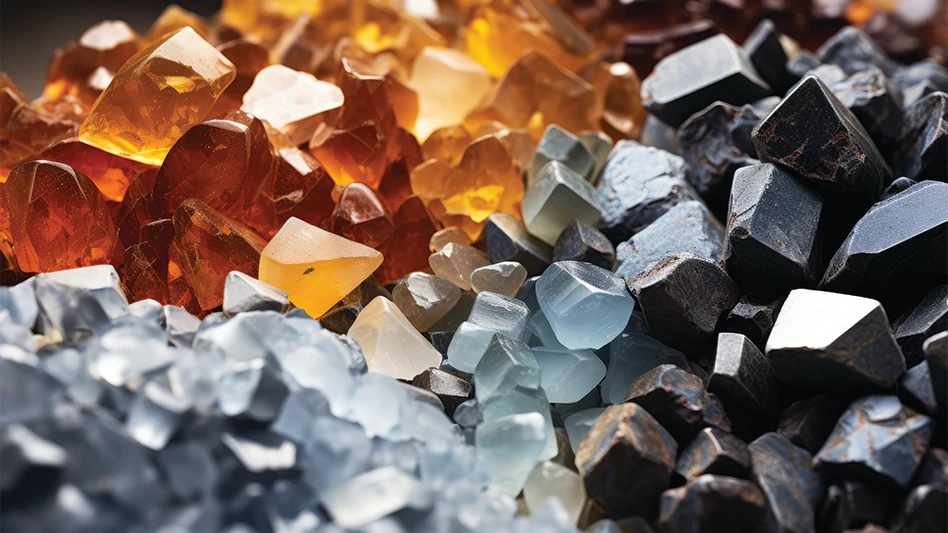
Anastasiia | stock.adobe.com
ReElement Technologies Corp., a rare earth and battery materials refiner and a wholly owned subsidiary of Fishers, Indiana-based American Resources Corp., has signed a memorandum of understanding with South Korea-based Posco International.
Under the agreement, ReElement will integrate its magnet recycling and rare earth ore refining processes into Posco’s global rare earth magnet manufacturing network. American Resources says ReElement will become the primary North American refiner supplying Posco with heavy and light rare earth elements, supporting Posco’s permanent magnet vertical as they satisfy nearly $900 million in announced original equipment manufacturer (OEM) contracts.
RELATED: Companies partnering to build battery recycling facility in Indiana | Hurricane-damaged vehicles could be a treasure trove for recyclers
Additionally, ReElement will recycle magnets and manufacturing scrap, reintroducing the materials into Posco’s production process. Together, the companies also will offer a circular supply chain solution for high-value magnet materials to Posco’s existing and future clients.
“We have been collaborating closely with the Posco team for several months and are excited about the opportunity to address rare earth element supply and sustainability challenges together,” ReElement CEO Mark Jensen says. “Posco’s extensive expertise and network in the permanent magnet industry and electrified economy enable us to drive efficiencies and implement impactful solutions where they are most needed.
“This partnership also highlights ReElement’s ability to catalyze and build a robust and sustainable supply chain. Additionally, we are confident that the unique strengths of our platform technology will enhance our capacity to source quality feedstock from around the world to support our current and emerging manufacturing base. Offering Posco’s North American and European OEM customers a diversified supply chain for rare earth magnets is key to reducing volatility and costs in electric transition.”
ReElement uses patented technology for the separation and purification of rare earth and critical battery material. Unlike conventional hydrometallurgical processes, the company says it maximizes surface area interface by using columns and resins, adding that it reduces capex, physical footprint, environmental impact and chemical usage and results in lower operational expenditures for mineral separation, purification and refinement.
The technology was developed over decades, drawing on expertise from commercially operating processes used in industries such as sugar refinement (for fructose and glucose) and pharmaceutical production, including commercial production of insulin.
Latest from Recycling Today
- Yolo County Central Landfill celebrates mattress recycling milestone
- University researchers create ‘low-cost’ plastic recycling method
- Biden administration delays enforcement of order blocking Nippon Steel, US Steel transaction
- Singapore researchers develop flame retardant removal process
- Getting mixed results
- Norsk Hydro buys remaining shares of Hydrovolt
- The Scrap Show: Dhawal Shah of Metco Ventures LLP
- AEPW releases new mechanical recycling ‘playbook’