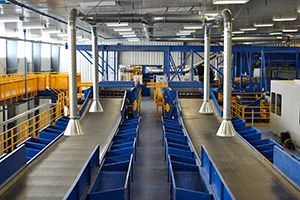
The waste and recycling company Rumpke, based in Cincinnati, has officially opened its new material recovery facility (MRF) in St. Bernard, Ohio. The MRF replaces Rumpke’s facility that was destroyed in a fire in April 2012.
The company invested about $32 million to build the new 100,000-square-foot facility on 10 acres. When fully operational, the MRF will be able to process 55 tons of recyclables per hour. The volume is a significant increase from Rumpke’s earlier facility, and has been built with the expectation that the company will be able to grow its volume to fill the facility’s capacity.
The equipment used at the facility was designed by Machinex and is expected to serve more than 4.5 million residents in the Cincinnati area.
Steve Sargent, director of Rumpke Recycling, says the company also has built the MRF with the concept that future growth will take place. One sector holding great promise is the possibility of commercial single-stream operations, which Sargent says he feels could help boost the tonnage the facilty processes.
Jeff Rumpke, vice president of Rumpke, says, “I am very proud of this new facility. However, I am more proud of our team and how we all pulled together in the hours after last April’s devastating fire to come up with a short-term plan that ensured uninterrupted service for our customers and a longtime vision to grow our business.”
Rumpke says before the company decided on what system to use, it visited nine MRFs, including three recycling centers in California, one in Rhode Island and five in Canada. Four different equipment systems were proposed and considered before Rumpke chose Machinex, Plessisville, Quebec.
"Machinex is extremely proud to partner with Rumpke on its state-of-the-art recycling facility,” says Pierre Paré, Machinex CEO. “This system is the achievement of a work team where both companies’ know-how and expertise have been combined. Machinex provided a custom design system that combined with the latest technologies on material separation.”
The facility includes six optical scanners, two electromagnetic eddy current separators, hundreds of spinning discs as well as nearly 100 employees. While the facility can sort 500 tons of material per day, Rumpke says it expects to double the number of tons processed with the opening of this facility.
“We designed our new facility with the additional capacity to handle growth as recycling increases in the region as well as provide the ability to process additional types of materials as new recycling markets become available,” adds Rumpke.
The company continues, “We are committed to growing the recycling effort. By investing in technology, we have increased the efficiency of recycling and we continue to drive down the cost to recycle. Today, we can go to a home or business owner, examine their waste stream and identify a variety of waste solutions offering maximum recycling opportunities at the lowest cost possible, making recycling a win environmentally and economically.”
Rumpke says the total speed of the optical scanner conveyors is up to 600 feet per minute. Also, to prevent fire the company has installed 1,700 sprinklers at the plant.
To give the facility as much flexibility as possible, the MRF has a 15,000-square-foot tipping floor, enough space to hold 2.5 million pounds of material. From there, the material is loaded onto one of two drum feeders, which spread out and regulate the amount of material entering the plant, allowing employees and equipment to efficiently sort the material. Material enters the plant at the presort station. There, employees remove material that can’t be processed or recycled.
Following the presort, recyclables travel through the cardboard screener, which consists of three decks of large spinning discs that separate the old corrugated containers (OCC) from other material.
Next, materials pass through the scalping screen, where the glass bottles are broken, allowing the broken glas and other small recyclables to fall to a deck below for additional sorting, while paper and other containers will ride over the screens.
From there, the material traveling over the scalping screens encounters five newspaper screeners, which are designed to remove ONP (old newspapers) from the recycling mix. Spinning discs allow the paper to ride over the top while other recyclables fall below.
The material then meets the angled sorters that separate the paper from containers. Fans blow the material and help paper to travel over the top of the machine while containers will roll off the side.
The next machine recyclables encounter is an overhead magnet, which attracts and removes steel cans from the material mix. Recyclables then meet the fourth optical scanner, which is designed to identify HDPE (high-density polyethylene) plastic. Next, the material travels through the eddy current, which removes aluminim used beverage containers (UBCs). Recyclables then travel through two more optical scanners to remove PET (polyethylene terephthalate) plastic and mixed plastic bottles and cartons.
Glass is one commodity that Rumpke, unlike many other recycling firms, is actively seeking. Rumpke estimates that roughly 15 percent of the recyclables coming through the plant will be glass. Along with glass, the company also will focus on ensuring that it can maximize the amount and quality of fiber it takes in. Rumpke says about 60 percent of the material it takes in is fiber. To grow its fiber intake, the company will be adding aseptic cartons to the mix of material it will be handling.
To accommodate the range of materials Rumpke says that the facility has 14 walking floor bunkers.
Latest from Recycling Today
- Paper recycling is focus of two January webinars
- Disruption likely for material flows in mid-January
- Blue Whale Materials to expand Oklahoma lithium-ion battery recycling plant
- CARI names new president and CEO
- Interzero revamps leadership structure
- Altilium secures $5M investment from Marubeni
- DOE report provides recommendations to increase recycling, reuse of wind energy equipment
- Sonoco makes leadership changes