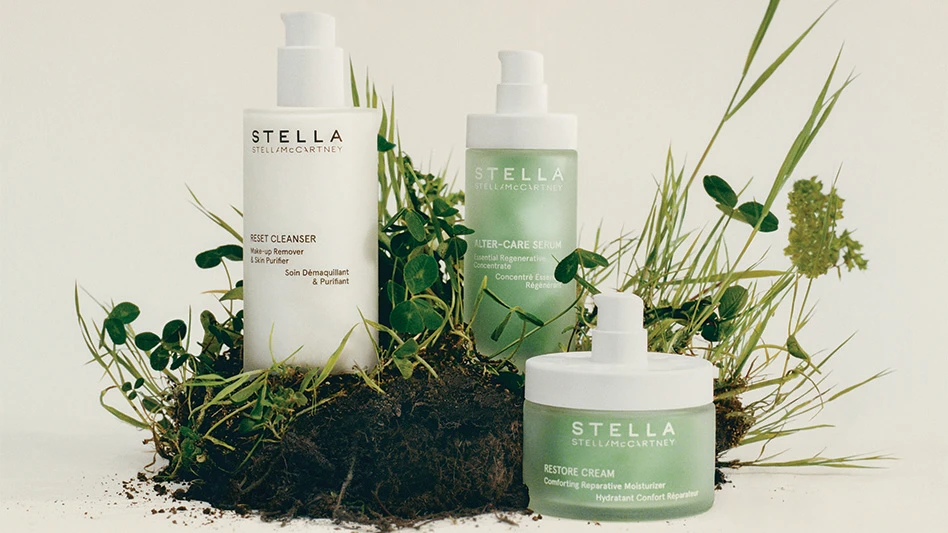
Image courtesy of SABIC
One of the biggest environmental impacts of a luxury cosmetic product is caused by its packaging.
According to SABIC (Saudi Basic Industries Corp.), a global chemicals company based in Saudi Arabia, its recent collaboration with London-based luxury fashion brand Stella McCartney brought about a “breakthrough” in lowering that impact.
By working with a trio of France-based plastic converters, SABIC developed new skin and eye care refillable containers for use with Stella McCartney Beauty’s Stella Alter-Care Serum and Restore Cream products using SABIC’s Trucircle portfolio of certified renewable polymers.
SABIC says the containers feature three of its polyolefin resins with a combined mass balance-certified renewable feedstock content of up to 90 percent and meet with the vegan branding of the cosmetics manufacturer.
“Stella by Stella McCartney is committed to minimizing [packaging’s environmental impact] as much as possible,” a SABIC spokesperson tells Recycling Today. “With a commitment to vegan and cruelty-free practices, the company was a dedicated partner looking to push boundaries in sustainable choices and bring these principles to the forefront.”
SABIC officially launched and presented the refill containers during Interpack in Dusseldorf, Germany, in May 2023, and the products have been introduced to the North American and United Kingdom markets.
“This innovation marks a significant step forward in transforming the packaging of cosmetics and skin care products to fully sustainable material alternatives,” Abdullah Al-Otaibi, SABIC’s polyethylene (PE) business unit general manager, says in a news release announcing the collaboration. “Moreover, it also demonstrates that our certified renewable polymers can facilitate the changeover by providing efficient drop-in solutions with no compromise in processability, purity, quality or convenience.”
The buildup
SABIC’s spokesperson says the project represents a breakthrough in the cosmetics industry because of the various sustainability aspects of the refillable packaging.
“Together with the refill concept of the durable Stella McCartney Beauty containers, the dedicated use of renewable raw materials aligns with consumer demands for more responsible packaging resources,” the spokesperson says. “In addition, once the containers have reached the end of their useful life, the value of the PP [polypropylene] and PE polymers can be recovered through established polyolefin recycling, making this concept a role model for sustainable packaging.”
The collaboration between SABIC and Stella McCartney was initiated by France-based plastics converter PRP Creation, which later was acquired by another French company, Texen. A SABIC customer also pitched the idea to the company.
According to the SABIC spokesperson, the company’s petrochemicals business supported the project and began working with stakeholders along the value chain, including Stella McCartney Beauty, barrier and multilayer film converter Leygatech, printing and lamination company STTP Emballage and Texen, which produces caps, jars and pouches. Discussions began at the end of 2021 and SABIC’s petrochemicals business agreed to supply the packaging materials by April 2022, a five-month process that aligned with Stella McCartney’s product launch timeline.
