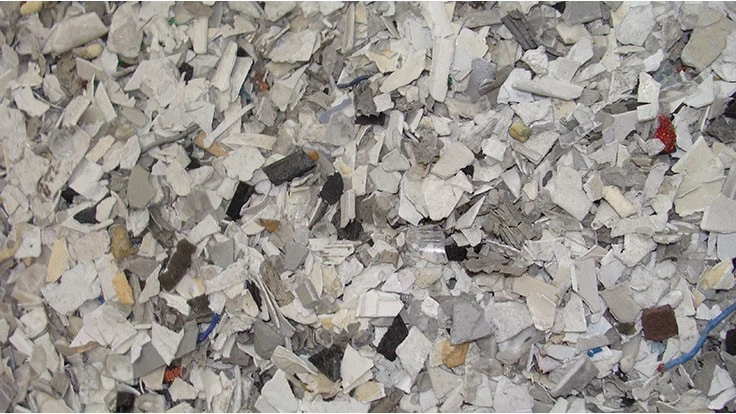
[The following article is based on a presentation given by Recycling Today Media Group Editor Brian Taylor at the Plastics & Rubber Processing Technology and Innovative Materials Application Summit 2018. That event was organized by Hong Kong-based Ringier Events and took place March 7-8 at the Shanghai Marriott Hotel Parkview.]
The official presentation title I was assigned is “Prospects for Plastics Recycling and Case Sharing.” In addition to that, I have informally given it a second title: “The good, the bad and the ugly.”
This refers to a film made in 1966. The movie is not about plastic or recycling, but rather cowboys and gunfighters. However, I think that series of words can very much be applied to the current state of global plastic recycling.
Some ugly circumstances
I am going to work my way backward through these three words and start with “the ugly.” To many people who saw it, there was a lot of ugliness on display in the 2016 movie “Plastic China.”
This 2016 documentary displays the reasons why mixed, post-consumer plastic scrap imports are no longer welcome in China. The movie shows this type of plastic recycling through the eyes of a family that works at and lives near a plastic scrap hand-sorting and processing operation.
Reportedly, this movie was viewed widely in China, including by top government officials, helping to prompt the restrictions that have been put in place. Critics of the sector portrayed in the firm referred to imported scrap materials as “foreign garbage.”
While political analysts may see the problem as a rift between China and the U.S. and Europe, there were people on both sides of the ocean benefitting from the prior trade, and people on both sides criticizing it.
The restrictions are now in place and likely to stay, and along with them have come efforts to collect more plastic scrap within China. This may be needed to help make up for the millions of tons of plastic scrap that used to be imported as industrial feedstock. That will create some of the opportunities—and technical challenges—for producers of plastic resins and compounds in this audience.
The accumulating volume of plastic in the world’s oceans is another reason why plastic—as a material—is being harshly criticized. Environmental and wildlife advocacy groups are ringing alarm bells about this. Yes, they are advocating for more recycling, but some in this community also are urging people, corporations and governments to turn away from plastic altogether. Plastic shopping bag bans have become widespread, including in Hong Kong where I live. Clearly, this type of reaction is not good for a lot of people in this sector, although it is a motivator for increased recycling.
The movement to ban some types of plastic has not stopped it from growing as a basic material. Each year, more plastic is produced, meaning each year, more obsolete plastic comes onto the market for recycling. However, while some metals and types of paper are recycled at a 70 percent rate in some parts of the world, plastic languishes with an estimated 10 percent recycling rate globally.
Technical issues are certainly part of the problem. Plastics producers have tight purity and color specifications—even tighter than those for metal alloy or white paper producers. So, when end-of-life plastic is collected in a commingled fashion, this creates instant discouragement for many producers of plastic who might otherwise consider using scrap as feedstock.
Automated technology does exist to sort plastics by resin and by color, but the fact that so much plastic is collected in a commingled fashion points to what could be an even bigger challenge.
