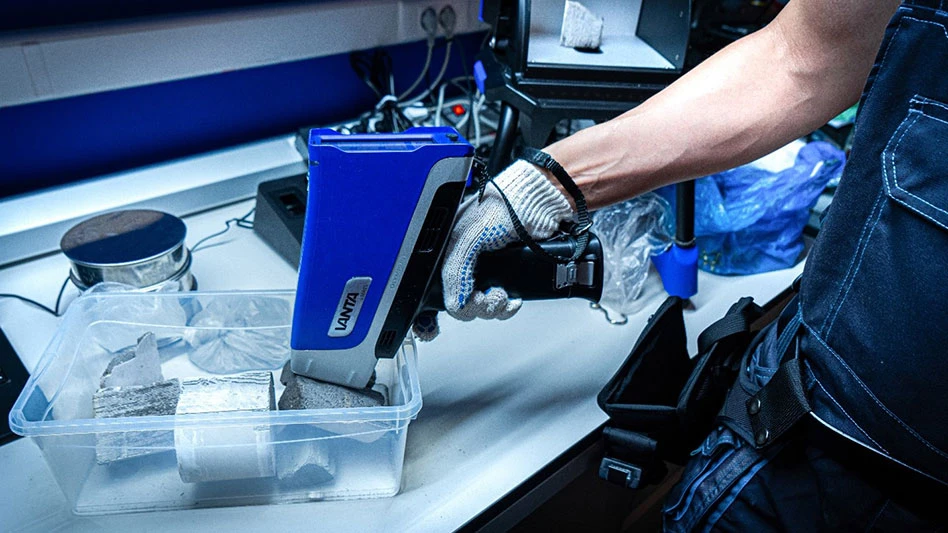
Photo courtesy of Evident Scientific
As demand for electric vehicles accelerates globally, so does the need for high-performance lithium-ion batteries (LIBs).
While LIBs play an important role in the move to more sustainable energy sources, they need to be responsibly managed at end of life. Properly recycling batteries promotes a circular economy where battery materials are kept in use to reduce waste and pollution. Extracted materials can be remanufactured into new batteries or used for other applications, reducing the need to mine raw materials to be used in new production. Portable X-ray fluorescence (XRF) technology can aid in the effective recovery of valuable metals from end-of-life batteries.
Many technologies use LIBs as a power source. Analysis suggests the global market size will grow to roughly 88 billion by 2027, according to AIMS Clean Technologies and Recycling Vol.1, Issue 2. The automotive industry is one of the leading commercial drivers of the increased usage of LIBs. Every car manufacturer has a line of electric vehicles (EVs) hitting the road in the next few years if they aren’t on the road currently. Portable electronic devices such as laptops and cellphones make use of LIBs for power as well. It’s safe to say that LIBs are ubiquitous in society and will play an even greater role in the future.
The downside to LIBs is that—like fossil fuels—they are made from finite resources, including cobalt, nickel, manganese and lithium (Li). The good news is that these minerals can be recycled, and this is the key to sustainability. Unlike fossil fuels, which are converted into carbon dioxide and water during a combustion reaction, most of the minerals found in batteries are not chemically altered, so they can be extracted and Freprocessed for reuse. Methods to recycle these materials will be paramount to sustaining the industries emerging from the battery boom. The major challenge in recycling is the efficient reprocessing of spent batteries.
Challenges in battery recycling
No set standard has been established for battery manufacturing, leading to a wide variety of battery designs and battery materials on the market. Some batteries are optimized for power density, others for energy density and others need to have a fine balance between both. This variety means the chemical components used in the batteries will be vastly different depending on how they are being used. The chemistry of the battery material guides the best way to process it during recycling.
The battery material that gets recycled is commonly called black mass, and it is a matrix of the cathode active material and the anode active material. The main elements in black mass are graphitic carbon, lithium, cobalt, nickel, manganese, iron and aluminum.
The most practical way to separate the components depends on cost and the potential for excess waste. Two common methods—pyrometallurgical and hydrometallurgical—have pros and cons. The pyro method involves burning the black mass, so the unwanted materials burn away, leaving behind the desirable metals. This is counterintuitive to the concepts of reusable and renewable since the goal is to save as much as possible and mitigate the amount of CO2 being released into the atmosphere. The hydrometallurgical method also can add to the carbon footprint by generating wastewater that must be processed.
