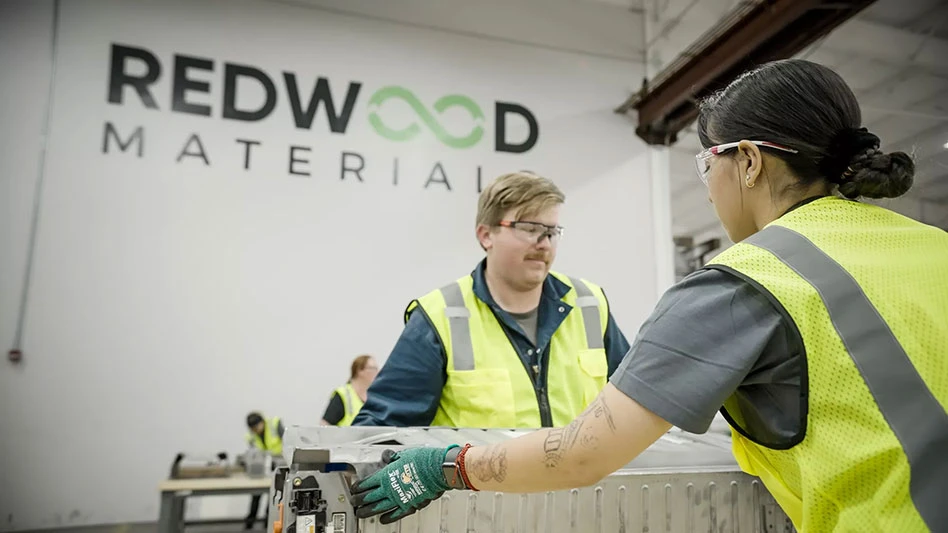
Photo courtesy of Redwood Materials
In February 2022, Redwood Materials launched an electric vehicle (EV) battery recycling program in California, which it calls the leader in the transition to electric transportation. The program has the support of Gov. Newsom and several automotive partners, including Toyota, Ford Motor Co., Volvo Cars, and Volkswagen Group of America. Redwood says its goal was to establish efficient, safe and effective recovery pathways for recycling end-of-life (EOL) hybrid and EV battery packs, and now it is sharing its findings.
In addition to the automakers listed above, Redwood says it worked with auto dismantlers to collect and recycle lithium-ion and nickel metal hydride (NiMH) EV batteries from EOL vehicles.
As the first wave of these vehicles are retired from the roads, California’s management of EOL battery packs will serve as a model for other states and the battery recycling industry, Redwood says.

Working directly with auto dealers, dismantlers and aggregators in California, the company says it identified and recovered 1,268 EOL battery packs that were a mix of older NiMH and newer lithium-ion chemistries, totaling approximately half a million pounds of material. The batteries, less than 5 percent of which were damaged, defective or recalled, were packaged and transported for recycling at Redwood’s facilities in northern Nevada. The company says its beginning to produce high-quality battery materials, anode and cathode that can be returned directly to U.S. battery cell manufacturers.
Redwood says it expects mixed battery chemistries to continue to be generated as older, hybrid vehicle models are retired in greater numbers from California roads. However, lithium-ion batteries (LIBs) represented the majority of the chemistry types collected, according to the company, which says it expects LIBS to continue to grow as they are the only type of vehicle battery on the market.
Logistics represent the most significant cost of battery pack collection and recycling, the company says. The key to reducing logistics costs is achieving economies of scale through increased collection volumes, Redwood says, adding that it is confident that as EOL pack volumes increase, this cost will decrease. The company says its recycling process for smaller batteries, such as those found in consumer devices, and production scrap is profitable.
Redwood says auto dismantlers “are core to creating the safest and most efficient recycling pathways,” and notes that Automotive Recyclers Association (ARA), Manassas, Virginia, and the California Auto Dismantlers and Recyclers Alliance (CADRA) have been “incredible partners.” The company adds, “Everyone we worked with in the dismantler community wants to do the right thing, and they were excited to partner directly with Redwood to ensure responsible recycling. The dismantler community helped us to establish the most efficient transportation routes and aggregate batteries at their central locations and, in return, they were appreciative of the knowledge we shared on handling, packaging and transporting EV packs.”
The company says it supports public policies that govern the safe collection, transport and handling of EV packs and would encourage the industry and policymakers to focus on lowering transportation costs without compromising safety. “Existing regulatory frameworks were not intended to address recycling pathways for large electric vehicle battery packs,” Redwood continues. “This is a major opportunity to update these regulations to address the modern EV era while continuing to ensure the safe collection and recycling of these packs without adding additional fees that could inadvertently increase the costs of EVs.”
Redwood says vehicle original equipment manufacturers (OEMs) want to responsibly manage their EV batteries, as evidenced by Redwood’s partnerships with automakers in this pilot. An extended producer responsibility (EPR) approach could be effective, according to the company, but such policies should allow automakers to partner directly with recyclers or to recycle the batteries themselves. This is paramount to ensure the market manages EOL batteries in the safest and most efficient manner while avoiding unnecessary costs to the battery value chain. It also presents an opportunity for the industry to drive down the costs of future domestic battery production and pass those savings to consumers, Redwood adds.
However, the company says mandating a singular producer responsibility organization for EV battery recycling, similar to certain electronics recycling frameworks, is not appropriate for EOL EV battery packs. Instead, EPR programs can ensure best practices and responsible EOL management without choosing winners and losers.
Automotive OEMs also must collaborate directly with recycling partners that can sustainably manage the materials throughout the supply chain, collecting and recycling EOL LIBs and refining the materials sustainably into “battery-grade” metals that can go directly back into battery component production, Redwood says. “It is essential that recyclers have the capability to produce ‘battery-grade’ refined metals,” the company writes. “Without this capability, we will end up with a chain of recyclers producing only intermediates, adding to costs and increasing the likelihood that critical materials could end up overseas instead of being reused in batteries to support the United States’ electrification goals.”
The company adds that proposals or actions that add extra costs to the EV battery value chain will put California and the U.S. at a competitive disadvantage during this transition toward clean energy and electrification.
The Inflation Reduction Act (IRA) recently incentivized critical mineral and battery component requirements for EV batteries. To attain compliance, battery makers and automotive manufacturers will need a reliable, domestic supply of recycled content and battery materials, Redwood says, adding, “Our program demonstrates the strong market for these materials within the U.S., especially considering the recent expansion of the Clean Vehicle Credit through the IRA.”
Redwood says its experience makes it “clear that the market economics for EV battery packs and the valuable metals they contain provide an increasingly strong incentive for responsible end-of-life management.” The company asks policymakers to ensure responsible management of EOL batteries with incentivizes similar to the policies established by the IRA. “We also urge policymakers to be mindful that, while still in the early stages, market forces and industry partnerships are already at work to create safe, efficient and sustainable pathways for end-of-life batteries.”
Latest from Recycling Today
- Volvo CE dealership in Canada changes hands
- Takeuchi adds Southwestern US manager
- McNeilus unveils fully integrated, electric front-loading collection vehicle
- CalRecycle releases SB 54 updates as new year begins
- Regenx receives funding from the National Research Council of Canada Industrial Research Assistance Program
- GFL Environmental Inc. to sell majority stake in Environmental Services business to Apollo, BC Partners
- SPR launches automated bifacial solar panel recycling line
- MBA Polymers UK offers ABS to global market