Logistical hurdles
At the 2014 Eco Expo Asia in Hong Kong, Bertus Tulleners of Netherlands-based consulting firm TheRockGroup said this: “Many people tend to see recycling as a technical problem [and] we try to invent technical solutions. We need to organize the reverse logistics. It is more of an organizational question versus a technical question.”
I strongly agree with him, and I write about this factor often. The reason plastic scrap is both collected in commingled fashion and then compressed into a tight bale (which must be untied and becomes even more difficult to sort) is all about logistics. Whether you are shipping plastic scrap from North America to Ningbo, China, or merely from Shanghai to Ningbo, the economics of transportation weigh heavily.
If a plant produces polypropylene detergent bottles, or TPO (thermoplastic polyolefin) car bumpers or ABS (acrylonitrile butadiene styrene) that becomes a computer casing, the technology exists to recycle that plastic back into a like recycled-content resin.
But when those detergent bottles, automobiles and laptop computers end up in 34 different provinces in China, or in hundreds of nations around the world, how do you cost-effectively gather them together at the end of their useful lives?
The United States-based Reverse Logistics Association is full of people dedicated to figuring this out—and they do come up with best practices—but very few companies are willing to suffer enormous financial losses in an effort to close their own loop.
In the packaging sector, one additional constraint involves food contact rules. In the U.S., the Food and Drug Administration has set up protocols and test regimens that are emulated in many other parts of the world. These must be followed before recycled-content plastic can be used in many food, beverage and pharmaceutical packaging applications.
From what I’ve gathered living in this part of the world for five years, food safety is taken very seriously in China. Much like the “foreign garbage” imports mentioned earlier, it seems a matter of national pride to make improper food handling a thing of the past.
It appears, then, that plastic recyclers in China whose plastic is used in food packaging or serving applications must be extremely wary of skirting this boundary, lest they end up on the bad side of China’s Ministry of Environmental Protection (MEP).
I mentioned earlier plastic’s 10 percent recycling rate. Considering that some 320 million tons of plastic are produced annually, and only about 30 million tons are recycled. That means some 290 million tons are out there each year waiting for a recycling solution. This material is available and affordable.
Filling the gaps
When something is in ample supply, one generally can count on it being affordable. That is the case with most types of plastic scrap in the first quarter of 2018.
In February 2018, pricing services in the United Kingdom showed that virgin PET (polyethylene terephthalate) was selling for 65 cents per pound. At the same time, baled (mixed) PET scrap was being purchased for 1.5 cents per pound.
This points to a couple of circumstances: 1) the vast oversupply of plastic scrap on the global market in the first quarter of 2018; and 2) the amount of work necessary to upgrade that mixed, baled material to something closer to virgin quality.
When a spread is this large, however, it also shows that a manufacturer with access to nearby material has an incentive to find a way to use this affordable feedstock.
Globally, corporations are putting serious money into improving their own and the world’s plastic recycling rate. Coca-Cola, Alibaba, Procter & Gamble and McDonalds are among the global companies investing in alliances and plant and equipment to try to close their own loops.
In China, when both the five-year plan and Jack Ma are paying attention to recycling, follow-up actions are likely to occur.
On the government front, in January 2018, the MEP and the minister of housing and urban-rural development provided an update on a program requiring 46 cities to carry out “mandatory garbage sorting by the end of 2020” for public institutions and companies.
By the end of November 2017, 12 cities had adopted laws and regulations on such sorting, while 24 had introduced work programs related to the issue, according to the housing ministry.
So, that brings us right back to the people in this audience. If this material is being collected, what can and should plastics producers do with it?
Some non-governmental organizations (NGOs) advocate for closed loops, and they have coined the terms “upcycling” and “downcycling” to make a distinction. In this mindset, when a plastic bottle or auto bumper is converted back to its original form, that is “upcycling” and a victory for the environment. When a product is collected and recycled but becomes, instead, a traffic sign, a park bench or a railroad tie, that is “downcycling,” and can be met with disapproval.
