
Trex Co. Inc. says it has become the world’s No. 1 decking brand because it offers the most innovative, technologically advanced products available today, and that innovation began by combining recycled plastic with reclaimed wood to create a maintenance-free decking product.
Today, recycling remains a cornerstone of the company’s manufacturing process, with Leslie Adkins, vice president of marketing and ESG (environmental, social and corporate governance) development, saying it is “key to our material inputs and to our financial performance.”
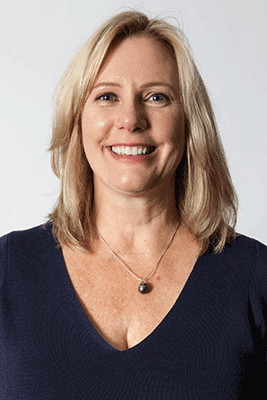
Adkins has been with Trex for 15 years, performing a variety of roles during that time. She has been in her current role since 2017. “In this role, I expand and extend my consumer brand and marketing experience to help steer the company’s ESG efforts,” she says.
Trex operates manufacturing facilities in Winchester, Virginia, which also is home to its corporate office, and in Fernley, Nevada. Its third manufacturing facility in Little Rock, Arkansas, is expected to come online in 2026. At these sites, Trex takes scrap polyethylene film, shredding and grinding it into small flakes. “Some of those flakes are extruded into pellets based on the variation and contamination levels,” Adkins says. “Then, the pellets or flakes are mixed with ground wood chips, and the material is heated, mixed and extruded into Trex decking products.”
In the following interview, she shares how Trex came to embrace recycling and the company’s evolution in this area.
Recycling Today (RT): What first led Trex to use recycled content in its products? How has the company’s use of recycled content evolved over time?
Leslie Adkins (LA): Founded with the belief that innovation can turn trash into treasure, Trex introduced the innovative idea of combining plastic film with wood sawdust to become durable decking boards that would perform better than wood. From that invention spawned the composite decking industry more than 30 years ago, and [it] has evolved over time as Trex has honed our supply chain and proprietary processes to offer a range of beautiful, high-performance, eco-friendly outdoor living products in a variety of colors and finishes, available at scale.
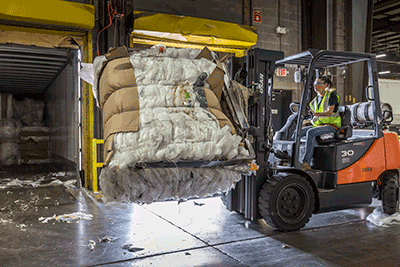
RT: How much and what types of plastic does Trex recycle in a typical year? How much of that material is consumed internally versus sold to other manufacturers?
LA: Trex is one of North America’s largest recyclers of polyethylene (PE) film (comprising shopping bags, pallet wrap and packaging), and in 2022 the company diverted more than 330 million pounds of plastic film that otherwise would have gone into landfills. Instead, we integrated it into our manufacturing process to create the world’s No. 1 brand of composite decking that provides decades of enjoyment without warping, rotting, fading or needing to be resealed.
RT: How does Trex source the plastics it recycles? Is most of the material collected through the NexTrex program? Can you talk a bit about how that program originated and how it may have changed over time?
LA: Trex sources recycled plastic film from:
- Postretail sources that include stores that use plastic bags or wrap in back-of-house operations before items reach the sales floor. This allows many of our commercial partners to offer cost-effective circular solutions for their plastic film waste. These retailers include Rent the Runway, L.L. Bean, REI and Urban Outfitters. We continually seek new partners in industrial, consumer and agricultural sectors whose waste PE can be purchased and upcycled into our products.
- Postindustrial sources, including manufacturing hubs and/or distribution centers that frequently use plastic film to wrap pallets for transport.
- Postconsumer sources, such as used plastic bags, wrap, bubble mailers, dry cleaning bags and other packaging that end users deposit in our NexTrex bins in retail stores, such as Kroger and Safeway, as well as other community collection points. The NexTrex program started as a school recycling program where children could learn about and participate in recycling and has since expanded to include a variety of community and civic organizations.
RT: What is the company’s overall philosophy when it comes to recycling and sustainability?
LA: Since Trex was founded 30 years ago, our company has operated on the belief that we can turn trash into treasure. Trex makes beautiful outdoor living products that homeowners can enjoy for decades with little maintenance, and we make those products from recycled and reclaimed content. This allows us to attain financial success while taking care of our employees, our shareholders, our communities and our planet.
