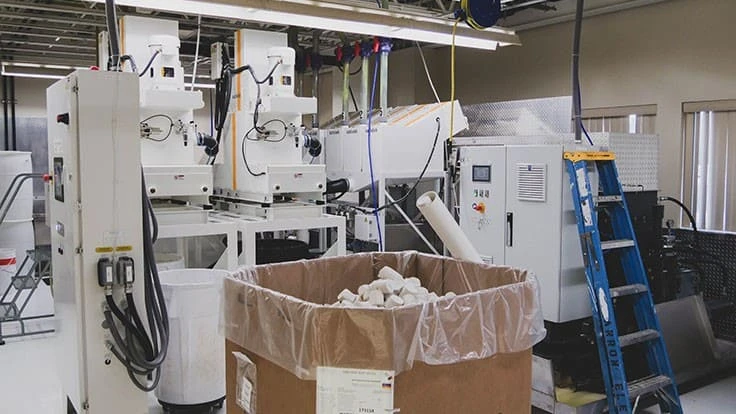
Photo courtesy of Weima
The city of Peoria, Illinois, is home to eyeglass manufacturer Maui Jim, which is known for its fashion-forward approach to sunglasses and prescription eyewear.
The company’s sustainability goals increase the value of its products to modern consumers as Maui Jim has taken steps to implement green practices during production and recycling initiatives for its end-of-life products.
Manufacturing byproducts
The process of creating custom lenses involves loose, airy scrap and cutting fluid. Each lens starts out as an 11-millimeter-thick piece of plastic that is machined and polished to the correct shape and thickness.
“As we start the whole process of making a pair of prescription lenses, they go into what we call an orbit lens generator,” Paul Ponder, vice president of prescription manufacturing at Maui Jim, says. “It creates swarf as it cuts that lens down to prescription shape and thickness. That swarf is flushed out with a fluid, used to cool the lens during the cutting process. It is also used as a wetting agent to flush it through the evacuation tubes. That fluid, which is taking the waste out, is cleaned back up and then comes back to the machine for reuse.”
Bazell Technologies has worked with Satisloh to provide the best-in-class coolant delivery equipment that Maui Jim uses to generate lenses. The engineers at Bazell worked with Weima, a German company with a U.S. sales and service office in Fort Mill, South Carolina, to select the right briquette press for the job—in this case, a Vario model—to compress the lens swarf and separate the cutting fluid for reuse.
The shavings, once they have been separated from the cutting fluid, are then conveyed from the cleaning unit to the Weima briquette press. The machine sits in its own designated space just off the production floor. Its footprint is minimal, but its presence in the process makes it possible to recycle the fluid and the swarf.
“It takes the processing of the debris off the production floor and saves space,” says Paul Dick, president and managing director of Bazell Technologies, Concord, California. “This allows space for more lens generators on the production floor.”

Briquetting benefits
With 12:1 compaction rates, Maui Jim saves space by processing scrap created during production shifts instead of storing it in its original form. The briquette press compresses these shavings into round, puck-shaped briquettes that are then picked up by a recycler to be transformed into postconsumer resin, or PCR, and integrated into other material streams.
Maui Jim found that the cost for the recycler to pick up this scrap was comparable with the landfill fees they would accrue. The value of this landfill diversion added to the reasons why Maui Jim opted to recycle this material instead.
Recycling partners
Maui Jim’s recycling efforts don’t stop there. The lifetime warranty on each pair of Maui Jim glasses extends to lenses and frames. Each time a pair of glasses is sent in for minor repairs, the frames and/or scratched lenses are also picked up by a recycler to be made into new things. The consumer will receive a pristine pair of glasses, and the damaged frames or scratched lenses leave the facility to be given a second life.
“Certainly, we want to be environmentally friendly, doing everything we can to keep anything from going to a landfill,” Ponder says. “All our lens waste, all our frame waste, any defects or rejects—it’s all recycled. Our frame designers are always looking at ways to be environmentally friendly.”
Latest from Recycling Today
- ReMA opposes European efforts seeking export restrictions for recyclables
- Fresh Perspective: Raj Bagaria
- Saica announces plans for second US site
- Update: Novelis produces first aluminum coil made fully from recycled end-of-life automotive scrap
- Aimplas doubles online course offerings
- Radius to be acquired by Toyota subsidiary
- Algoma EAF to start in April
- Erema sees strong demand for high-volume PET systems