I think financial stakeholders—the people buying plant and equipment to make plastic recycling a reality—have to be careful about this mindset. As observed earlier when I talked about logistics, that is what can make a recycling effort unprofitable in its earliest stages.
Recyclable plastic items confined to a closed loop will have to log many kilometers of travel, because there is no need to produce a pure, blue plastic compound in every city and province (because there are not blue detergent bottle or blue auto bumper factories in every province and city).
Helping fill in those geographic gaps can be factories that make composite items—like park benches, railroad ties or street signs.
Manufacturers like Trex Co. and EcoStrate LLC in the U.S. have travelled this route. Texas-based EcoStrate, won an award for its design and technology in 2017. Composite lumber products made by Virginia-based Trex use recycled grocery bags and other plastic films in its process. The company was founded in 1996. It is now publicly listed, its stock trades at $100 per share, and it has yearly sales of about $560 million.
And here in China, comparable composite recycled-content products are made in Anhui Province by Forestar. The company was founded in 2008, and like Trex it uses plastic scrap and wood residues to make its products.
Germany’s ALBA Group and France’s Suez are traveling a somewhat different path by working closely with virgin polymer producers. ALBA is building a plant in an industrial park full of petro-chemical producers. Suez has formed a joint venture with a global polymers producer.
Rather than thinking of recycled-versus-virgin materials as a competition, these companies are building alliances to have their recycled-content resins used as a blend in all types of applications. Time will tell how this idea works out.
Recycle or else
Corporate, government and NGO desires for sustainability can and do lead to more plastic recycling. But if progess is slow, and if closed-loop systems fail financially, we’ve already seen that NGOs will quickly move to their Plan B message: Let’s simply use less plastic.
The “Break Free from Plastic” alliance of more than 1,000 NGOs states as its goal, “to demand massive reductions in single-use plastics and to push for lasting solutions to the plastic pollution crisis.”
Among my closing thoughts, I’ll return to the earlier quote from the Dutch consultant. Even when a recycling technology barrier is lifted, it doesn’t mean much if logistical hurdles remain. A profitable plastic recycling business model starts with the logistics.
The other piece of advice I will venture to offer is, be wary of outsiders trying to convince you what is “good and bad” recycling, or “upcycling versus downcycling.” A closed loop is easier to explain than turning old bottles into car mats or street signs. When it works it does create a nice sustainability story to tell. But be careful of pursuing only a closed loop when other options are available.
Here is one more case study that is not as pleasing. I mentioned Coca-Cola earlier. It is a company that with the best of intentions squandered several million dollars in the U.S. attempting to help close its own loop. The company’s bottle-to-bottle recycling joint venture plant in the southern U.S. operated for less than two years before closing after an estimated investment of $60 million.
Certainly, the company and its consultants meant well and wanted a good recycling story to tell. But going “all or nothing” on a closed loop may just leave you with nothing.
Former U.S. President John F. Kennedy stated, “There are risks and costs to action. But they are far less than the long-range risks of comfortable inaction.”
Any business venture is subject to failure, and certainly not all makers of recycled plastic composite items will meet with success either. As China recycles more of its own internally generated plastic scrap, there are sure to be both winners and losers.
When looking at the plastic recycling landscape in 2018 and beyond, it is wise to be wary of the challenges. It may be equally wise (and profitable), however, to take advantage of the opportunities.
Get curated news on YOUR industry.
Enter your email to receive our newsletters.
Latest from Recycling Today
- Unifi launches Repreve with Ciclo technology
- Fenix Parts acquires Assured Auto Parts
- PTR appoints new VP of independent hauler sales
- Updated: Grede to close Alabama foundry
- Leadpoint VP of recycling retires
- Study looks at potential impact of chemical recycling on global plastic pollution
- Foreign Pollution Fee Act addresses unfair trade practices of nonmarket economies
- GFL opens new MRF in Edmonton, Alberta