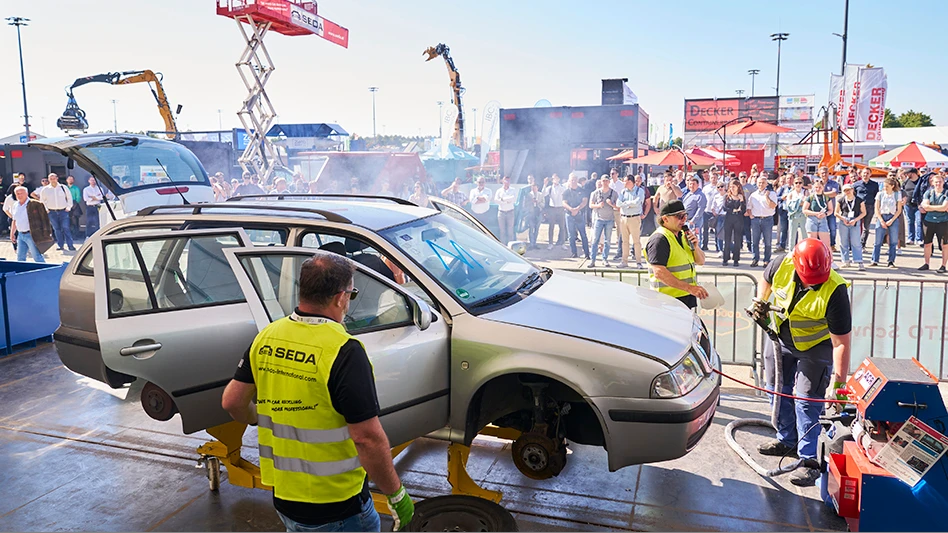
Photo courtesy of SEDA Umwelttechnik GmbH
SEDA Umwelttechnik GmbH, an Austria-based company with a focus on end-of-life vehicle (ELV) recycling technologies, demonstrated several portions of its product line at the IFAT trade fair, which was held in May in Munich, Germany.
The company says it cooperated with the Confederation of German Steel Recycling and Waste Management Companies (BDSV) to demonstrate equipment and techniques it offers to EVL recyclers, including those handling electric vehicles (EVs).
“International visitors and professionals from all over the world could experience the entire recycling process” SEDA says of the demonstrations it offered three times per day at its 38,500-square-foot exhibit area.
SEDA says it provided “exhaustive" information encompassing the current and related innovative processes as well as handling of ELVs. Its process as consisting of five stages: preparation, depollution, dismantling, EV recycling and further handling and compacting.
The preparation stage involves creating a disassembly and dismantling plan for the parts that can be prepared for further sale and use for each vehicle. All other parts go into the raw material recycling process.
Dismantling is carried out on a vehicle trolley designed to provide an "easy positioning" of an ELV in a workshop that can be forklift-free. SEDA says forklift-free workshops have proven “very popular" in the recycling industry, since the maintenance costs are low and possible dangers of forklift operating are eliminated.
Depollution involves the draining and safe handling of average of oils and liquids, of which an average of 22 liters (5.8 gallons) can be found in a typical ELV, according to SEDA.
Like depollution, dismantling takes place on the same trolley in the SEDA system, with that trolley moving from the preparation work station to the depollution station and then the dismantling stop.
Workers with hand tools, including hydraulic shears, remove the remarketable components previously identified at the preparation stage. A crane lift is used for heavier parts, such as a rear axle.
EVs undergo an additional stage largely involving battery removal and several safety considerations and techniques SEDA says are critical to the process.
At IFAT, SEDA enlisted the help of a Liebherr scrap handler outfitted with a shear made by Italy-based Zato s.r.l. to cut each hulk into several pieces. Zato especially designs and produces compatible shears for scrap and metal recycling with an installed weight of from 1 to 9 tons.
Finally, at IFAT 2024, the sheared pieces of steel were fed to an RR6 model baler made by Italy-based Roter Recycling.
The IFAT 2024 trade fair attracted more than 140,000 visitors from over 170 countries. More than 3,200 exhibitors took part. IFAT 2026 has been scheduled for May 4-8, 2026.
Latest from Recycling Today
- Commentary: The escalating danger of lithium-ion batteries in recycling and the need for an urgent industry response
- PLASTICS shares concern over tariffs
- Industrial Netting: We’ve got you covered with Car-Go-Net®
- Frequently asked questions about Industrial Netting’s Car-Go-Net®
- Customer testimonials: Industrial Netting’s Car-Go-Net®
- Tracey Road Equipment becomes authorized Tana North America dealer
- Machinex completes three MRF installations
- BTR appoints CEO