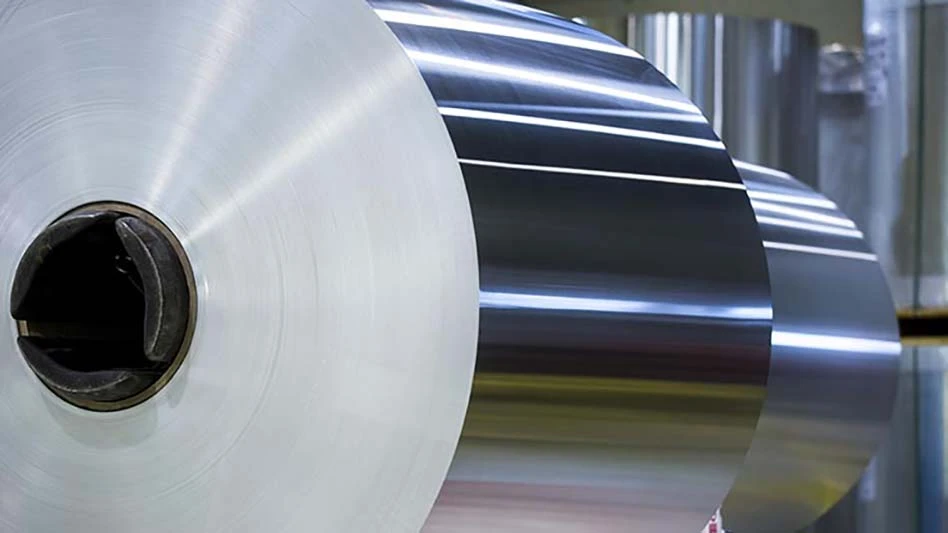
fotosr52 | stock.adobe.com
The SAFE (Securing America’s Future Energy) Center for Strategic Industrial Materials (C-SIM) has released a report titled “The U.S. Aluminum Industry’s Energy Problem and Energy Solution.” It is the first report in a series of policy papers about the issues affecting domestic primary aluminum production.
According to Washington-based SAFE, aluminum is critical to U.S. economic and national security through its use in defense, aerospace, electricity and transportation applications. Demand for the metal is predicted to grow as the economy transitions to green energy with the electrification of automobiles and other technologies. This report analyzes the dichotomy between increasing aluminum demand and its energy-saving benefits versus declining production in the U.S. given its energy-intensity production.
“As the aluminum sector is expected to rapidly grow over the next 20 years, the United States should evaluate whether it is likely to maintain a secure and reliable supply of primary aluminum, or whether vulnerabilities exist in the supply chain,” says Joe Quinn, C-SIM director. “Global demand is outpacing supply, so we can see a potential supply shocking coming. The U.S. has the power to avoid these damaging results by creating opportunities for industry to overcome current and future energy challenges.”
SAFE says that without action to stabilize and decarbonize domestic primary aluminum production, the country is at risk of increasing its reliance on the United Arab Emirates, Russia and China to meet its infrastructure, military and clean technology needs.
The C-SIM report recommends government leaders leverage new and existing policies, such as the recent Infrastructure Investment and Jobs Act and the Inflation Reduction Act, to ensure secure supply chains and improve environmental outcomes.
RELATED: The future of low-carbon aluminum
The report recognizes the growth of secondary aluminum production in the U.S., noting that it has doubled since the 1980s and uses 6 percent to 10 percent of the energy that primary aluminum production requires. However, it adds that despite these benefits and the growth of U.S. secondary production, “the aluminum industry is unable to transition entirely because recycled aluminum cannot be used for all applications,” noting that primary and high-purity aluminum is favored in the aerospace and defense sectors.
“Moreover, there is not currently enough scrap aluminum available to meet the rising demand for aluminum,” the report continues, particularly in light of companies’ and governments’ sustainability commitments. “The World Bank found even when recycling is at 100 percent and secondary aluminum is maximized to meet an increasing demand across its lifecycle, more primary is needed.”
Given that aluminum demand cannot be met entirely through recycling, the report says decarbonizing innovations in primary aluminum technologies can offer “a lifeline to industry as green aluminum becomes increasingly globally competitive.”
The report notes that when alumina goes through the smelting process, electricity runs through the mixture of alumina and an anode that is traditionally carbon-based, inducing a chemical reaction that splits the raw aluminum from the oxygen, which then combines with the carbon anode and is released as carbon dioxide. “The carbon emitted from this process is responsible for 13 percent of primary production emissions with an estimated carbon intensity of 1.5 t CO2 per ton of aluminum.”
The report notes that incorporating innovations, such as Elysis, in the smelting process, and sourcing electricity from renewable energy sources can help to decarbonize the primary aluminum industry in the U.S.
RELATED: Rio Tinto markets low-emissions aluminum can
Elysis, a joint venture between Alcoa and Rio Tinto, uses an innovative noncarbon-based anode, eliminating the carbon emissions in electrolysis, according to the report. “Inert anodes increase the economic viability of primary aluminum. While traditional carbon anodes need to be replaced every 25 days, ELYSIS’ inert anodes last for two years, reducing operating costs by 15 percent. With economies of scale, production of the anodes themselves could also become cheaper than carbon anodes. As such, BloombergNEF projects inert anodes are likely to become the industry standard for new smelters built from 2030 onward, with the potential to cost-dependently retrofit existing smelters as well.”
“A strong North American aluminum sector could become the cornerstone of an innovative manufacturing ecosystem benefiting a wide spread of industries,” say SAFE Founder and CEO Robbie Diamond. “Evaluating our options at this pivotal moment in the energy transition will ensure domestic supply chain resiliency and guarantee the United States will not cede its industrial future to adversarial nations. This matters to our clean energy, industrial, and military future. Aluminum personifies the opportunities and challenges the U.S. has as we seek to reindustrialize across the supply chain requiring both minerals and the cheap, abundant, reliable and clean electricity to process them.”
In the coming months, C-SIM says it will release additional reports examining domestic and global policy options for aluminum to preserve economic and national security while enabling a clean technology transition.
Get curated news on YOUR industry.
Enter your email to receive our newsletters.
Latest from Recycling Today
- AF&PA report shows decrease in packaging paper shipments
- GreenMantra names new CEO
- Agilyx says Styrenyx technology reduces carbon footprint in styrene production
- SABIC’s Trucircle PE used for greenhouse roofing
- Hydro to add wire rod casthouse in Norway
- Hindalco to invest in copper, aluminum business in India
- Recycled steel price crosses $500 per ton threshold
- Smithers report looks at PCR plastic’s near-term prospects