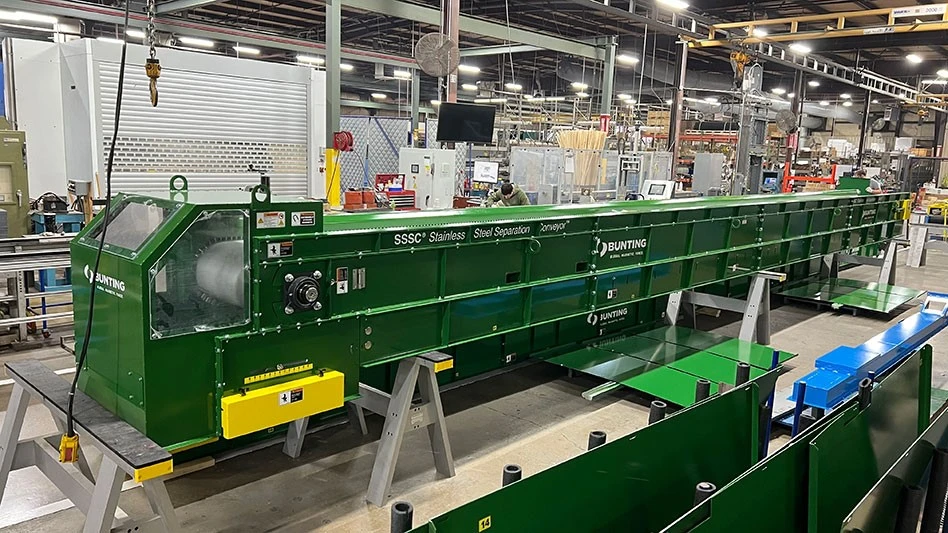
Photo courtesy of Bunting
This autumn, United States-based equipment maker Bunting shipped a sizable stainless steel separation conveyor (SSSC) to a recycling operation in North Carolina that processes mixed shredded material. When market conditions call for high-purity zorba free of stainless scrap—or for pure stainless shred—the owner of the SSSC will be ready.
“An automotive recycler in North Carolina is the proud new owner of an exceptionally large SSSC conveyor [that] is two feet wide and 38 feet long,” Bunting states. The equipment supplier says the recycler will “now freely pull midsized stainless steel pieces out of shredded automotive shredder residue (ASR).”
“We utilize a patented magnetic circuit that creates some of the most powerful high-intensity magnetic head pulleys in the industry,” says Jake Fenwick of Bunting. “The magnetic head pulley gauss and circuit design gives us the ability to magnetically separate very weakly paramagnetic materials out of the product stream of ASR or ICW [insulated copper wire] lines. Then, depending on the fraction size, we will determine which unit we would recommend.”
The customer for the order filled this autumn was equipped with the 38-foot-long SSSC because it believed a single, longer SSSC was better than going with a series of standard 12-foot SSSC conveyors. The sequential conveyors, in the customer’s case, also would have required an additional inline transfer to feed them, according to Bunting.
“For fun perspective on the size of this conveyor, we [turn] to baseball,” Bunting writes. “The Green Monster wall in left field of [Boston’s] Fenway Park is 37 feet tall. The green SSSC is 38 feet long.”
Fenwick, a technical writer with Bunting, tells Recycling Today that SSSCs typically are placed in lines “after all the ferrous metals have been removed—this is critical. We separate 300 series stainless steel from plastic, glass, ASR, zurik, zorba or ICW streams. The key to optimal stainless steel separation is utilizing dry material with a consistent fraction size and making sure the material that flows over the high-intensity magnetic head pulley is at a thin/monolayer stream.”
He adds, “Different designs and sizes are used depending on the fraction size. For example, most ASR will come out of a trommel screen in small, mid- and large fraction streams, which utilize different models of SSSCs.”
Fenwick says Bunting sells and configures SSSCs for customers with different challenges and priorities. “We basically have three different sets of customers,” he remarks. “The primary customer is looking for a 98 percent or higher purity stainless steel fraction to sell to a smelter for their highest ROI [return on investment]. The second customers are looking to pull all the stainless and other ferritic organic material out of their primary metal stream. An example of this would be taking stainless and slightly magnetic foam/cloth out of an ICW stream prior to chopping. The third would be pulling stainless steel out of a zorba stream to give a higher purity of aluminum.”
While the “green monster” SSSC deployed in the U.S. Southeast was made at one of Bunting’s three U.S. facilities, Fenwick says customers in Europe can purchase SSSCs assembled in the firm’s United Kingdom plant. He says delivery times on SSSCs can run from eight to 16 weeks.
Bunting describes itself as dedicated to designing, making and selling magnetic technology and equipment since 1959. It is based in Newton, Kansas, with additional manufacturing facilities in Illinois, Pennsylvania and the U.K.
Latest from Recycling Today
- Two factors raise ferrous export questions in April
- Analyst: Scrap imbalance lost amid copper’s critical status
- AF&PA report shows decrease in packaging paper shipments
- GreenMantra names new CEO
- Agilyx says Styrenyx technology reduces carbon footprint in styrene production
- SABIC’s Trucircle PE used for greenhouse roofing
- Hydro to add wire rod casthouse in Norway
- Hindalco to invest in copper, aluminum business in India