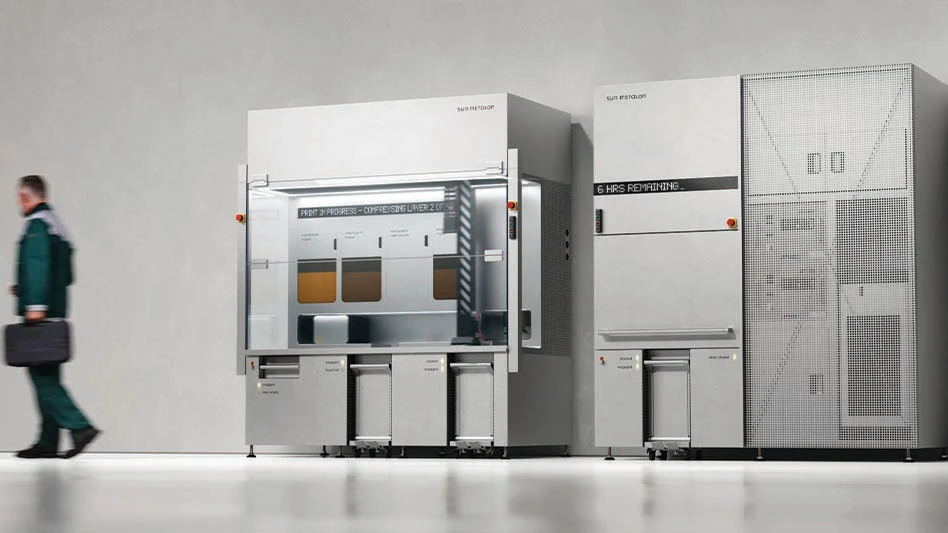
Photo courtesy of Sun Metalon Inc.
Producing steel and aluminum can generate as much as 10 percent of human-caused CO2 emissions annually—more than any other heavy industry.
Sun Metalon Inc., a Cambridge, Massachusetts-based startup that began operations in 2021 to develop metal forming equipment, has presented a solution it says foundries can use to recycle and refine scrap at its source, generating more value out of their material while reducing costs and slashing emissions.
The company’s technology, which rapidly heats metal without emitting CO2 and recycles scrap generated during machining, has drawn the interest of customers abroad, including automaker Toyota. Now Sun Metalon is in the process of expanding in the United States.
“We recognized that there was a real need in both recycling and refining, and it lends itself to our core technology,” says Mark Cook, Sun Metalon vice president of product and business development. “In the automotive industry, [for example], there are a lot of mandates to make sure that all of their components are recyclable. But that doesn’t necessarily address their efficiency in their factory. What do they do with all their scrap in their factory? And that’s what we’re doing.
“It doesn’t always get glory and recognition, but it’s important. And, so, we’re trying to [show] what we’re doing here and how important [our technology] is and how valuable it could become to companies [in the foundry space].”
The power of the puck
Sun Metalon’s method for quickly and efficiently heating metal lends itself to a number of applications, Cook says, but the company mainly has focused on aluminum as it attempts to grow its footprint.
Using a machine Cook says is comparable in size to a large desk and stands about 5 feet tall, foundries can take machining chips or grinding sludge generated in-house and convert them to what he calls a “clean metal puck” that can be placed back into production. The pucks measure 3 inches wide and about 2 inches tall, but the size is variable and can be customized to a facility’s needs.
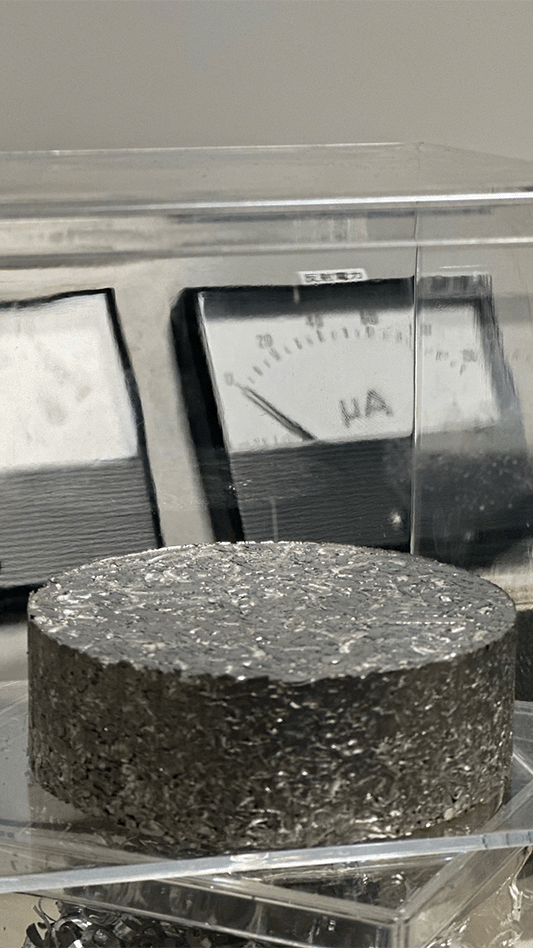
By comparison, Cook says recovering machining chips or grinding sludge typically results in a much lower value for that material, or what Sun Metalon calls “downcycling.” Cook uses A6000 series aluminum as an example. The chips generated from the machining process are contaminated with cutting fluids, making them less valuable when they arrive at a furnace to be melted.