Using XRF in battery recycling
XRF is a tool used to accurately and precisely provide the material chemistry of a sample with minimal sample preparation. Most systems reliably measure elements from magnesium to uranium in seconds. However, Li and carbon are two major constituents of LIBs that cannot be measured directly by XRF.
As a tool, XRF is proven to readily identify and sort materials to specific grades or chemistries in the metals recycling industry. Hand-held XRF is widely used in the recovery of precious metals (e.g., platinum, palladium and rhodium) from spent catalytic converters. XRF will do the same thing in the battery recycling process, offering the capability of grading different battery materials that come into facilities. This offers several benefits. First, if you are shipping loads to the reprocessing plant, knowing the analysis—and hence, the value—of each batch helps ensure you are properly paid for the true metal content. If you’re receiving known or unknown batches of black mass, XRF analysis allows the processor to blend batches for optimal recoveries. Finally, knowing the material chemistry helps ensure the materials go through the proper chemical process as many of the extraction methods are sensitive to slight changes in chemistry.
Some existing analytical techniques used in battery recycling require the materials to be transformed from a solid phase to an aqueous phase through destructive digestion. After digestion, not all the material could go into solution. If everything does make it into solution, some elements will be in high concentrations and others in low concentrations. Most of the analytical instruments used in this process are quite sensitive and only can handle very dilute concentrations, requiring a lot of dilution in conducting aqueous measurements. XRF, on the other hand, can analyze materials in their solid state with no requirement for dilutions and with minimal sample preparation. The technique also is nondestructive, so sample materials can be retained indefinitely. The main requirement is that the solid material is as homogeneous as possible. If the elements are present in the sample at detectable limits, XRF will quantify them.
Figure 1 shows two examples of the chemistry that can be displayed on an XRF when analyzing black mass from LIBs. The display is easy to understand, with the concentrations of elements going from high to low. The standard deviation of each element’s calculation also is represented in the display window. A test like this can take as little as 15 seconds. Increasing the XRF analysis time can further increase the accuracy and precision of the results.
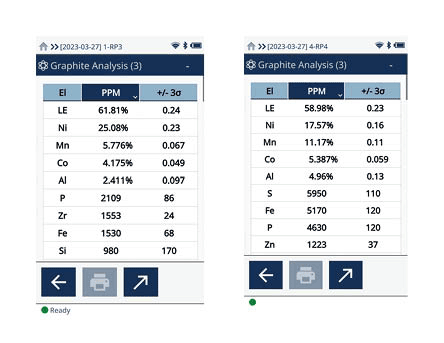
In a high-paced, high-throughput environment such as the recycled materials processing industry, making dynamic changes in real-time makes processes more efficient. For chemical analysis, no other system requires as little from the user while giving accurate, precise results as XRF. An XRF analyzer provides lab-quality data in minutes with minimal sample preparation. In a continuous workflow, in-line XRF can be used to monitor concentrations of elements in real time as material moves throughout the process. Speed and ease of use make XRF a valuable analytical and production tool. Used properly, XRF analyzers are very safe because the X-rays are low intensity, focused and only generated when measurements are taking place.
Today, many companies are using XRF for black mass applications. Because of their versatility, XRF analyzers also are used on the front end of battery manufacturing to provide anode and cathode composition, film thickness and a variety of other chemical analyses significant to battery engineers. If you want to know the chemical composition of a material, there is a good chance XRF can provide it accurately and precisely.
Like a Swiss Army knife, multiple applications for XRF are available in any given industry. For battery recycling, XRF can be an invaluable tool for successful battery recycling operations.
Marcus S. Johnson, Ph.D., is an XRF application scientist with Evident Scientific, based in Waltham, Massachusetts, and a member of the pre- and postsale support teams. He earned a Ph.D. in physical chemistry from The University of Alabama, becoming an expert on surface-sensitive measurement techniques and general materials science. He followed that research experience by entering a postdoctoral opportunity at George Washington, gaining extensive knowledge in general electrochemistry and battery R&D.
Latest from Recycling Today
- ReMA opposes European efforts seeking export restrictions for recyclables
- Fresh Perspective: Raj Bagaria
- Saica announces plans for second US site
- Update: Novelis produces first aluminum coil made fully from recycled end-of-life automotive scrap
- Aimplas doubles online course offerings
- Radius to be acquired by Toyota subsidiary
- Algoma EAF to start in April
- Erema sees strong demand for high-volume PET systems