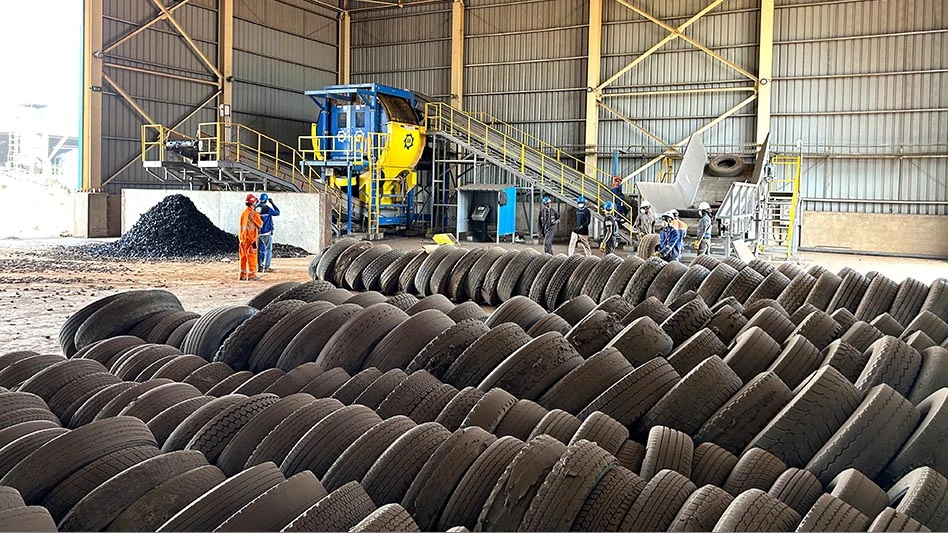
Photo courtesy of SSI Shredding Systems Inc.
SSI Shredding Systems Inc., Wilsonville, Oregon, says American-made equipment it has provided to a cement producer in the African nation of Senegal is shredding end-of-life tires, “providing a cost-effective, space-saving solution that converts waste tires into energy.”
Senegal, like much of West Africa, is experiencing a period of rapid urban development and economic growth, according to SSI.
“Large deposits of limestone in Senegal and high demand have led to an organically expanding cement industry,” the equipment maker says.
One process in cement production involves heating crushed limestone in a kiln to produce an intermediary product known as clinker. To generate the immense amount of heat required in clinker production, kilns most often are heated with coal. To reduce the cost and carbon emissions of coal-fired kilns, clinker factories also use recycled tire chips or tire-derived fuel (TDF) as a supplemental fuel source.
Senegal-based cement producer Les Ciments Du Sahel, located about 30 miles outside of the capital city of Dakar, produces 600,000 tons of cement annually and has added an in-house TDF line to produce its own tire chips.
In designing this expanded facility, Les Ciments Du Sahel partnered with Chinese-based engineering firm CBMI Construction Co. Ltd (CBMI). CBMI has more than 60 years of experience developing systems for waste-to-energy and power generation plants, according to SSI.
Tires are a difficult material to shred because of their thick rubber treads inlaid with high-tensile steel wire. SSI says a shredder “with a large enough throat, specialized internal parts and enough power” is required.
To add to the challenges for a shredding device, tires can contain high levels of contaminants like dirt and sand “that accelerate wear on cutters and screening equipment,” SSI says.
CBMI reached out to SSI because of its decades of experience designing systems for tire processing, says the United States-based equipment firm.
After considering the conditions of the operation, as well as the budget, SSI says it designed and manufactured an M120 two-shaft shredder with a trommel screen enclosure. The company says it was “confident in the system” in part because of its experience building trommel systems since the mid-1990s.
“Trommel systems are a great option for companies who are considering starting a TDF line,” says Rich Ellis, Asia sales manager at SSI. “It is a cost-effective option that is easy to maintain, has a small footprint, and produces a good quality fuel chip.”
The trommel, a rotating drum screen, captures the tire pieces as they leave the shredder. Fingers on the screen recirculate the pieces until gravity drops them back into the cutting chamber. Once the pieces reach the desired size they will pass through the screen and onto a conveyor.
“Trommel systems excel in conditions with high levels of dirt and sand. Due to their design, dirt can pass easily out of the screen as it spins," SSI says.
The combined shredder-trommel screen system produces a clean sheared tire piece that can flow easily into an incinerator, according to SSI.
Relative to their vibratory screen counterparts, trommel systems are considerably more economical and space-efficient solutions, adds the equipment firm.
Instead of requiring multiple conveyors and lots of floor space, the trommel system at Les Ciments Du Sahel “fits snuggly into the corner“ of the facility, taking up floor space only slightly larger than the footprint of the shredder itself—around 300 square feet, according to SSI.
The small footprint does not mean small power, adds the company, saying the 250-horsepower M120 is powered by a direct drive electric motor capable of shredding 6 tons of mixed auto and over-the-road truck tires per hour.
SSI describes the M120 as a low-speed, high-torque shredder that “can handle the challenges of tire shredding with ease.”
“Providing reliable and economical shredding solutions to companies in emerging markets like Senegal is an essential part of sustainable urban and industrial development," the company says.
A video of the system at work has been posted by SSI to YouTube.
SSI Shredding Systems engineers, manufactures and services size- and volume-reduction systems for an array of applications, including the process of recycled metals, solid waste and tires.
Latest from Recycling Today
- BlueScope, BHP & Rio Tinto select site for electric smelting furnace pilot plant
- Magnomer joins Canada Plastics Pact
- Out of touch with reality
- Electra names new CFO
- WM of Pennsylvania awarded RNG vehicle funding
- Nucor receives West Virginia funding assist
- Ferrous market ends 2024 in familiar rut
- Aqua Metals secures $1.5M loan, reports operational strides