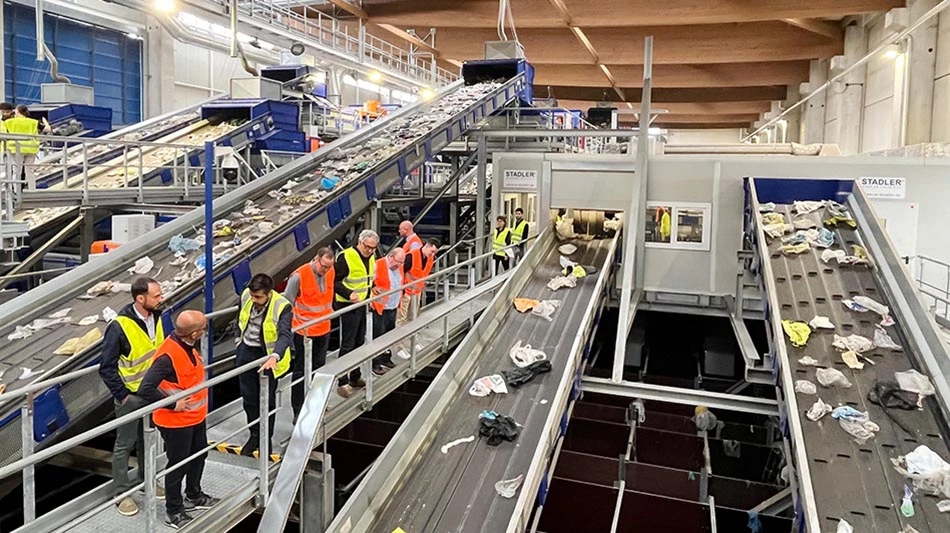
Photo courtesy of Stadler Anlagenbau GmbH
Germany-based sorting and recycling equipment provider Stadler Anlagenbau GmbH says it has helped design and install "the largest circular plastics sorting plant in Italy."
The new facility near Turin, Italy, is operated by Italian utilities and environmental services firm Iren SpA. Stadler says the plant has the capacity to process approximately 100,000 tons of mixed plastics and metal cans each year, closing the circular economy loop by sending up to 80 percent of incoming material to recycling plants.
In mid-September, Stadler and the Iren Ambiente business unit of Iren welcomed a group of customers and media representatives for a tour of the facility.
Stadler says the new sorting plant integrates "innovative solutions and advanced technologies" to automatically sort 17 types of polymers and plastics, aluminum, and ferrous materials, ensuring maximum operational flexibility.
“We are proud to be Iren’s supplier,” says Paolo Cravedi, senior project manager with Stadler. “We started with a small project in 2020, then went on to work together on Iren’s WEEE [waste electrical and electronic equipment] plant in Volpiano, Italy; its plastic recycling plant in Pianezza, Italy; and the ReCap facility in Parma, Italy, which processes both plastics and cardboard.
“We also designed and built the Valterza plant in Asti, Italy, which sorts mixed plastic waste made up of mainly bottles and films.”
The new circular plastics plant starts the process by separating the incoming material into three streams: bulky, medium size and fines.
The bulky material is screened with a Stadler STT5000 ballistic separator, designed to ensure a clean separation of film, with materials then heading toward a sorting cabin.
Fine material, after it is extracted by a Stadler trommel screen and ballistic separator, are processed through a magnet separator and eddy current system to extract ferrous metal and aluminum. What remains heads into a Stadler trommel screen and under two optical sorters to recover small plastic components such as bottle caps and other materials with value.
The medium-sized material is split into two lines, each with a Stadler STT5000 ballistic separator, designed to sort the two-dimensional and three-dimensional material, while fines are sent to the dedicated fines line. The 2D stream goes through six optical sorters to divide films into polypropylene (PP), polyethylene (PE) and bio-film fractions.
The 3D stream is cleaned of ferrous metal, then separated with optical sorters into four colors of polyethylene terephthalate (PET): clear, blue, multicolored and opaque PET (such as trays). Further optical sorting “ensures additional automatic quality control and cleaning of these primary products,” according to Stadler.
In parallel, says the firm, high-density polyethylene (HDPE), polystyrene (PS) and PP fractions are sorted on a second line. The output of the two 3D lines comes together to enable the extraction of clean aluminum particles, the company adds
Residual materials from the 2D and 3D lines go through a second sorting process at the Italian plant, with materials fed beneath optical sorters to recover any marketable materials left. Some of these containers are sent to what Stadler calls an advanced bottle recovery line equipped with a bottle opener, a dedicated ballistic separator and a material dosing system "to guarantee maximum recovery."
The system for Iren Ambiente includes a load cell system installed to monitor the quantity of incoming material and the quantities of the different materials stored in the bunkers ready for baling.
“This enables the operator in charge of the baling presses to keep track of exactly how much material is contained in each bunker and produce a precise number of bales for each product,” the company says.
Also included are features and technology tasked with data collection and analysis tied to preventive machine maintenance and predictive maintenance.
“We know Stadler well and we appreciate their excellent organization, high reliability and the precision with which they execute all projects," says Flaviano Fracaro, technical director at Iren Ambiente. "Equally important for us is the quality and reliability of their product. In our experience, all installations have gone into production on schedule, with short start up periods, and deliver excellent performance, minimizing issues and downtime.”
Fracaro calls the plant “a truly impressive facility with all its machines and optical sorters.”
“What we appreciate most is the layout’s space management, with walkways that make all the machines accessible and the entire plant easy to navigate, ensuring excellent access for maintenance," Fracaro adds. "Additionally, thanks to the various management systems for operators, it is very easy and intuitive to control and manage the entire facility.”
Latest from Recycling Today
- RMDAS April figures show recycled steel price setback
- Steer World offers PEX plastic recycling machine
- New recycling grant program launches in Massachusetts
- Tire Recycling Foundation names executive director
- Dock 7 named 2025 Exporter of the Year at New Jersey International Trade Awards
- Waste Connections reports ‘better than expected’ Q1 results
- Commentary: How EPR is transforming the packaging industry
- Acerinox names new North American Stainless CEO