More recently, in 2022, we initiated a program as the first step towards a whole-life strategy to divert construction offcuts and end-of-life Trex decking from landfills. While Trex decking from our earliest days is still in use across the country and the world, it is important that we support future generations who may desire to replace their existing composite deck with new Trex decking.
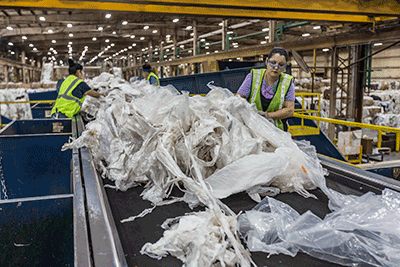
Having been in business for approximately 30 years now, Trex would love to be able to recapture and recycle Trex decking that is reaching its end of life. That, however, poses considerable challenges in terms of logistics. We do not know where those decks are nor when those decks might be replaced.
Accordingly, we are focusing on potential recycling opportunities closer to our sphere of influence. For example:
- When we know of a commercial project where a large number of cuts will be made and therefore a large volume of Trex scrap, we work to set up collection bins and arrange for that waste to be brought back for recycling.
- Similarly, when creating our merchandising and displays, some Trex waste is generated. We set up programs with our third-party vendors to collect that waste and return it to our facilities for recycling.
- We also pursue opportunities with our distribution partners to collect waste generated at their locations for recycling.
- When feasible, we also seek to recycle decking that is being replaced through our claims process—whether the claim arises in the channel or at the build location.
These are small steps towards our goal of minimizing the amount of Trex decking that ends up in landfills and intercepting that material for another round of recycling.
Additionally, we constantly seek to reduce the materials used in our packaging, recycle water used in our manufacturing and seek to optimize our use of energy to reduce our GHG emissions.
RT: With the removal of the Film Drop-Off Directory, which was housed at BagAndFilmRecycling.org, is Trex worried that store drop-off of plastic film will be reduced? If so, how does the company plan to address that?
LA: No, we are not concerned that store drop-off plastic film will be reduced as our NexTrex Film drop-off directory and collection network is, by far, the leader in communicating consumer drop-off locations where collected film truly is recycled. Over the years, the reporting accuracy of the Film Drop-Off Directory had declined to the point that many of the drop-off locations did not have collection and many of those that did have collection did not have a recycling solution, resulting in the collected materials going to the landfills.
RT: Did the ABC News investigation that put Apple Air Tags into bundles of plastic bags contribute to a decrease in the film recovered from retail locations, making it harder for Trex to source material?
LA: Trex was one of the few bright spots in the ABC News investigation as we were one of the only examples of the bundles reaching a recycler. The problem of plastic film waste cannot be solved by Trex alone; however, we are proud to do our part and as we grow, we grow the amount of plastic film that is recycled.
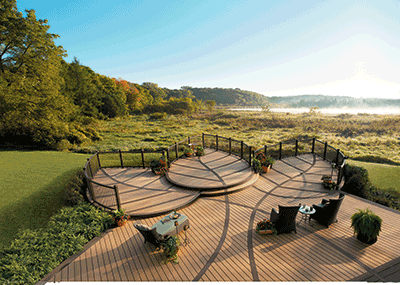
RT: You were recently awarded “2023 Recycling Education Program of the Year.” How critical does Trex feel recycling education is and how does it view its role?
LA: Trex believes that education is critical to increasing recycling as is evident by our long-standing school recycling programs. We welcome increased recycling efforts and position our company to be a small but commercially viable means to reduce the amount of plastic film waste.
RT: Some MRFs are beginning to recover film for recycling. How does Trex feel about film recovered from residential recycling programs?
LA: Trex is actively working to expand our raw material streams to include sources such as MRFs. In an ideal world, all consumer scrap film would be collected separately to reduce variability and contamination, but not all consumer scrap plastic can be collected via store drop-off. Accordingly, Trex continually evaluates scrap plastic collected in current and emerging programs to effectively utilize in our manufacturing processes.
Latest from Recycling Today
- Open End Auto Tie Balers in stock, ready to ship
- Reconomy names new chief financial officer
- ICIS says rPET incentives remain weak
- New Jersey officials award $16.2M in annual recycling, waste reduction grants
- Linder Industrial Machinery announces leadership changes
- First phase of EPR scheme launching in Alberta
- Veolia technology helps PetStar with water conservation
- Athens Services terminates contract with San Marino, California