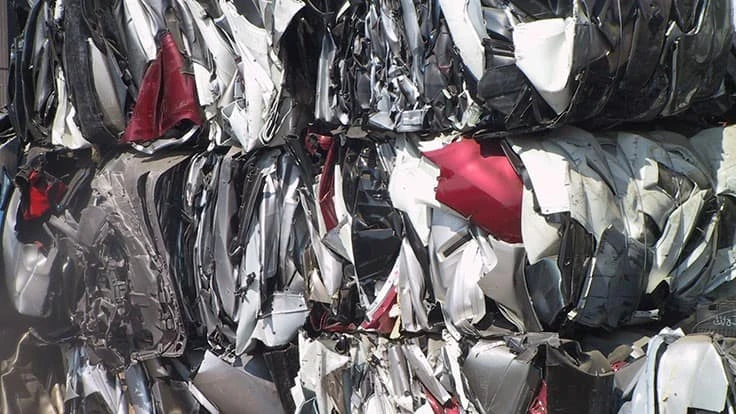
Portland, Pennsylvania-based Ultra-Poly Corp. has worked with the Plastics Industry Association on a project to collect and recycle thermoplastic polyolefin (TPO) plastic automobile bumper covers. The recycling firm and the Washington-based trade association have published a case study on the project.
The two organizations say the process as demonstrated can direct about 500 tons of plastic toward recycling outcomes. “The study also found the recycled material displays 85 percent to 90 percent of the flexibility and elasticity found in virgin material, making it ideal for numerous end product uses,” says Ultra-Poly and the Plastics Industry Association in a news release.
The process developed by Ultra-Poly does not rely on third-party collectors and processors to gather and preprocess the bumper covers. Instead, Ultra-Poly collects used covers directly from body shops, where they already have been removed from the automobiles and their reusable connected components already have been salvaged.
“This project demonstrates that true post-consumer material does not have to be collected only at the curbside and preprocessed by materials recovery facilities,” says Kevin Cronin, a vice president with Ultra-Poly. “It can also be sourced directly at the point of generation, reducing the carbon footprint and yielding more consistent recycled products.”
Point-of-generation collection also assures a steady stream of material. A single body shop can yield up to 30 scrapped bumper covers per month. The body shop itself saves money on dumpster space and is relieved of the concern that damaged covers may be improperly sold as replacement parts, the organizations say.
“This case study is a win all around for body shops, recyclers, manufacturers and the environment,” says Tony Radoszewski, CEO of the Plastics Industry Association. “We’re proud to have innovative member companies like Ultra-Poly out there, seeking new ways to eliminate plastic waste, providing new sources of valuable materials and expanding capabilities, which means more jobs in the recycling sector.”
The Ultra-Poly case study is part of the Plastics Industry Association’s larger New End Market Opportunities (NEMO) program, which focuses on developing new methods for the recovery, recycling and reuse of plastic products. NEMO places special emphasis on difficult issues, such as plastic grocery store bags. Another NEMO project has resulted in the successful use of such recycled polyethylene film in producing asphalt for road construction.
Ultra-Poly Corp. has five locations in Pennsylvania and produces custom compounded polypropylene (PP) and polyethylene (PE) resins from recycled plastics. The firm says it also provides toll reprocessing services for plant-generated scrap in several different industries.
Latest from Recycling Today
- Indiana county awarded $65K recycling grant
- Mixed paper, OCC prices end year on downward trend
- Updated: CAA submits final draft program plan in Oregon
- Enviri names new president of Harsco Environmental business
- Survey outlines ‘monumental challenge’ of plastic packaging collection in UK
- Nippon Steel acknowledges delay in US Steel acquisition attempt
- BASF collaborates to study mechanical plastic recycling
- Commentary: navigating shipping regulations for end-of-life and damaged batteries