
Photo by Brian Bohannon Photography
Sessions held back-to-back Sept. 17 at Scrap Expo 2024 in Louisville, Kentucky, sought to define what the term “green steel” means, with the help of industry veterans representing both steelmakers and scrap suppliers.
Under the umbrella of the Changing Steel Landscape, panelists discussed low-carbon steel, the scrap flows supplying mills such as those operated by Nucor Corp. and SSAB, and changes to those flows that could be coming as new mill capacity is added in the U.S.
The meaning of ‘green steel’
Trevor Saunders, vice president of Charlotte, North Carolina-based Nucor Corp.’s Raw Material Group, and Sean Keenan, vice president of supply chain at SSAB Americas, agreed that the term “green steel” was broad and somewhat difficult to define during the Steel Mill Focus session.
In Saunders’ view, green steel, or clean steel, is produced from electric arc furnace (EAF) technology, or steel made from recycled scrap that “starts at a base that’s much more competitive from a decarbonization standpoint than the rest of the world.”
RELATED: Scrap Expo 2024: Meeting evolving customer expectations
“For us, when we think about green steel, we think about clean steel that offers a level of circularity at its base that starts with lower carbon emissions as well as gives us an avenue to compete on the global stage better than anyone else,” he said.
Keenan added that term “green steel” is a generic evaluation of moving toward a particular lower-carbon process, and SSAB’s goal is always to think about a science-based target using its data analysis to truly understand what its carbon emissions look like and how to decrease them.
“At SSAB, we produce the most sustainable steel plate in North America, and we’re able to do that because in 2023 we had our electricity come 100 percent from renewable generation,” Keenan said. “In 2024, we’ll have about 90 percent from renewable generation, and the other 10 percent from non-carbon-emitting. So, that’s a great start for us.”
Keenan said his Sweden-based company, which operates steel mills in Sweden, Finland and in Alabama and Iowa in the U.S., has utilized scrap as its primary raw material source 98 percent of the time, with no carbon embodied in that scrap. “On top of our renewable electricity, we’re moving to renewable natural gas as an opportunity to run our reheat furnaces and everything we run in the primary end,” he said. “We’re using biomaterials, [too,] so all of these give us an opportunity to reduce our carbon footprint.”
Keenan noted that SSAB was able to make a finished product at its Montpelier facility in Iowa last year that featured zero carbon and was audited and verified by third-party organizations.
“Of course, it’s green steel, but there’s no real definition of what green steel is,” Keenan said.
Regarding the supply of scrap for recycling, session moderator John Sacco, president of Bakersfield, California-based Sierra International Machinery, pointed out that new mills—including some that will utilize EAFs—are being built in the southern U.S., meaning increased capacity and the need for more material is on the way. Keenan added that the U.S. scrap market is highly efficient and has developed material for the mills in the areas where the mills need it.
“We know that recycled materials generally are consumed in the areas where they were generated,” Keenan said. “There’s an efficiency to that. There’s also a lower carbon embodiment to that if you have that in your mix, or your Scope 3 emissions [tracking]. … As you’re starting to see, most people are making decisions with that efficient supply chain in mind and are locating these facilities where there is going to be a ready supply of scrap in the various forms that they’re going to need.”
Keenan noted that steelmakers converting their basic oxygen furnaces (BOFs) to EAFs, as well as the building of new production facilities, could be disruptive to the scrap industry.
“That’s going to happen in North America in the next two to three years,” he said. “That will happen in Europe because the same people are going to put new EAFs on the site of old facilities. They’re going to a new facility on a brownfield site, so those could potentially be very disruptive to the industry. The opportunity for people in the recycled metal side is, can they develop a supply chain to support where some of those new facilities are going in that are both efficient and economic.”
While he lauded the efficiency of the domestic scrap market, Keenan said that not every scrap shipment is perfect. With so much new capacity on the horizon, he said some processes will have to evolve to better extract unwanted materials and improve scrap quality.
“Onshoring of manufacturing in North America is going to create greater amounts of prompt scrap,” he said. “We’re going to see that link. We’re already seeing that, and heavy manufacturing is going to come back to this country, and we’re going to have some huge infrastructure projects that are going to create a lot of scrap.
