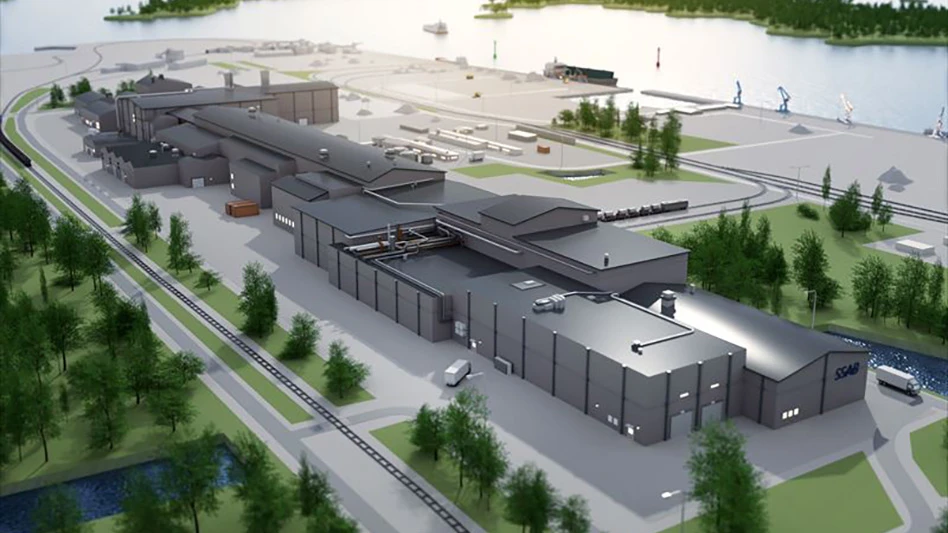
Image courtesy of SSAB
The board of directors of Sweden-based metals producer SSAB has decided to build a fossil-free minimill in Luleå, Sweden.
When the electric arc furnace (EAF) technology is installed, SSAB will close the current blast furnace/basic oxygen furnace (BOF) production system. The company says the move will reduce Sweden’s CO2 emissions, along with a previously announced BOF-to-EAF conversion taking place at its mill in Oxelösund, Sweden.
The replacement Luleå mill will have a capacity of 2.5 million metric tons per year of steel production and will consist of two EAFS and advanced secondary metallurgy, a direct strip rolling mill to produce SSAB’s specialty products and a cold rolling complex.
The new melt shop will be supplied with a mix ferrous scrap and what SSAB calls “fossil-free sponge iron” from a Hybrit demonstration plant in Gällivare, Sweden.
“The transformation of Luleå is a major step on our journey to fossil-free steel production,” SSAB President and CEO Martin Lindqvist says. “We will remove 7 percent of Sweden’s carbon dioxide emissions, strengthen our competitive position and safeguard jobs with the most cost-effective and sustainable strip production in Europe.”
SSAB is investing up to $4.5 billion in Luleå. “By investing in new technologies, SSAB is avoiding investments otherwise required in existing plant and equipment of $2.15 billion during the next 10 years,” the company says. “The investment will result in significant value creation.”
Compared with operating with blast furnaces and BOFs, SSAB estimates an improvement in yearly earnings before interest, taxes, depreciation and amortization (EBITDA) of nearly $500 million at current commodity forecasts.
The EAF mill will offer a better cost position with lower fixed costs, higher efficiency, shorter lead times and eliminated CO2 costs, according to the company, and the mill design includes a production increase of 500,000 metric tons per year and the ability to produce more specialty and premium steel grades.
Startup of the new mill is planned for the end of 2028, with the minimill ramping up to capacity one year later. “To date, SSAB has entered 55 partnerships with leading customers for our fossil-free and zero steels," the company says about markets for the mill's products.
SSAB made a similar decision in 2023 regarding its Oxelösund mill and says that project is proceeding according to plan.
“Together with our partner [Sweden-based sponge iron provider] LKAB, we are making a commitment to eliminate the CO2 emissions from our value chain and establish the new benchmark technology for a fossil-free future,” Lindqvist says.
Latest from Recycling Today
- Lautenbach Recycling names business development manager
- Sebright Products partners with German waste management equipment company
- WasteExpo transitions to biennial format for enhanced experiences
- Study highlights progress, challenges in meeting PCR goals for packaging
- Washington legislature passes EPR bill
- PureCycle makes progress on use of PureFive resin in film trials
- New copper alloy achieves unprecedented high-temperature performance
- Gränges boosts profits and sales volume in Q1 2025