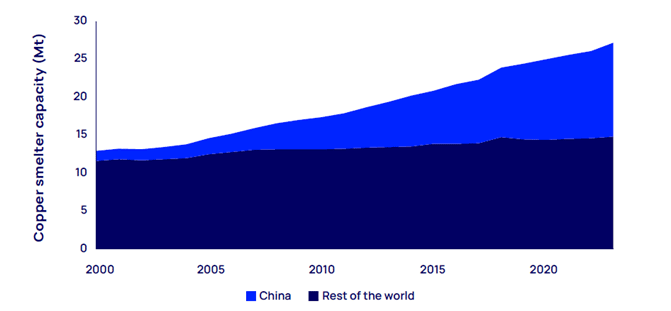
He adds that Wood Mackenzie projects an copper demand outside China will grow by 8.6 million metric tons over the next decade. “This demand represents 70 percent of smelter capability and 55 percent of fabricator capacity in the rest of the world. As governments and manufacturers aim to diversify away from China, it is crucial to consider the entire supply chain, not just mining operations.”
The global copper supply chain is a complex system comprising mining, smelting and refining, semifabricating and manufacturing of finished goods, the company says. Copper flows from raw material extraction in the Americas and Africa to downstream processing and manufacturing, predominantly in China. The country’s substantial investments in downstream processing and semi manufacturing sectors present significant challenges to global copper supply security.
According to the report, China has accounted for 75 percent of global smelter capacity growth since 2000 and now controls 97 percent of global smelting and refining capacity, contributing more than 3 million metric ton of production and nearly $25 billion in investment. The country also has added nearly 11 million metric tons of copper and alloy capacity since 2019, representing roughly 80 percent of global additions. Approximately two-thirds of these facilities produce wire rods, giving China half of the world’s fabrication capacity, with further expansion underway.
Zhifei Liu, managing consultant, copper markets, at Wood Mackenzie, says, “China's copper smelting industry has undergone significant evolution. In the 2000s, a drive for stricter environmental and efficiency standards led to the modernization of smelting capabilities.
“Today, Chinese smelters are low-cost and meet high environmental standards, particularly in sulphur dioxide capture, making them highly competitive.”
Pickens added that semifabricators outside of China, especially in Europe, face challenges from lower utilization and higher operating costs. Carbon emissions regulations, such as the European Union’s Carbon Border Adjustment Mechanism, could reduce competitiveness by imposing higher taxes on the European copper industry without providing equivalent benefits. Additionally, U.S. government incentives such as the Inflation Reduction Act might not ensure the long-term sustainability of the industry.
RELATED: EU metal distributors worry about the ‘b’ in CBAM
The report highlights significant shifts in the global primary copper smelting landscape, with new facilities set to come online this year outside China. India is launching a custom smelter, Indonesia is adding two integrated smelters and a new smelter in the Democratic Republic of the Congo is expected to be completed by 2025, primarily driven by Chinese investment. Wood Mackenzie says these additions will add 1.6 million metric tons to global smelting capacity, the largest increase outside China in decades.
However, North America and Europe have no plans for new primary smelting capacity, Wood Mackenzie says, noting that the U.S. is adding scrap-based secondary production, citing an investment in Georgia as one example.
Aurubis AG, headquartered in Germany, broke ground in 2022 on its first large secondary smelter in the United States in Augusta, Georgia. That site will produce 180,000 tons per year.
In a previous interview with Recycling Today, Inge Hofkens, chief operating officer, multimetal recycling, at Aurubis, said, “The world needs metals such as copper for our mobile phones, EV [electric vehicle] batteries, cables, solar panels [and] wind energy parks. But, at this point, current supply cannot meet demand, and the U.S. in particular lacks recycling processing capacities. Recycling helps strengthen and safeguard supply chains. It is the basis for a fully independent and renewable economy. With Aurubis’ facility in Augusta, we are transitioning to a true sustainable economy.
“Aurubis Richmond will be a game changer. With our state-of-the-art recycling activities in our modern plant, we will increase the availability of critical and strategic raw materials,” which largely will come from printed circuit boards (PCBs) and cables.
Other investments in secondary copper production in the U.S. include Ames Copper Group in North Carolina, which can produce 50,000 tons of 99.7 percent pure copper anode annually, and Germany—based Wieland’s new smelter in Kentucky that has the capacity to produce up to 85 million pounds of low-carbon copper annually, with room for expansion.
Wieland also is increasing its recycling and melting capacity in Europe with an investment of 80 million euros ($85.8 million) at its Vöhringen, Germany, facility.
Wood Mackenzie’s report notes that scrap likely will play a more significant role within the market if copper is to meet the environmental challenges the world faces.
“We have begun to witness an acceleration in the direct use of scrap at the semifabricator level, especially for the manufacture of copper foil in the world outside China. Copper producers and consumers are also either developing standalone secondary capacity or increasing the share of scrap into their raw-material feed where possible, given the challenges associated with primary supply.”
“While copper supply risks can be mitigated and some rebalancing has begun in various countries, the scale of China’s dominance in the supply chain means complete replacement is unfeasible,” Pickens says. “The introduction of new processing and fabrication facilities may result in higher costs and delays in the energy transition.”
He adds that financing these investments also presents hurdles, noting that resistance to new smelter projects on environmental and social grounds is particularly strong in Europe.
“Pragmatism and compromise will be essential to achieve net zero goals without imposing excessive costs on taxpayers," he says. "Easing global trade restrictions could be one necessary concession.”
Get curated news on YOUR industry.
Enter your email to receive our newsletters.
Latest from Recycling Today
- Fenix Parts acquires Assured Auto Parts
- PTR appoints new VP of independent hauler sales
- Updated: Grede to close Alabama foundry
- Leadpoint VP of recycling retires
- Study looks at potential impact of chemical recycling on global plastic pollution
- Foreign Pollution Fee Act addresses unfair trade practices of nonmarket economies
- GFL opens new MRF in Edmonton, Alberta
- MTM Critical Metals secures supply agreement with Dynamic Lifecycle Innovations