Partners in packaging
The product plan involved two components: the container head and body. The heads are molded by Texen using an impact-resistant grade of SABIC’s high-density polyethylene (HDPE) resin, and the container bodies feature a film made from SABIC’s linear low-density polyethylene (LDPE) that was supplied by Leygatech. The film is processed and printed by STTP Emballage, while flip-top closures on the containers are injection molded by Texen using SABIC’s PP polymer to complete the packaging.
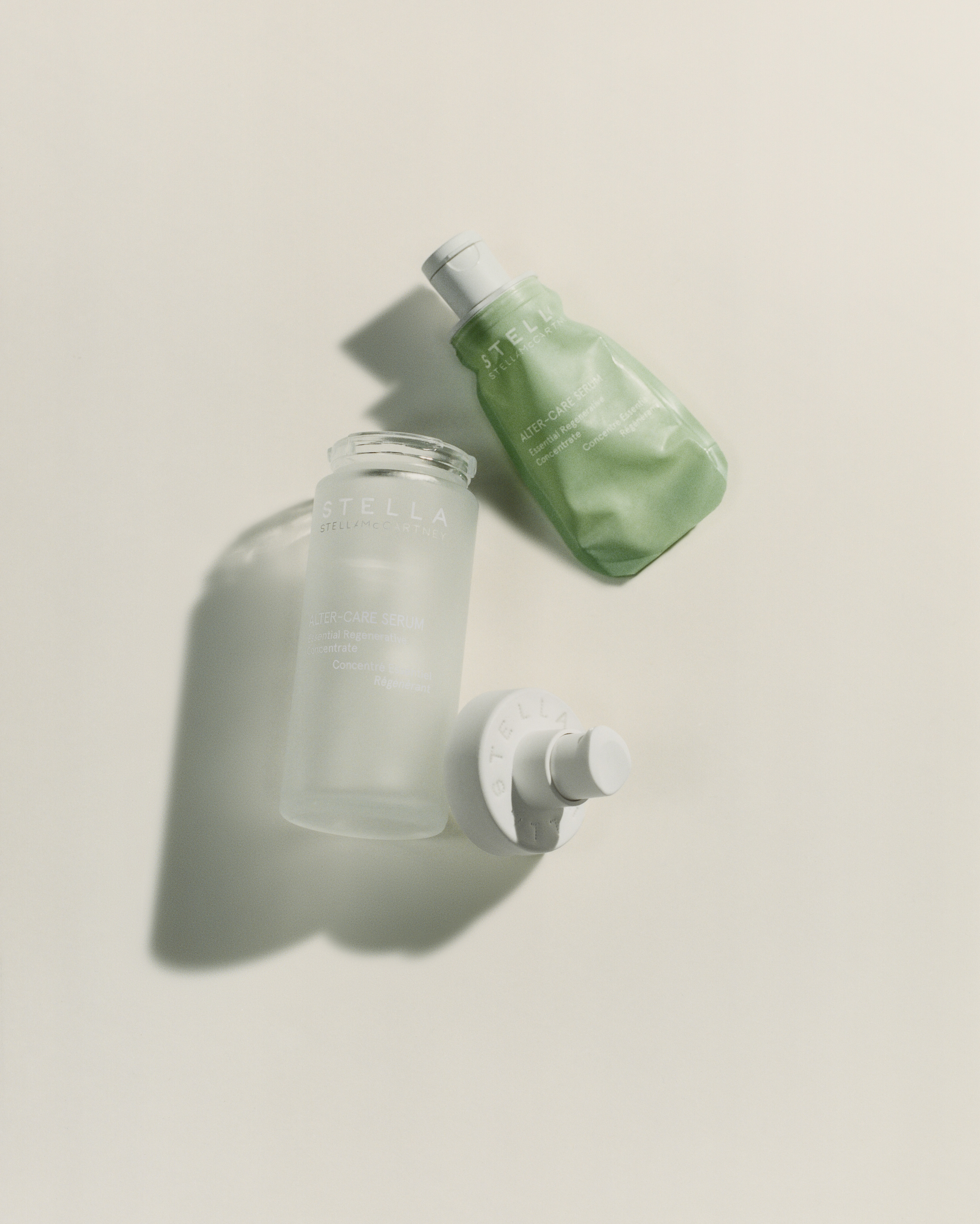
SABIC says its certified renewable materials containing bio-feedstocks help reduce the carbon footprint of the packaging, and the monomaterial packaging is easy to recycle and lighter in weight than glass bottles to reduce the energy required for transport. The company notes the refillable containers can be sold separately.