“You’re going to see a lot of demolition scrap. You’re going to see demolition scrap that’s coming from bridges that are going to get torn down, that are typically from BOF production from years ago, and it’s going to be a great quality of scrap that’s going into the system. We’re going to see a lot of barges and rail cars that are going to come into the system over time and that’s all BOF steel, so very low residual steels. If [low residuals] is your definition of quality steels, then I think we’re going to see a bit of that reservoir grow over time, as well as improved processing and picking.”
A vertically integrated EAF steelmaker and recycler, Nucor demands the highest quality of scrap possible, Saunders said, adding that the quality of products manufactured by its end users could be adversely affected otherwise.
“In general, we demand [high-quality material] and hold that accountable to all participants that supply raw material into our mills,” he said. “We need to make a quality product that ships on time and that performs as needed by our customers, and we expect the same thing from all of our suppliers, internal or external.”
Keenan said the steel scrap reservoir in the U.S. is likely to stay strong into the future and will be aided by stable collection and flow rates.
“Steel is the most recycled product material in the world,” he said. I can tell you that 65 percent to 70 percent of the steel that’s produced in the United States comes from recycled materials. … In this country we’re recycling 80-85 million tons of carbon-free steel every year, which is a phenomenal number.
“The other thing to remember is steel can be melted and remelted without loss of properties forever. That product is going to stay in demand. Better collection rates and more stable flow rates are going to be very important when we get to these kinds of numbers of consumption, if we start to cross 90 million tons of consumption in this country every year.”
Saunders echoed Keenan’s statement, adding that the story the industry needs to tell outsiders is that it is a mature industry with deep roots on both the supply and demand side, with a sound infrastructure for collection and processing and a sufficient scrap reservoir.
“[Steel] goes through its life cycle. We demolish or we recycle it, and we start that over and over again, so much so that we [account for] 70 percent of the steel produced in the best steel-producing and steel-consuming country in the world,” Saunders said. “It’s double what other countries [produce] because of that maturity of bot of our [scrap and production] industries. So, I think that it’s very important to understand that we are very sophisticated and we’re very mature and economics drive the whole scenario because of that maturity.”
Views from the supplier side
Moderating the Scrap Supply Focus, Sacco asked the panel if challenges existed when it came to increases in green steel production. George Adams, CEO of Orange, California-based SA Recycling, said there are varying degrees of what is considered “green.”
“If something is green, that means it’s supposed to be made with renewable energy,” Adams said. “But there’s certain grades of steel that are greener than others. If you make DRI [direct reduced iron], then put that in a blast furnace, then that’s greener than running iron ore. You can greatly reduce your carbon footprint by running DRI. But then, how do you make the DRI, and is that made with natural gas, made with hydrogen? There’s a million different ways.
RELATED: Scrap Expo 2024: Tips to reduce operating costs
“I don’t know that anybody is ever going to get a definition of green. There’s always going to be some steel that’s greener than others. And I think they’re going to start putting carbon credits for steel along the way, and they’ll start counting it that way.”
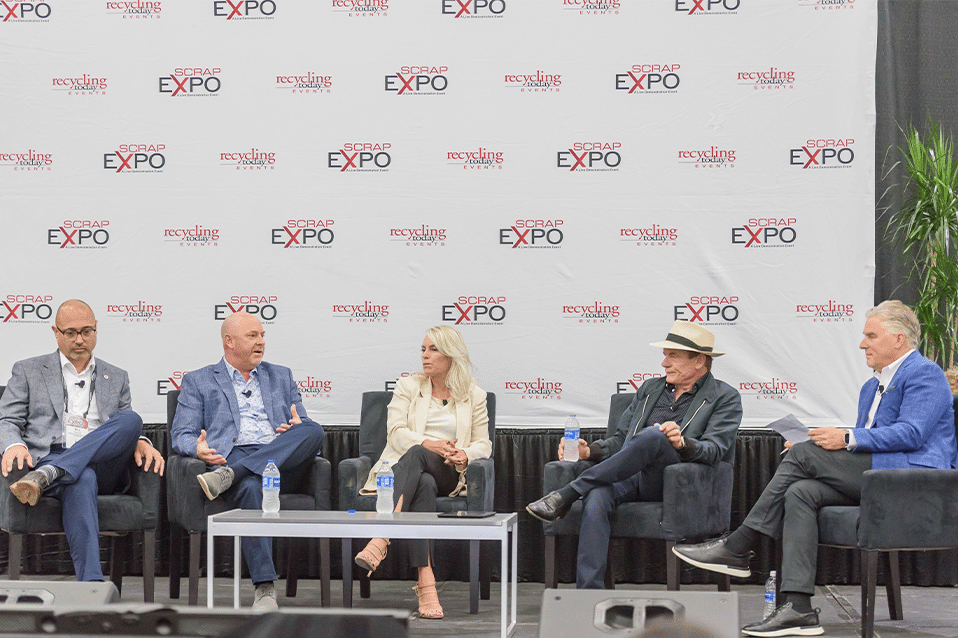
and John Sacco discuss material flows during the Scrap Supply Focus
at Scrap Expo 2024.
