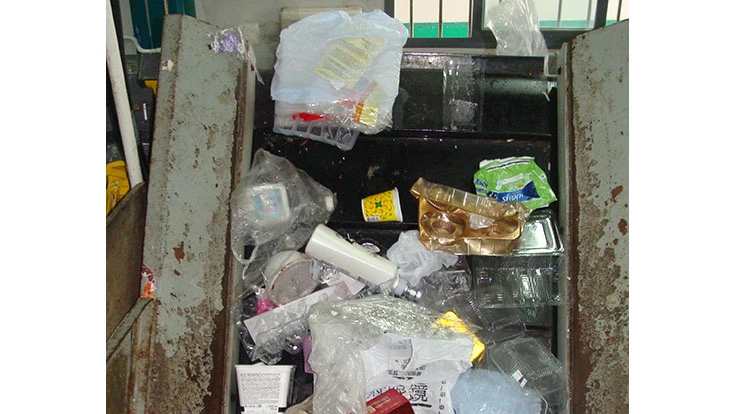
A coalition of industry groups and companies says it has conducted research showing that automated sorting technologies in use today can capture flexible plastic packaging, “potentially creating a new stream of recovered materials while improving the quality of other recycling streams."
The research is presented in a report from Ann Arbor, Michigan-based Resource Recycling Systems (RRS) titled “Flexible Packaging Sortation at Materials Recovery Facilities.”
The industry groups backing the report say it demonstrates that with adequate screening and optical sorting capacity, flexible plastic packaging can be captured efficiently in a single-stream material recovery facilities (MRFs).
Common forms of flexible plastic packaging include snack bags, resealable food bags, pouches for laundry detergent pods and pet food bags.
“Flexible packaging has many positive attributes—highly efficient, great product protectionand low environmental impact,” says Brad Rodgers, foods packaging research and development director for discovery and sustainability at PepsiCo, Purchase, New York. “However, recovery has been one of its weak points. This study is shedding light on pathways that can be deployed to improve flexible packaging end-of-life options.”
PepsiCo, along with several other corporations and industry trade groups, is a member of the Materials Recovery for the Future (MRFF) collaboration effort behind the report. The MRFF project brings together brand owners, manufacturers and packaging industry organizations that say they are committed to enhancing recovery solutions for flexible plastic packaging.
“We now know how flexibles flow through a material recovery facility and that the technology already exists for separating flexibles out of the materials streams,” says Larry Baner, senior packaging research scientist of global packaging and design for Nestlé Purina PetCare, St. Louis. “Although there is still a lot of work to be done to define the best way to separate flexibles from single-stream recyclables, this research moves us closer to solutions.”
This first phase of the research program sponsored by MRFF included baseline testing, equipment testing and a series of recovery facility trials to test existing sorting technologies commonly used in MRFs, such as screens and optical scanners. RRS developed the test methodology and conducted the research trials. Subsequent research will focus on further refinements to sorting technology, economic feasibility, assessing end-use markets for the material and developing a recovery facility demonstration project.
The three MRFs selected for baseline and MRF performance testing were chosen based on several aspects of their equipment configuration that made them well-suited for measuring the potential to sort flexible plastic packaging.
As each MRF is uniquely configured with many different combinations of equipment, building design and recovery capabilities, the MRFs used in testing had to be individually selected by reviewing numerous potential test locations in North America.
RRS sought MRFs with optical sorters on their fiber lines, hypothesizing that the majority of flexible plastic packaging would flow with the fiber stream and that optical sorting would provide the best option to recover the flexible plastic packaging from the fiber stream.
These factors resulted in choosing the following MRFs as test sites:
- IMS Recycling/CP Group, San Diego, was selected as the location for the baseline test to provide initial results that further testing would be compared against. The RRS report notes that IMS Recycling is a typical type of mid-life single-stream MRF serving the city of San Diego. The single-stream material at IMS Recycling is reflective of beverage container deposit states in general, with smaller-than-average bottle and container flow in light of the regulated deposit system there.
- Emterra, Surrey, British Columbia, was an optimal Test 1 site, RRS says, because of the optical sorting on the fiber lines, which fed directly from primary screens. The MRF is an advanced-design, single-stream MRF serving Multi-Material British Columbia (MMBC) and the British Columbia’s Vancouver/Surrey region. While the MRF is more modern than most U.S. MRFs, it processes a stream of materials similar to that received by many U.S. single-stream MRFs. The single stream material is reflective of deposit states in general (because of the beverage container deposit system used in British Columbia), with smaller-than-average bottle and container flow in light of the more aggressive deposit system there, RRS says.
- Emterra, Regina, Saskatchewan was chosen for Test 2. The Regina MRF is a single-stream MRF serving Regina and surrounding Saskatchewan. It has a similar sorting sequence to many newer U.S. single-stream MRFs. Its attractiveness for testing for the MRFF project was driven by the ability to send a mix of fiber and flexible plastic packaging to a series of three optical sorters through minor and easily reversible modifications to the equipment, RRS says.