“This combination of factors sets a new standard for sustainable packaging in the cosmetics industry, and we believe it could encourage other brands to move towards using circular materials in packaging similar to what we have produced,” the SABIC spokesperson says.
The spokesperson adds that the company is committed to responding to challenges and discovering avenues that benefit its business and customers. “The successful launch of the new refill containers for Stella Alter-Care Serum and Restore Cream products was a result of close collaboration among all participating companies,” they say. “We were also able to adapt and overcome potential challenges faced during this journey and fostered a strong team spirit that ultimately helped bring the final product to fruition.”
Trucircle developments
SABIC says its Trucircle renewable polymers include various PP and PE materials derived from second- and third-generation renewable feedstock that is selected to avoid direct competition with human food and animal feed production and is not linked to any direct or indirect changes in land. The Trucircle portfolio also includes mechanically recycled polymers, ocean and ocean-bound recycled solutions, as well as closed-loop and design-for-recyclability services.
The company says a cradle-to-gate life cycle analysis has confirmed the sustainability of these polymers, concluding that each kilogram of the company’s bio-based resins reduces CO2 emissions by an average of 4 kilograms compared with fossil-based virgin alternatives while also cutting fossil depletion by up to 80 percent.
The mass balance of the renewable feedstock in the SABIC materials is validated by independent third-party accounting according to the widely recognized International Sustainability & Carbon Certification (ISCC Plus) program, following a set of clearly defined and transparent rules. The approach allocates the renewable content used in the production and conversion of the plastic materials to the ultimate application. The certification also provides traceability throughout the partners’ entire supply chain from the feedstock to the final product and allows brand owners to document the sustainability of their packaging to consumers.
The company has set a goal to make 1 million metric tons of the recycled-content resins annually by 2030, which it announced at the January 2023 World Economic Forum Annual Meeting in Davos, Switzerland.
“Our target of 1 million metric tons of Trucircle solutions by 2030 intends to help usher in the new circular economy,” SABIC’s spokesperson says. “Driving circularity for plastics will require a rapid transformation of the entire value chain, which is only possible through collective action, innovation and collaboration across the industry and ecosystem of waste management. Therefore, we are working hard with downstream and upstream partners to accelerate this process.”
Construction of the company’s first commercial unit in Geleen, Netherlands, is entering the final stages, according to the spokesperson, and deliveries of the first circular polymers are expected this year.
As a next step on the trek to meet its 2030 target, the company plans to increase volumes globally of bio-based materials, as well as advanced and mechanically recycled materials.
To lower its carbon footprint further, in 2023, SABIC signed a joint agreement with German companies BASF and Linde PLC to develop and demonstrate solutions for electrically heated steam cracker furnaces. The partners already have worked on concepts to use renewable electricity instead of the natural gas typically used for the heating process. The project recently hit a milestone with the installation of the last transformers for the demonstration plant.
“Thanks to novel heating concepts and by using electricity from renewable sources instead of natural gas, electric steam cracker furnaces, one of the most energy-intensive productions processes, can potentially reduce CO2 emissions by at least 90 percent compared to conventional technologies,” SABIC’s spokesperson says.
The demonstration plant will be fully integrated into one of the existing steam crackers at BASF’s Verbund site in Ludwigshafen, Germany.
The author is associate editor of Recycling Today and can be reached at cvoloschuk@gie.net.
Latest from Recycling Today
- Fitch Ratings sees reasons for steel optimism in 2025
- P+PB adds new board members
- BlueScope, BHP & Rio Tinto select site for electric smelting furnace pilot plant
- Magnomer joins Canada Plastics Pact
- Out of touch with reality
- Electra names new CFO
- WM of Pennsylvania awarded RNG vehicle funding
- Nucor receives West Virginia funding assist