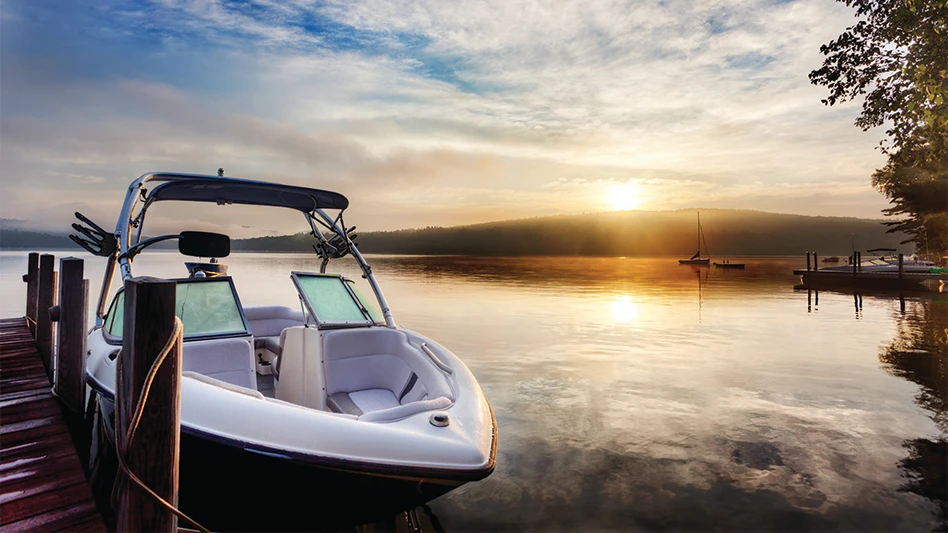
Jo Ann Snover | stock.adobe.com
Supersede, headquartered in Phoenix, recently launched what it claims is the world’s first 1:1 marine-grade plywood replacement.
Supersede Marine Board is an engineered extruded sheet crafted from plastic scrap and is modern, scalable and cost-effective, according to the company. The material is 100 percent recyclable, waterproof and rot-proof and does not splinter or split. Beginning with the boat manufacturing industry, Supersede also plans to provide its solution to manufacturers of modular homes, RVs and trailers.
The company says the launch of its product comes as traditional plywood prices are one-third higher than in 2019, following pandemic-related supply chain challenges. It notes that boat manufacturers increasingly are facing a rise in plywood warp, rot, splinter and performance issues because of a change in moisture levels, adding that marine-grade plywood is processed using harmful chemicals that potentially could cause health, safety and environmental hazards.
While marine-grade plywood has been used for decades, the company says the unreliability of its supply chain, its nondurability and its potential risk to human and environmental health make the market “ripe for transformation.”
“Boat manufacturers and their insurers have more experience than almost anyone with the headaches of plywood—from the persistent challenges associated with inconsistent performance, warping and splinters, to extensive maintenance, high costs and little peace of mind,” Supersede co-founder and CEO Sean Petterson says. “We have created the first modern breakthrough addressing these issues with the Supersede Marine Board, a true 1:1 replacement to marine-grade plywood that has all the attributes boat manufacturers look for—a durable, reliable and affordable solution that is nonhazardous, environmentally sustainable and always consistent. This isn’t just an upgrade to the legacy plywood industry, it’s a long overdue leap forward.”
Supersede says the potential environmental impact of its Marine Board is “substantial,” claiming that for every 72 sheets of half-foot plywood displaced, one tree is saved. Additionally, the company says its manufacturing and engineering process eliminates volatile organic compounds (VOCs), adhesives and waste. The company’s product also provides a cost-incentivized solution for plastic recycling.
The company says its vertically integrated and streamlined supply chain means manufacturers benefit from consistent pricing. Supersede also eliminates steps in the manufacturing process such as sanding, sealing and drying, saving partners labor costs while increasing throughput. Supersede says its offcuts also are 100 percent recyclable, and its offcut buyback program enables its customers to achieve zero-waste goals.
Growing its capabilities
According to Supersede co-founders Jordan Darling and Sean Petterson, the company has been operating in "stealth mode" since 2021 and publicly launched in October. It currently is addressing the boat building and RV manufacturing markets but plans to make its solution available to the construction industry and manufacturers of tractor trailers, modular homes and other specialty vehicles.
The company, which primarily works with postindustrial polypropylene (PP) sourced from local and U.S.-based manufacturers, resource recovery centers and brokers, manufactures its Marine Board product from its Phoenix headquarters and says it has plans to expand to a second facility later this year.
Darling and Petterson say that for every 100 sheets of Supersede 3/4-inch Marine Board, 2,500 pounds of recycled PP is used. They tell Recycling today that they are "currently ramping up production with our first factory at max capacity," and can displace approximately 2 million pounds of plastic annually.
"When our second facility is online and at max capacity, we will displace an additional 6 million pounds of recycled plastic annually," they add.
At the company's Phoenix facility, it regrinds and reuses all offcuts from its production process. Additionally, Darling, the company's chief operating officer, and Petterson, the company's CEO, say it partners with customers to purchase their leftover trimmings, which the company then reprocesses to create new products, further closing the loop on plastic scrap.
Darling and Petterson say the company's recycling process is a combination of internal expertise and strategic collaboration with industry-leading partners. To transform PP into plywood replacement boards, the company:
- Works directly with large manufacturing operations and with suppliers across the U.S. who source postindustrial and postconsumer PP from manufacturers that do not utilize their own scrap or offcuts, ensuring Supersede is capturing high-quality materials that would otherwise go to waste.
- Reformulates the material by using advanced pelletizing systems to shred and re-extrude the recycled PP, incorporating specialized additives that enhance the material’s strength, flexibility and durability. The company says its proprietary formulation process ensures consistent performance tailored to its needs.
- Uses specialized extrusion lines to transform pellets into high-performance sheathing boards. The company says its process is highly efficient, producing continuous 100-foot sheets of material that are cut and prepared to exact customer specifications.
“Later this year, we are expanding our operations to integrate the entire process—from recycled PP to proprietary formulations—under one roof,” Darling and Petterson say. “This will allow us to have even greater control over quality, cost efficiency and the environmental impact of our production process.
“By leveraging both our in-house manufacturing capabilities and partnerships with experts in recycled materials, we are able to deliver a unique, high-performance product that exceeds the standards of traditional plywood and provide unique products for our OEM [original equipment manufacturer] customers, allowing them to stay ahead of the curve and also contribute to a greener future.”
Latest from Recycling Today
- ReMA opposes European efforts seeking export restrictions for recyclables
- Fresh Perspective: Raj Bagaria
- Saica announces plans for second US site
- Update: Novelis produces first aluminum coil made fully from recycled end-of-life automotive scrap
- Aimplas doubles online course offerings
- Radius to be acquired by Toyota subsidiary
- Algoma EAF to start in April
- Erema sees strong demand for high-volume PET systems