The research finds that existing optical sorter and MRF equipment technology can be used to sort flexible plastic packaging at promising levels of efficiency. With some targeted adjustments of the equipment, identification and sorting of the seeded flexible plastic packaging improved dramatically.
Although the film quality levels generated were not yet optimal, it is expected that the technology can be optimized so that fiber product quality is concurrently improved, RRS says.
Following the testing, RRS has come to the following conclusions:
- Further equipment testing is needed to improve sorting of flexible plastic packaging through MRF equipment in a controlled environment. There is a need to focus on optical sorters and design of air flow control to optimize the separation of fiber from flexible plastic packaging. Improvements also be may possible through optimizing aim, pressure and port size of the ejectors or by using airflow capture for either the flexible plastic packaging or the paper. Some recognition improvement may be possible by working with equipment manufacturers to assure the optimum portion of the spectrum for recognizing flexible plastic packaging is used. Developing a community of practice to share knowledge among equipment manufacturers, operators and brands seeking next-life solutions for this material will accelerate equipment development to achieve greater sort efficiencies. Once the new design is successfully achieved in a controlled setting, a robust engagement of key stakeholders in the recycling industry and broader recycling community could help identify a MRF demonstration site for curbside collection testing in a community.
- End market assessment will provide a comprehensive evaluation of the full range of potential end markets. While an increasing amount of plastic film is being returned to packaging products, the majority of this consumption is in bulk extruded and molded products, such as plastic lumber. Much of the flexible plastic packaging stream will not be marketable to the existing plastic film market because it is made up of multilayer, multiresin construction. While a number of small scale processors are able to blend and mold these mixed resin materials into durable products, no large scale consumer with this capability has been identified to date. And no research has been performed that estimates the market for end products produced with these technologies. While some end market technologies have been explored extensively, others are in early research stages.
- MRF processing economic analysis is needed in the form of an updated net system cost analysis that considers the economics of installing new equipment to sort flexible packaging and its subsequent impact on revenues, costs, disposal and quality of paper after sortation to economically justify long-term change in MRFs, and to provide useful information to municipalities who may want to add flexible packaging to the curbside mix.
- Secondary processing economic analysis is needed as the MRF sorted flexible plastic packaging mix will require preparation by secondary markets to achieve full recovery. Greater understanding of the technical feasibility, environmental impacts and economic value of flexible plastic packaging secondary processing to meet end market feedstock requirements is needed. The costs of further sorting, cleaning and converting cleaned flexible plastic packaging to various products will inform proper investment and will be one input to the MRF processing economic analysis. Conducting feasibility analysis of the preparation for each market would provide understanding and cost data to project net system costs that establish a business case and prove an end form with value can be developed. Conducting trial testing with the most promising end markets will be necessary to confirm the feedstock is suitable for larger scaled applications.
- A community MRF demonstration pilot with a willing community MRF partner is the last step that would provide a brick and mortar demonstration site in a community that is eager to add more material to their carts. Once the cost-benefit analysis of capital costs, operating costs and secondary processing and market value is complete, private-public partnerships could pave the way for success of a market-based solution. The MRF would install the necessary equipment upgrades and provide a data set that could be evaluated by others
According to the report, promising technologies for further research include resin compatibilizers that could be added to new packaging and may improve the ability to recycle more of the flexible plastic packaging with plastic film. Similar additives possibly could be added when blending some laminated flexible plastic packaging to improve usability in a range of existing end markets. Other technologies include chemical and physical delamination processes and chemical recovery processes that allow reclamation of monomers and precursors that can be refined and used to make new polymers. Conversion technologies remain an alternative for some elements of the stream to allow recovery of useful chemicals and energy, the report states.
In addition to announcing its initial research findings, MRFF has welcomed three new members to the collaborative: Target, LyondellBasell and Plum Organics. Other MRFF members include Amcor, The Dow Chemical Co., Nestlé Purina PetCare and Nestlé USA, PepsiCo, The Procter & Gamble Co., SC Johnson and Sealed Air, as well as the Association for Postconsumer Plastic Recyclers (APR), the Flexible Packaging Association (FPA), SPI: The Plastics Industry Trade Association and the American Chemistry Council (ACC).
The 32-page report is available here.
Latest from Recycling Today
- Aqua Metals secures $1.5M loan, reports operational strides
- AF&PA urges veto of NY bill
- Aluminum Association includes recycling among 2025 policy priorities
- AISI applauds waterways spending bill
- Lux Research questions hydrogen’s transportation role
- Sonoco selling thermoformed, flexible packaging business to Toppan for $1.8B
- ReMA offers Superfund informational reports
- Hyster-Yale commits to US production