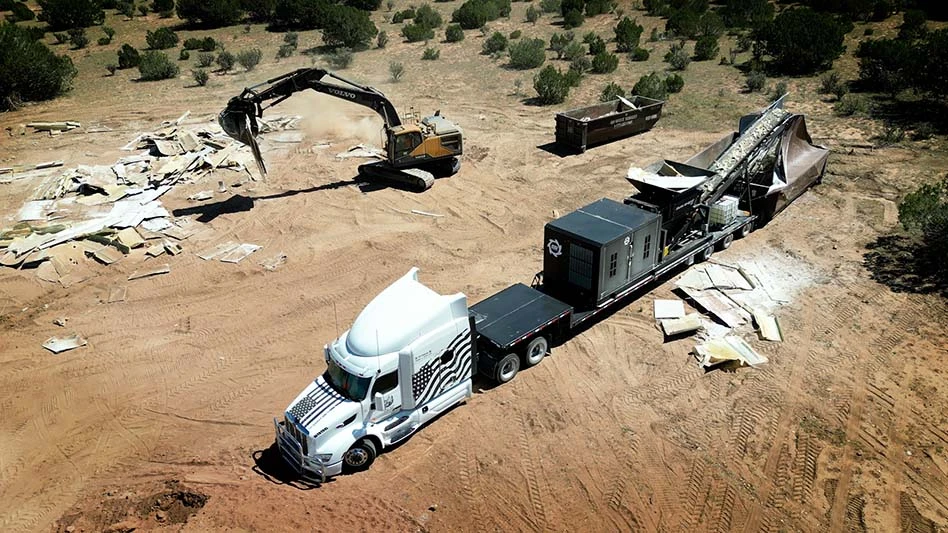
Photo courtesy of SSI Shredding Systems
Wind power energy is a green industry prevalent throughout the United States, yet recycling used wind turbine blades has become a problem. According to the United States Geological Survey, the U.S. is home to more are than 70,000 wind turbines.
According to a news release from Wilsonville, Oregon-based SSI Shredding Systems Inc., wind turbine blades must be rebuilt every 10 to 12 years. The blades break down from flexing due to erosion, ultraviolet damage, lightning strikes and are recalled because of delamination and cracking. Manufacturers construct the blades from a variety of materials, including fiberglass, carbon fiber, balsa wood, foam and resin.
This variety of manufacturing materials makes them difficult to repair or reuse. Instead, SSI says energy companies leave old wind turbine blades on the ground next to their old towers or send them to landfills.
SSI says solutions are in development to address this growing concern.
“We’re in the infancy of wind turbine blade recycling,” says Lee Sage, industrial sales specialist at SSI. “The problem is the U.S. dove into wind energy, never considering the end of life of those components and where they would go. It was always going to be someone else’s problem.”
Sean Baisden, owner of New Mexico-based Pitbull Blade Demolition, is helping to address the thousands of wind turbine blades decommissioned each year. To keep his costs down, Baisden needed a machine that could shred blades while being small enough to transport from wind farm to wind farm. He reached out to SSI Shredding Systems, which went on to design a solution.
Blade recycling on autopilot
Wind turbine blades are difficult to shred because of their unique components and enormous profile. SSI says the Dual-Shear M120 has the torque and technology to break down and recycle them. For more than two decades, the Dual-Shear M120 has been deployed to reduce bulky items such as tires, appliances, aluminum and electronic scrap.
“There are a lot of different aspects that go into working or developing a new application, like a wind turbine blade,” Sage says. “This has been three years in the works.”
Creating a mobile shredder can be challenging since it must be within the weight and height constraints the Department of Transportation sets. However, being able to move the shredder to various generating sites is invaluable to Baisden and his business.
SSI’s engineers designed the M120 with a mobile retrofit to solve this issue. The shredder is mounted on a 53-foot flatbed trailer and hauled with a diesel-powered vehicle. The shredder rotates at a low speed, uses high-torque hydraulics and runs on a classic Caterpillar motor.
Precut turbine blades are fed into a hopper on top, which pulverizes them into smaller pieces. The material is then moved up a conveyer belt built with a skid-mount design that empties the shredded material into a truck or dumpster.
“An average blade takes about two to three hours to shred, and it’s shredded down into sub-4-inch pieces,” Baisden says. “We then supply these shreds to Regen Fiber, a new company in Iowa that recycles them for reuse as raw materials in various industries. So, none of the material whatsoever goes to the landfill from the wind turbine [blade].”
Regen Fiber, a wind turbine blade recycling company based in Des Moines, Iowa, recently launched its patent pending process for converting shredded turbine blades into reinforcement fiber materials. The Travero-owned company says these materials add strength and durability to concrete and mortar applications such as pavement, slabs-on-grade and precast products.
SSI says the Dual-Shear M120 shredder is easy to operate and requires minimal maintenance compared with the daily upkeep needed for most industrial shredders. The unit offers a long life expectancy because every part of it is replaceable. Using American-made parts also makes repair time quick and painless.
The company says nearly all of its shredders are built to order and can be customized.
Latest from Recycling Today
- Steel Dynamics nets $217 million on record shipments
- Massive Chinese steelmaking rebound recorded in March
- LME looks into sustainable metal pricing
- OnePlanet Solar Recycling closes $7M seed financing round
- AMCS launches AMCS Platform Spring 2025 update
- Cyclic Materials to build rare earth recycling facility in Mesa, Arizona
- Ecobat’s Seculene product earns recognition for flame-retardant properties
- IWS’ newest MRF is part of its broader strategy to modernize waste management infrastructure