Matt Dykstra, senior vice president of the Ferrous Marketing Group at St. Louis-based Alter Trading Corp., which operates more than 70 recycling facilities in 11 states, said he didn’t foresee challenges in supplying EAF steelmakers in the future.
“There’s a lot of capacity coming online, but we’re a heavy net exporter,” Dykstra said. “There’s going to be a different flow of recycled metal, specifically around the Great Lakes region. … But we’re a very mature business. There’s a lot of metal to recycle here. Are we going to have less to export? Probably. But we’re not going to be a scrap-deficient nation by any means.”
Bill Sulak, president of Detroit-based Ferrous Processing & Trading Co., a wholly owned subsidiary of steelmaker Cleveland-Cliffs, added that there is no greener industry than recycled materials.
“This is what we do,” Sulak said. “Regardless of how it’s defined today, I see it as a tremendous opportunity for our industry, specifically from a procurement, processing and even transportation standpoint, if at some point they evaluate green steel as including Scope 1, Scope 2 and Scope 3 emissions.”
Looking at current flows of steel scrap, Sulak said operating rates are about 78 percent, though demand has remained strong and expects that to continue going forward. Dykstra agreed, noting that scrap flows have stayed consistent, though down slightly from 2023.
Nanci Schuld, co-founder, president and chief operating officer at Sandusky, Ohio-based FE Trading Group LLC, said in recent years different regions of North America have provided different levels of supply, though demand has seemed “fairly good” recently.
“I think we all believe that as this new capacity comes online that the demand should get better,” Schuld said. “And the U.S., at the minimum, should be in a situation where the supply of new steel is enough for the mills in the United States.”
Adams, whose company operates more than 140 recycling facilities across the U.S., said the country used to export 18 million tons of steel scrap annually, but that number has decreased to 15 million tons in recent years.
“You’ve got 18-plus million tons of new capacity coming online in this country. To me, that means we’re going to have a very large shortage of scrap,” Adams said. “I think now is the calm before the storm. There’s a lot of people that feel our scrap flow is increasing as the country develops, which is probably true, and they also feel as though imports coming from the Gulf [of Mexico] are going to offset a lot of that.
“I think there’s a lot of scrap-challenged and geographically undesirable places, like California, for example. Maybe that changes some of the flow. I still think some recycled steel will get exported, but I believe the vast majority will stay here in this country. All of our flows are going to dramatically change in the future as far as the way it’s going. With what’s going into Canada and Mexico, I just think there’s a massive change coming in this country.”
Scrap Expo 2024, hosted by Recycling Today Events, was held Sept. 17-18 in Louisville, Kentucky, at the Kentucky Exposition Center. The conference will return to the same venue in 2025 from Sept. 16-17.
Latest from Recycling Today
- Aurubis CEO says its metals play vital role
- Steelmakers await impact of tariff policy
- Radius loses money, says merger on track
- Electrostatic technology vies for role in ASR sorting
- ReMA board to consider changes to residential dual-, single-stream MRF specifications
- Trump’s ‘liberation day’ results in retaliatory tariffs
- Commentary: Waste, CPG industries must lean into data to make sustainable packaging a reality
- DPI acquires Concept Plastics Co.