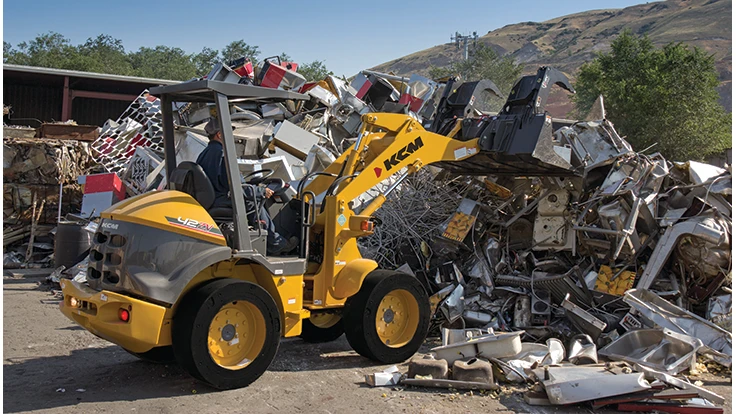
Not too big, not too small but just the right size. Finding a wheel loader that is the right size for your needs is better than a bowl of porridge any day.
Define the application
The first priority when buying a wheel loader is defining the application, says Sam Crawford-Shelton, marketing manager for United States-based KCMA Corp. “What will the wheel loader be required to do?” is her first question.
“Spend money upfront on a correctly optioned loader,” Crawford-Shelton advises. “Cheap initial prices will come back to haunt you very quickly.”
Caterpillar’s Product Application Specialist Rich Knudson says, “When considering the size and type of machine, one should consider the Golden Rule ... let the application and work to be completed define the work tool,” he says. “The work tool will determine the machine size.”
Application and work considerations include production requirements, such as tons per hour or per day, lift height and reach, support work required, yard size, size of haul vehicles or hoppers and the sizes and types of materials to be moved.
Don’t just think about today, either. “One should include any future production changes or growth when sizing a machine,” Knudson says.
Take a close look at the management of an objective material and whether the loader could be used for conveyance, loading, stockpiling, etc. “This also goes to the attachment type and capacity desired,” Crawford-Shelton says.
“Look at functionality, for sure,” advises Juston Thompson, product specialist for wheel loaders at Hyundai Construction Equipment Americas, based in Atlanta. “What do you want out of the machine?”
Determine if the main use is loading, stockpiling, sorting, hopper feeding or as a haul vehicle, Knudson says. “Helping the dealer answer these questions will help the customer with correct right-sizing,” he says.
“All of the above factor in the decision and are part of the application aspect of our Golden Rule,” Knudson says.
In addition to tons handled, look at typical work cycles, what type of floor the machine will be working on and how many hours per day it will be active.
Next, Crawford-Shelton suggests looking at limiting factors imposed by the job site, such as work area size (and the related need for machine maneuverability), bunk or chute access, including bucket/machine widths and heights, bins, hopper or truck dump height requirements.
Operator comfort also is an important consideration. “Look at operator comfort to maximize productivity both of the machine and the person,” Thompson says. “You want to keep the operator as productive as possible.”
Be sure the seat adjusts to operators of many sizes. It is nice if the loader controls are integrated with the seat so the joystick or lever moves up-down and in-out as the operator adjusts seat height.
Choose your options
Manufacturers also offer a variety of options. Extended-reach units, for example, allow a higher dump height and longer reach when dumping scrap into a truck.
Specialized forks, buckets and grapples also are available. Auto shredder operators will want a unit equipped with a longer set of forks so they can get under a car lengthwise to move the bundle.
“Determine whether you need a third function for special uses,” Thompson says. Know how that function is controlled—is there an added lever, or is the control on the joystick?
Every supplier agrees on the value and necessity of proper guarding. Most original equipment manufacturers (OEMs) offer rugged options that address the extreme environment in recycling yards.
Crawford-Shelton says a recycler should look primarily at guarding and cooling system anti-clogging measures.
“Recycling applications demand a full guarding package, work tools and tires that will help keep the customer’s cost lower,” Knudson says.
Among other options to consider are the ability to limit tire spin, reversing fans and debris-resistant cooler cores, he says.
Crawford-Shelton emphasizes the need for factory installation of the selected options. This includes taking delivery on a machine with the proper tires and buckets, properly positioned guarding, radiators fit for the job and fire suppression.
“Your salesman’s knowledge and like-customer referrals can help equip a loader properly,” she says.
Whether to multitask
“Multitasking one loader makes sense in a lighter-use application,” Crawford-Shelton says. Things like couplers with standard and large buckets and grapples can demonstrate versatility.
Still, be careful when doing so. “When recycled product has higher weight or abrasive characteristics, a properly designed bucket is better,” she advises.
In operations that heavily use their loaders, two or more machines may be best, Crawford-Shelton advises. “You need at least two machines for redundancy. If one machine goes down, work doesn’t stop.”
“A larger machine with a smaller support machine is sometimes necessary,” Knudson agrees. He says the decision depends on the size of the yard and capital the recycler has to work with.
“We find many customers currently try to get by with a loader to handle different jobs or support work,” Knudson continues. Still, he adds, “If it is a large yard with a lot of required tonnage, multiple machines need to be considered.”
Lifetime performance
The lifetime of a wheel loader will depend on the yard using it. Major factors that affect a loader’s lifetime include service and maintenance practices, operator technique and machine environment.
Sources say owners should keep track of operational costs and make repairs before failure occurs. “As the hours build and repair costs start to build, that is a good replacement indicator,” Knudson says. Then it is time to decide whether the cost to repair or rebuild is offset by the buy-back value and the capability of a new machine and its possible production increases.
In a typical recycling application, a wheel loader’s lifetime probably runs 10,000 to 15,000 hours. By avoiding abuse and performing routine maintenance, including using quality maintenance products, yards can extend the life of any machine, suppliers say.
“Most Caterpillar machines are designed to rebuild so that the owner can have multiple lives with one machine,” Knudson says. He has seen machines with more than 20,000 hours performing well in the field.
However, when downtime accumulates, it is probably time to look at replacing a wheel loader.
“An hours lease is a good way to acquire a machine,” Thompson says. Because most recycling operations have their business ups and downs, a lease allows a company to expand as business fluctuates and to keep the fleet fresh.
Much depends on the replacement thought process of the owner. Typically, machines spend their entire lives in this environment, Knudson finds. When replaced, an older machine goes to a smaller site or becomes a support machine.
Latest from Recycling Today
- PCA reports profitable Q1
- British Steel mill subject of UK government intervention
- NRC seeks speakers for October event
- LME identifies Hong Kong warehouses
- Greenville, Mississippi, launches aluminum can recycling program
- Cotton Lives On kicks off 2025 recycling activities
- Georgia-Pacific names president of corrugated business
- Sev.en Global Investments completes acquisitions of Celsa Steel UK, Celsa Nordic