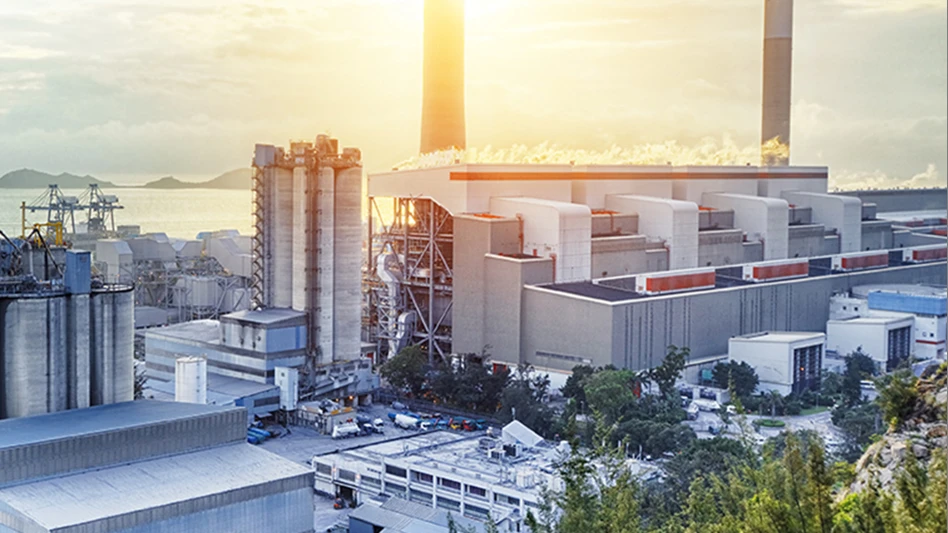
Photo courtesy of the South East Asia Iron and Steel Institute
Steelmakers in North America, Europe and beyond have publicized their attempts to lower their carbon footprints. In most cases, the use of recycled content in electric arc furnaces (EAFs) is a leading factor.
Producers that wish to export steel to Europe and the United States have kept a close eye on carbon border adjustment mechanism (CBAM) systems being enacted and discussed to provide low-carbon steel producers with trade protection.
A late-May message from the secretary general of the Malaysia-based South East Asia Iron and Steel Institute (SEAISI) describes a situation in that part of the world that portrays the opposite: a widespread shift away from EAF production toward the use of coal and iron ore in blast furnace/basic oxygen furnace (BOF) production.
Referring to the Association of Southeast Nations (ASEAN) region, Yeoh Wee Jin of SEAISI writes in part, “The ASEAN steel industry is going to become more carbon intensive, ‘de-greening’ in the future, if ASEAN governments continue to encourage such investments without carbon capture, utilization and storage systems (CCUS).”
Figures collected by the association show that while in 2011 EAF technology accounted for 95 percent of steel output in the ASEAN region, major new investments in blast furnace/BOF mills could reduce that figure to just 38 percent by 2018.
The SEAISI secretary general refers to blast furnaces as containing “older technology and the most pollutive technology that emits a lot of carbon.”
Yet, Malaysia itself—along with Indonesia and other ASEAN countries—has added considerable blast furnace/BOF capacity in the last few years, with potentially more on the way.
In Malaysia, writes Yeoh, the long steel products (bars, wire rod) sector was already in an overcapacity situation in 2018. However, “A new entrant with a capacity of 3.5 million tons per year (tpy) emerged, [and] what happened was a massive price competition, followed by a surge of exports of steel from Malaysia to neighboring countries.”
Among the largest such projects in Malaysia is a blast furnace/BOF complex started earlier this decade by the Xin Wu’an Steel Group of the People’s Republic of China, with the mill operating under the name Wenan Steel.
Reports about just how large the Wenan Steel complex will eventually become have ranged from 3.5 million tpy to up to 10 million tpy. The latter figure would nearly double capacity in Malaysia from 2018, when it was already considered by SEAISI as being in an overcapacity situation.
The extent of China-based steelmaking capacity installed or planned in ASEAN countries includes investments in: Malaysia (15.5 million tpy, including Wenan); Indonesia (9.5 million tpy); the Philippines (18 million tpy); Cambodia (3.1 million tpy); and even troubled Myanmar (4 million tpy). Those figures come from a 2020 report from the Singapore-based Yusof Ishak Institute.
As Yeoh writes in his essay, overcapacity leads to price cutting, red ink, mill shutdowns and (before the latter) a concerted effort to export products at any price.
For ASEAN blast furnace operators, the CBAM effort in Europe and the U.S. to prevent high-carbon-emissions steel from entering their markets could provide a barrier in export markets.
For steel industry observers, the selection of high-carbon steelmaking methods offers just one more reason why the ASEAN investments are raising questions in that region and beyond.
Writes Yeoh, “Blast furnace/BOF systems are 3.4 times more pollutive compared to EAF systems. Based on our computations, the ASEAN steel industry’s emissions will accelerate in the future with emissions from blast furnace/BOF hitting 84 percent of total emissions compared to EAF emissions of 16 percent by 2028.”
In addition to the export barriers conundrum, Yeoh asks, “How does this de-greening trend fit with the ASEAN countries’ Net Zero commitments? I believe ASEAN governments are looking at these seriously, and potential investors should also review their various proposals to bring in green technology to ASEAN.”
Offering some hope in Malaysia, he writes, is a Ministry of Investment, Trade and Industry (MITI) two-year moratorium policy that took effect last August designed “to allow for reassessments to address the challenges faced by the local iron and steel industry and update the industry’s direction” in line with an existing ministry plan. (Yeoh also writes, without elaborating why, that the moratorium applies to “non-ferrous recycling activities.”)
Yeoh also says MITI is in the process of forming a special committee that intends “to look at the sustainable development of the future” of the iron and steel industry in Malaysia, with participants including himself, the MITI minister and the CEO of HSBC Bank Malaysia.
Latest from Recycling Today
- Lautenbach Recycling names business development manager
- Sebright Products partners with German waste management equipment company
- WasteExpo transitions to biennial format for enhanced experiences
- Study highlights progress, challenges in meeting PCR goals for packaging
- Washington legislature passes EPR bill
- PureCycle makes progress on use of PureFive resin in film trials
- New copper alloy achieves unprecedented high-temperature performance
- Gränges boosts profits and sales volume in Q1 2025