“In the case of the automotive or aerospace [industries], they may not accept that recycled material coming back because it’s not going to be of the quality they need,” Cook says. “It can be used and can be recycled, but at a lower value.”
Cook says Sun Metalon’s heating technology allows companies to compress the metal puck to recover roughly 90 percent of the fluid, so it doesn’t have to be burned off at the furnace, which creates hydrocarbons.
“In theory, you’ve got 100 percent of what [material] you bring in,” Cook says. “This raw material goes out the door as finished products and with zero waste from the scrap side, and that’s our goal and that’s where we’re gaining traction with Japanese companies in automobiles and heavy industry but also here in the United States.”
Sun Metalon’s process involves using an electromagnetic heating source roughly the size of 1 cubic meter, outfitted with what Cook calls a “secret booster” that quickly produces pucks by heating the metal chips to a temperature where their surface particles bond with each other but won’t melt. “We can heat these metal pucks, clean them and allow the company to put that back into the start, their melt furnace or whatever the beginning of their process is, at very low energy levels.”
Cook estimates the machine can heat metal in two to three minutes using between 1,000 and 3,000 watts of power, depending on what a facility requires. As an example, he says a 3,000-watt unit processing pucks in short increments could yield roughly 200 tons per year of throughput. Sun Metalon’s technology can be scaled to increase wattage, or a customer could install additional units to increase throughput.
“It depends on the application and economies of scale for which way you want to go,” he says. “But it’s perfectly scalable either way. It’s very versatile.”
Though the company’s focus currently is on aluminum and steel, it has tested other metals and could expand its scope in the future.
Forging partnerships
Several years ago, Sun Metalon partnered with Toyota in Japan in the effort to develop a new method for aluminum recycling that would reduce CO2 emissions.
According to Sun Metalon, verification experiments confirmed the new process contributed not only to reduced emissions but also to improved safety and quality compared to the conventional aluminum recycling process. Toyota purchased equipment manufactured by Sun Metalon and begun verification testing of the new process, with results jointly presented at the Japan Foundry Engineering Society conference in May 2023.
“Sun Metalon and Toyota will work jointly to develop the technology to be ready for mass production, including the improvement of grade stability and equipment durability,” the news release says. “In order to implement this technology in society and to accelerate development, both companies are looking for partners who share the same vision and will work together to promote future development.
"With that vision in mind, the two companies intend to build an even stronger development system that will help interested companies collaborate in this effort.”
Upcycling solution
Cook says Sun Metalon wants to help customers “upcycle” their scrap metal. “Typically, that metal is downcycled. We’re upcycling it and recapturing most of the value of the original metal that they’re producing,” he says.
As an example, Cook says if a company produces $100 of metal, it might get paid significantly less for scrap generated during production. If it can recover the value back up to $90, then it has recovered most of that gap, he notes.
“We’re super excited about it,” he says. “We’re finding more and more applications every day and more customers. There are a lot of pain points out there with metal recycling and, specifically, with industrial metal recycling. … We’re talking about in the factory, helping those factories become more efficient. This technology, the secret sauce that makes it work, is our proprietary technology. But from a cost standpoint, it’s very manageable.”
Every application is different, but Cook says companies are intrigued by Sun Metalon’s potential to provide an affordable solution that also can address carbon emissions associated with transporting recycled material from facility to facility, for example.
“They’re able to deal with their sustainability initiatives but at an equal or lower cost where typically they might have a budget that’s maybe 10 percent above their current cost in order to implement their sustainability [initiatives],” Cook says. “We’re super excited about that as well. There’s a cost associated with being green and recycling, and we’re finding that we’re helping companies do that at a lower cost, so they’re saving money. So, we can do both.”
Latest from Recycling Today
- Recycled steel price crosses $500 per ton threshold
- Smithers report looks at PCR plastic’s near-term prospects
- Plastics association quantifies US-EU trade dispute impacts
- Nucor expects slimmer profits in early 2025
- CP Group announces new senior vice president
- APR publishes Design Guide in French
- AmSty recorded first sales of PolyRenew Styrene in 2024
- PRE says EU’s plastic recycling industry at a breaking point