
Photo courtesy of Republic Services Inc.
Leaders from Republic Services Inc. and Blue Polymers LLC have opened North America’s first Polymer Center and Blue Polymers plastics recycling complex in Indianapolis, where the joint venture partners say they will “transform” plastics circularity from curbside collection to consumer packaging and back again.
“The opening of the first Polymer Center-Blue Polymers complex is a significant milestone in advancing circularity for plastic packaging in Indiana and across the region,” says Jon Vander Ark, president and CEO of Phoenix-based Republic. “As a leader in environmental services, Republic Services is uniquely positioned to help meet customers’ demands for sustainable packaging and support Indianapolis’ vision to create a more resilient future.”
RELATED: Betting on quality
The Polymer Center and Blue Polymers facilities are designed to work together to produce more than 175 million pounds annually of recycled plastics for use in food-grade packaging and other applications. The Polymer Center is owned and operated by Republic, and Republic is a joint venture partner in Blue Polymers along with Luxembourg-based polymer recycling and distribution company Ravago.
The Indianapolis recycling complex includes two buildings totaling approximately 300,000 square feet. Together, the two operations are expected to create about 125 permanent, highly skilled local jobs.
The project received support through a grant from the Indiana Department of Environmental Management’s Central Indiana Waste Diversion Pilot Project; tax credits from the city of Indianapolis in conjunction with Develop Indy, the Indianapolis Department of Metropolitan Development and Employ Indy; Indiana Economic Development Corp. (IEDC) incentive-based tax credits, based on the company’s investment and job creation plans; and IEDC Hoosier Business Investment tax credits, designed to help companies invest in smart manufacturing and new technologies.
Making advancements
Indianapolis hosts Republic’s second Polymer Center facility, with the first having opened in Las Vegas in December 2023. The facilities process plastics collected from homes and businesses, including polyethylene terephthalate (PET), high-density polyethylene (HDPE) and polypropylene (PP). At each facility, PET is shredded and washed to produce recycled PET (rPET) flake, which is used to manufacture new beverage bottles. The HDPE and PP are sorted by color and type and then sent to Blue Polymers to be compounded, blended and pelletized, creating custom drop-in solutions for customers.
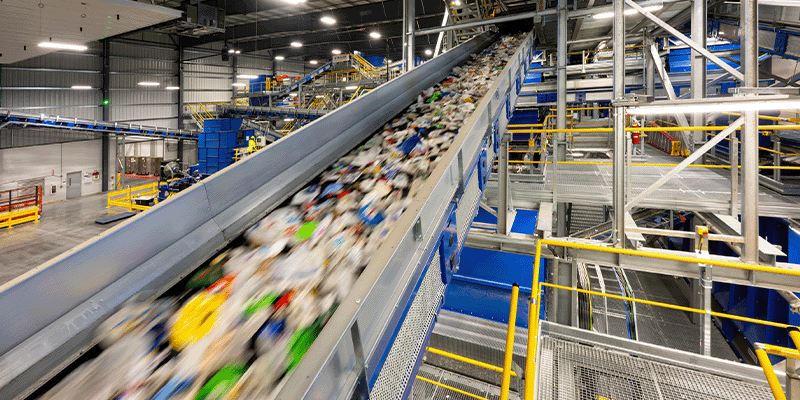
Republic Vice President of Recycling and Sustainability Pete Keller tells Recycling Today that olefins processed at the Las Vegas facility have been transported to Indianapolis to help provide the Blue Polymers facility with feedstock as it starts up, adding that the facility has been in a commissioning phase for close to 60 days. Overall, he says there is growing excitement for what the Indianapolis complex will be able to produce.
“We look at this as a forward integration in the plastics value chain,” he says, highlighting the Polymer Center’s ability to produce high-grade polyethylene (PE) and PP for food and nonfood packaging and provide secondary sorting of mixed-color resins. Over time, Keller says the facility will be able to sort blue- and green-colored material that could later be sold to specific customers.
Keller notes that a lot of PET goes into textile applications, such as clothing and carpet, but then is limited in its end-of-life recyclability. At the Polymer Centers, Keller says, “We’re real excited about the bottle-to-bottle [circularity] and the potential to keep that material in the marketplace multiple times. We have this sense that we can turn this material over six, seven times as opposed to turning it over once.”
Additionally, the process for recycling most HDPE jugs is designed to return them to store shelves in as few as 120 days.
Moving material
Republic operates 78 recycling facilities across the U.S. When it comes to the Polymer Centers, Keller says the company views them as working together in a “hub-and-spoke” model.
For the Indianapolis complex, he says materials will be sourced from Indiana and surrounding states such as Minnesota, Michigan but could extend to Missouri and Tennessee, for example. “We’ve got the opportunity to pull material in from western Pennsylvania and probably into northern Virginia. … The material wants to move.”
The company will primarily source plastic through residential collection, with a small percentage coming from commercial programs. Bales of PET, natural and mixed-color HDPE and PP will reach the Polymer Center for secondary sorting. While rPET flake will go back into bottle production, other high-grade bales will head to Blue Polymers, where they will be washed, purified, extruded and pelletized and blended based on customer needs.
