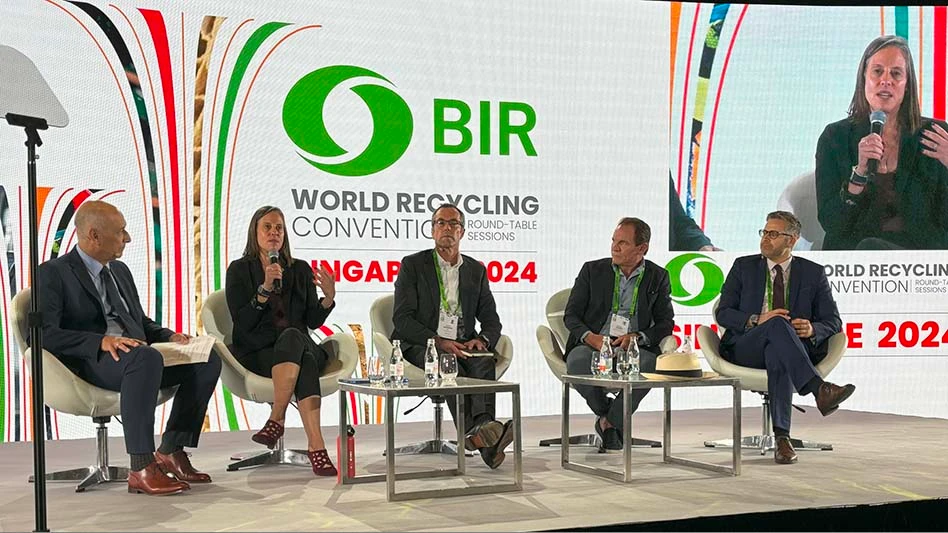
Recycling Today archives
Examining how much carbon is emitted in the steelmaking process has not led to unanimous agreement on how to either measure or lower steel’s carbon footprint, according to speakers at the Bureau of International Recycling (BIR) Ferrous Division meeting, held in late October in Singapore.
Adina Renee Adler of the Washington-based Global Steel Climate Council (GSCC) said recycled-content steel produced in an electric arc furnace (EAF) has proven itself as the lowest carbon footprint product.
The GSCC, which counts EAF steel producers among its members, measures and reports carbon emissions in the steel industry regardless of the production method.
The organization is not the only one seeking to measure and certify steel decarbonization efforts. Adler pointed to the Australia-based ResponsibleSteel certification standard but questioned whether it was measuring emissions appropriately.
ResponsibleSteel allows blast furnace/basic oxygen furnace (BOF) producers to use a sliding scale when attaining certification and even reduces a steel company’s score if it uses too much scrap, according to Adler. This, she said, discounts many of the decarbonization advantages of recycled-content steelmaking.
“It’s kind of messed up,” she said.
Adler said the GSCC and ResponsibleSteel recently have granted certified status to either a company or facility.
In GSCC’s case, its Indiana-based member company Steel Dynamics Inc. (SDI) attained GSCC certification in October. Adler said SDI uses about 85 percent recycled steel in its network of EAF mills and emits about 0.94 tons of carbon emissions for each 1 ton of steel it makes.
In late September, a ResponsibleSteel certification was announced for the Big River Steel operating unit of Pittsburgh-based United States Steel Corp. Big River has EAF melt shops in Arkansas and, according to Adler, uses 57 percent recycled content and emits 1.3 tons of carbon for each ton of steel it produces.
Patrick Davison of United Kingdom-based EMR Ltd., which operates metals recycling facilities in that nation and the U.S., said manufacturers of numerous products are “claiming to be green because it has a commercial impact.” He added, however, that the word green can be misused.
In addition to the GSCC and RepsonsibleSteel, Davison referred to environmental product declarations (EPDs), the London-based Science Based Targets Initiative (SBTI) and the European Union’s Carbon Border Adjustment Mechanism (CBAM) as emissions-related measuring systems to which EMR and its customers pay attention.
Davison, like Adler, expressed concern about vague definitions and measurement procedures, whether with good or questionable intentions.
“We need to paint a much clearer picture of what ‘green’ steel is about,” he said. "We need to focus on collaboration."
George Adams, CEO of Orange, California-based SA Recycling, was direct in his assessment: “Nothing reduces carbon on this planet more than recycling.”
Adams said operators of blast furnaces are aware of techniques to reduce emissions, but he sounded unconvinced that it is a priority for some BOF operators.
He cited U.S.-based Cleveland-Cliffs, which owns a direct-reduced iron (DRI) facility and a network of scrap yards, as continuing to favor ore-based production because “it’s so much easier” and cost-effective to use iron ore pellets.
The U.S. overall, however, received credit from Emmanuel Katrakis of Belgium-based recycling company Galloo for its 70 percent EAF market share. The EU’s shift away from Russian natural gas has exacerbated a situation in which high energy costs have hurt EAF competitiveness in Europe, according to Katrakis.
Rolf Willeke, who gathers steel recycling statistics for the Brussels-based BIR, said despite the challenges in the recycled steel sector, the world remains hungry for the secondary commodity. In the first half of 2024, China—the world’s leading steel producer—consumed 5.4 percent more scrap compared with the first half of 2023.
Leading European and U.S. scrap export destination Turkey, meanwhile, consumed 13.1 percent more scrap from January to June compared with the first half of 2023, while India’s ferrous scrap consumption was up by 14 percent year on year.
Such figures show that numerous steelmakers around the world continue to rely on steel scrap. Adler said the world will long need ore-based steel production but did not endorse the notion that the world is facing a scrap shortage.
She told recycling industry attendees that “discussions are happening without you” involving BOF operators and standards organizations that do not adequately recognize the carbon-friendly aspects of recycling—and proffering the notion that scrap is in short supply.
Enough scrap is available globally to reward recycled-content EAF steelmaking, she stated, and urged recycling companies to continue upgrading their products, to calculate and make available their Scope 1 and Scope 2 (transportation and production) emissions levels and to consider supporting the recycling-friendly GSCC standard.
The 2024 BIR World Recycling Convention Round-Table Sessions was at the Raffles City Convention Center/Fairmont Hotel in Singapore Oct. 27-29.
Latest from Recycling Today
- Republic Services, Blue Polymers open Indianapolis recycling complex
- Altilium produces EV battery cells using recycled materials
- Brightmark enters subsidiaries of Indiana recycling facility into Chapter 11
- Freepoint Eco-Systems receives $50M loan for plastics recycling facility
- PET thermoform recycling the focus of new NAPCOR white paper
- Steel Dynamics cites favorable conditions in Q1
- Hydro starts up construction in Spain
- Green Cubes unveils forklift battery line