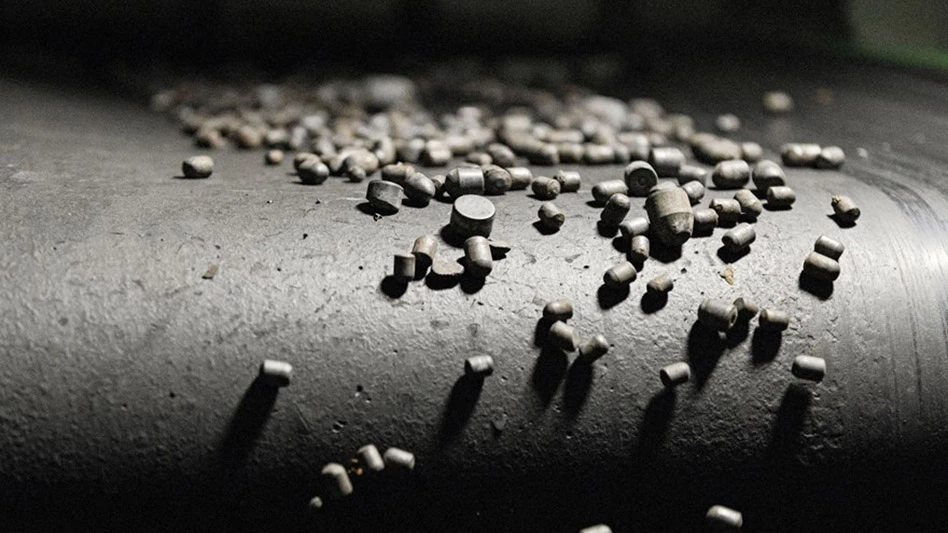
Photo courtesy of Sandvik AB
Sweden-based equipment manufacturer Sandvik AB has introduced what it calls the mining and quarrying industry’s first “opt-out” carbide drill bit recycling program.
“The initiative aims to transform the use of a material expected to run out within 40 to 100 years if consumption rates continue unabated,” says Sandvik regarding the tungsten found in drill bits. The mining, quarrying and construction drill bits made by the firm are made of cemented carbide, which includes carbon and tungsten alloyed with cobalt or nickel.
Sandvik describes tungsten as “a scarce and finite material.” In addition to the resource conversation aspects backing increased recycling, the company states, “Making tools from recycled carbide requires 70 percent less energy and emits 64 percent less CO2. It also reduces nitrous oxide emissions.”
The equipment firm has set as its goal to collect 90 percent of its own used bits by 2025. Other manufacturers’ used bits can also be recycled within the scope of the new program, according to Sandvik.
“Our breakthrough opt-out program supports our customers’ drive to mine more sustainably and demonstrates our commitment to delivering on Sandvik’s ambitious sustainability goals to halve CO2 emissions by 2030,” says Jens Holmberg, president of Sandvik Mining and Rock Solutions’ Rock Tools division. “We are determined to lead the industry into a new era, fully committed to embed circularity across an essential component of mining.”
Citing a 2020 World Bank report, Sandvik says the demand for certain minerals is estimated to grow 500 percent by 2050. “Recycling of drill bits is an important part of making the mining industry more sustainable,” states the company.
Historically, carbide recycling has faced several challenges, says Sandvik. “Collection of used products has been limited while carbide extraction has been cumbersome, inefficient and involved hazardous ways of working,” states the company. “The zinc recycling process has not returned the same quality of carbide performance, either.”
Regarding the early stages of the opt-out program, Holmberg says, “Customer response has been overwhelmingly positive. We need to transition our industry at an unprecedented speed. Our recycling program is one of many new initiatives you will see from Sandvik’s Rock Tools division moving forward.”
In an appeal to mining projects in remote locations, Sandvik is offering its customers what it calls extraction support. That part of the program is designed to “make it easier, faster and safer to recycle dull drill bits with a new patent pending method that will reduce emissions from transportation [by] 93 percent.”
Sandvik also has introduced a “Calmness of Recycling” campaign it says is designed to “address the stresses often associated with recycling.” Continues the company, “More people are now addressing their anxiety, stress and mental wellbeing, often with the use of relaxing and soothing online content.”
This campaign has started with a one-hour “relaxing” film that Sandvik says highlights the benefits of carbide recycling while “encouraging everyone to experience the calmness and wellbeing of recycling.” The film can be viewed on this web page.
Concludes Holmberg, “Our carbide recycling program is not only a good decision for the environment, it also creates a sense of calm about doing the right thing.”
Latest from Recycling Today
- EMR adds electric material handler to its Becker, Minnesota, operations
- Greenwave Technology pares back losses in Q3
- Lindner shredders prepare Brazilian plastic for recycling
- China ups steel output, while other nations cut back
- ReElement, Posco partner to develop rare earth, magnet supply chain
- Comau to take part in EU’s Reinforce project
- Sustainable packaging: How do we get there?
- ReMA accepts Lifetime Achievement nominations