“If a customer wants a 50-50 or 70-30 version of recycled content, or if they need certain masterbatches, certain colors or certain additives, we’ll have all those capabilities under one roof in Blue Polymers,” Keller says. “We’ll be able to produce batches of specific resin for specific customers.”
He adds that the Indianapolis facility’s capacity is 80,000 metric tons on an inbound basis per year and expects the Polymer Center to take in 75,000 short tons or more. While 100 percent of the olefins processed at the complex will be utilized by Blue Polymers, some PET will be made available on the spot market, though Republic has customers lined up for the majority.
“On the PET side, we keep a little in the spot market,” he says. “Some of that’s price discovery. We’re still kind of new at this. And some of it is just that we think it’s healthy to have a little ability to move material off to different customers month to month.”
The Indianapolis complex includes a rail spoke, giving the joint venture partners the ability to ship materials by truck or rail, though Keller says the majority of outbound material will move by truck, while a lot of inbound material will arrive via rail.
Building up
Acknowledging a process of continuous learning since the Las Vegas Polymer Center started operations, Keller says that as a “Generation 2” facility, the Indianapolis location has a few design elements not included in the former, though many details remain the same.
“I would say every project needs to be a little bit better than the last one, and that’s been applied here,” he says. “We have a perspective that Indianapolis has the most capable processing line of any facility that we’ve seen.
“We have the ability to take various grades of recovered resins from multiple markets and produce materials that are drop-in ready for packaging. That’s something that certainly we’re very excited about. … We think we’re going to be offering material to the market that the market has not had access to before, and what we hope to accomplish is to have high uptime, high yields and a consistent movement of material.”
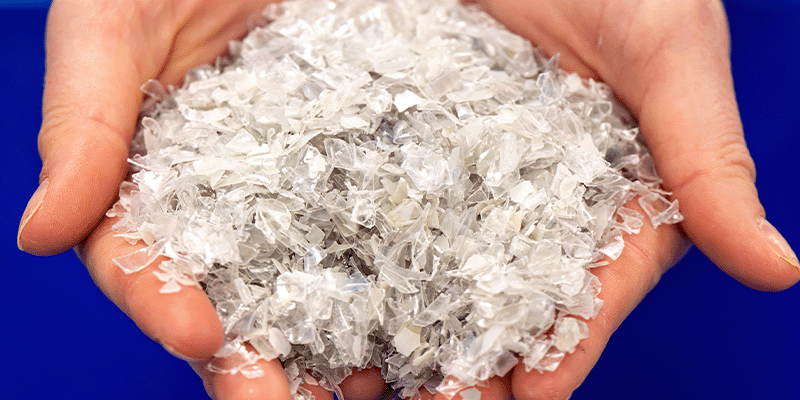
Similar to the Las Vegas facility, Indianapolis’ Polymer Center will utilize processing lines manufactured by German companies Stadler Anlagenbau GmbH and Krones. Keller says most of the equipment, which includes magnets, eddy currents, ballistic separators and air knives, for example, is used in traditional mechanical recycling facilities. While the Las Vegas Polymer Center has installed 19 optical sorters in its system, Indianapolis houses 22.
Additional equipment on-site includes a wet grinder, a series of dryers and silos and a flake sorter at the end of the wash line that can capture any material that might slip through the system.
Increasing supply
Keller says one of Republic’s focuses has been on now it can capture more material at the curb.
He surmises that single-use PET beverage bottles are collected at a rate of about 30 percent in the U.S. in terms of capture and recycling. His company is committed to increasing that number.
“For those folks out there that don’t think plastics recycling is real, we’d like to stress otherwise and encourage consumers, whether they’re on the go or at home, anytime there’s a rigid plastic package, please put it in the blue bin as opposed to the black bin,” he says. “We’d love an opportunity to be able to process captured material and, ultimately, get it back in the marketplace.”
Facility network
Republic’s first Polymer Center in Las Vegas has provided a learning experience for the company along with an outlet for bales of plastic. The facility, which at startup was expected to produce more than 100 million pounds of recycled plastics per year, has been progressing well, according to Keller.
“Within the last couple months, we’ve gotten to a steady state of operations where we’re shipping material as we’re producing it,” he says. “Demand is there for everything that we produce. We haven’t had an issue putting the [rPET] flake to market, and the majority of that material is going back into beverage containers.”
He notes that the ethylene and propylene plastics the facility accepts are being shipped to Indianapolis on a temporary basis and will eventually be sent to Blue Polymers’ under-construction facility in Buckeye, Arizona. He adds the Buckeye facility is expected to be operational late this year or in early 2026.
Republic intends to operate four Polymer Centers in the future, and Keller says the third will be located in the Northeast U.S. The company has not yet announced the location, though Keller says a site currently is under development.
Latest from Recycling Today
- Enfinite forms Hazardous & Specialty Waste Management Council
- Combined DRS, EPR legislation introduced in Rhode Island
- Eureka Recycling starts up newly upgraded MRF
- Reconomy Close the Gap campaign highlights need for circularity
- Nickel carbonate added to Aqua Metals’ portfolio
- EuRIC, FEAD say End-Of-Life Vehicle Regulation presents opportunity for recyclers
- Recyclers likely to feel effects of US-China trade war
- BCMRC 2025 session preview: Navigating battery recycling legislation and regulations