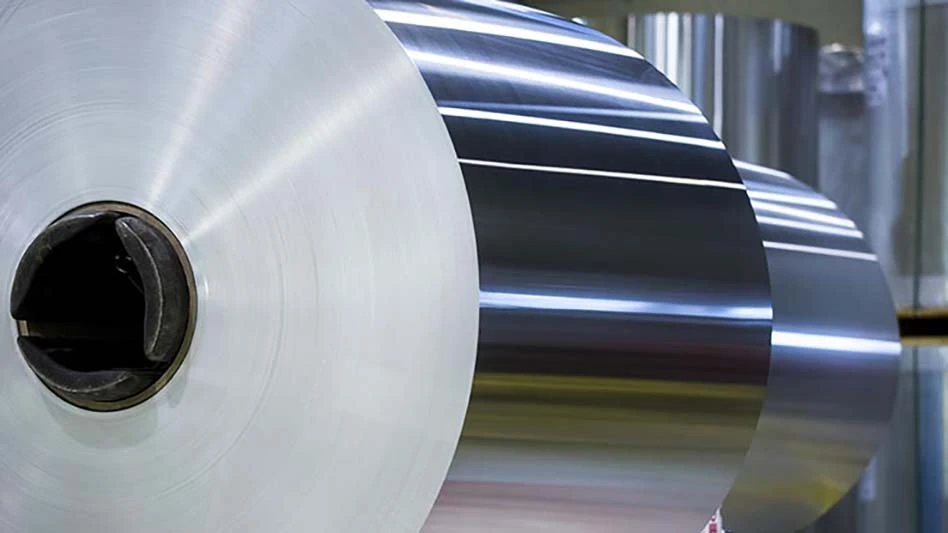
fotosr52 | stock.adobe.com
Washington-based nonprofit The BlueGreen Alliance has released a report that offers suggestions for reversing the decline of the U.S. primary aluminum industry to meet rising aluminum demand from the clean energy sector while also creating good-paying jobs, strengthening national security and reducing industrial emissions. Despite the advantages secondary aluminum production provides, the organization says insufficient scrap supplies mean more primary aluminum production will be needed.
In “Aluminum, Revitalized: Strengthening the Backbone of Our Clean Economy,” the BlueGreen Alliance, which unites labor unions and environmental organizations with the goal of solving environmental challenges in ways that create and maintain quality jobs and build a clean and equitable economy, notes that aluminum is used in solar panels, electric vehicles and other rapidly expanding clean technologies. By 2035, aluminum demand from U.S. solar power alone will exceed current the country’s aluminum production for all end uses, the nonprofit says, citing recent research. As demand soars, U.S. primary production has fallen, however, with only five primarily smelters operating today in the U.S. This production has been replaced by more polluting production overseas, the organization says, adding that primary aluminum production in China, now the source of a majority of the world’s aluminum, generates about 65 percent more emissions than U.S.-based production.
“As solar panels and electric vehicles spur rising demand for aluminum, we cannot depend on high-polluting aluminum production overseas that undercuts the very climate goals we seek,” BlueGreen Alliance Vice President of Manufacturing and Industrial Policy Ben Beachy. “Revitalizing clean U.S. manufacturing of aluminum—a material forming the backbone of the clean economy—is imperative for meeting our climate goals while offering the opportunity to create good-paying jobs in hard-hit communities.”
As primary aluminum production in the U.S. has declined, secondary production using scrap has grown, which has given rise to energy consumption and emissions reductions. According to the report, “Because aluminum recycling does not involve the highly electricity-intensive process of electrolysis, energy consumption is a fraction (about 6 percent) of what is needed for primary production.”
The report notes that a 2022 inventory of secondary facilities indicates that about 90 process aluminum scrap to produce secondary aluminum or aluminum alloys. Most of these 90 facilities (about 70) are found east of the Mississippi River, close to industrial centers that provide a source of scrap and accessible markets. With 13 secondary facilities, the highest concentration is in Indiana and the surrounding corridor, with 11 in Kentucky, eight in Ohio, seven in Tennessee, six in Pennsylvania, five in New York, four in Missouri and three each in Illinois and Michigan. Other states with the highest number of facilities include California (six), Alabama (five) and Texas (three), according to BlueGreen.
The report notes that maximizing collection, sorting and recycling processes for aluminum scrap would help displace about 15 percent of primary aluminum demand, effectively reducing absolute CO2 emissions by 250 million tons per year. “But under this scenario, postconsumer scrap would only supply about 43 percent of the global aluminum demand in 2050. “This means that regardless of recycling improvements, we will still need to increase primary production and mine additional bauxite,” BlueGreen says.
While the organization says the lower energy needs of secondary production give expanded recycling an important role to play in reducing sectoral emissions, growing aluminum demand exceeds scrap availability, necessitating the growth of primary production. “Transforming primary production will therefore be critical to reducing aluminum emissions.”
The report highlights how federal investments in the Inflation Reduction Act, the Bipartisan Infrastructure Law, the Defense Production Act and more can be leveraged to reopen aluminum smelters and retrofit facilities for cleaner aluminum production:
- 45X tax credit — an uncapped production tax credit to support expanded manufacturing of high-purity aluminum, among other clean technologies and critical materials;
- 48C tax credit — $10 billion available for manufacturers to install technologies that will reduce emissions by at least 20 percent; and
- U.S. Department of Energy Grants — about $6 billion for energy-intensive industrial facilities, including aluminum manufacturers, to adopt transformative technologies with the potential for deep emissions cuts.
Latest from Recycling Today
- Aqua Metals secures $1.5M loan, reports operational strides
- AF&PA urges veto of NY bill
- Aluminum Association includes recycling among 2025 policy priorities
- AISI applauds waterways spending bill
- Lux Research questions hydrogen’s transportation role
- Sonoco selling thermoformed, flexible packaging business to Toppan for $1.8B
- ReMA offers Superfund informational reports
- Hyster-Yale commits to US production