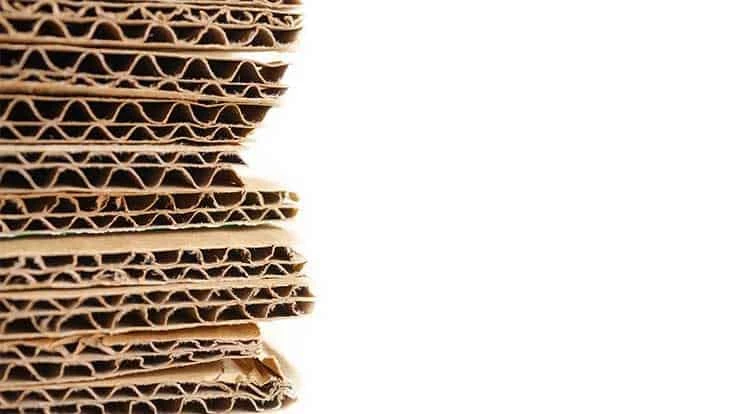
© Piman Khrutmuang | stock.adobe.com
In recent years, finding homes for some recovered fiber grades has become challenging for U.S. recyclers as a result of China's scrap import policies and overcapacity at domestic mills. Both mixed paper and old corrugated containers (OCC) have been in oversupply in the U.S.
Yet, in the U.S. Pacific Northwest, opportunities to consume recovered fiber are expanding.
A national broker for recovered fiber reported to Recycling Today in November 2019 that the domestic market is improving, particularly in that region.
“The domestic market [in the Pacific Northwest] is solid, and it’s just going to get that much stronger,” the national broker said in November 2019.
Several companies already have a presence in the region and are actively consuming recovered fiber, including Atlanta-based WestRock; Memphis, Tennessee-based International Paper; and Atlanta-based Georgia-Pacific LLC. But more companies are adding capacity to consume recovered fiber in this area, including Port Townsend Paper Corp.’s upgrades to consume OCC in 2019; Mexico-based Bio Pappel’s McKinley Paper Co. planned restart of a mill in Port Angeles, Washington, this year; and Packaging Corp. of America’s plans to add 350,000 tons per year of OCC pulping capacity at a mill in Wallula, Washington.
One company has announced plans to expand its ability to consume recovered fiber in direct response to National Sword and its impact on recyclers in the region. North Pacific Paper Co., Longview, Washington, has announced plans to consume more than 400,000 metric tons per year of OCC and mixed paper combined, turning it into items such as linerboard, corrugating medium, heavyweight bag grades, lightweight bag grades and specialty kraft papers.
Craig Anneberg, CEO of NORPAC, said in a news release issued in August 2019 that he anticipates converting about one-third of NORPAC’s production to packaging grades while solidifying the company’s future as an independent producer of packaging and communication papers, including super-bright and book papers, copy paper and newsprint.
“Today, our state faces an unprecedented environmental challenge from waste papers because of China’s new, more stringent restrictions on unsorted and high-reject content waste papers,” Anneberg said at the time news of this expansion was announced. “By increasing our ability to produce 100-percent-recycled packaging papers, our company will be able to help solve this challenge, transforming waste papers into much-needed packaging-grade papers for local and export markets.”
Making changes in Longview
Although NORPAC is today focusing much of its time on producing packaging materials, the company initially started in 1979 as a newsprint producer. As newsprint demand declined in more recent decades, the company diversified to produce book paper and freesheet copy paper. But Tom Rozwod, who oversees external affairs at NORPAC, says in the past few years, demand for printing and writing papers also has declined.
“Printing and writing papers are just on a perpetual decline to the point where in October of 2017, we actually shut down a paper machine and had to lay off people,” he says.
To improve business and expand to consume more recovered fiber, Rozwod says the company decided to start producing packaging materials about two years ago. In the spring of 2018, NORPAC restarted its shut-down paper machine to make packaging materials instead. NORPAC is producing linerboard, medium and some kraft brown bags.
“It’s been quite a product development journey for us over the last decade,” Rozwod says.
“We had to shut the machine down in late 2017—it would have still been down today if we were still trying to put printing and writing grades on it,” adds Jay Simmons, product development manager at NORPAC. “But we saw an opportunity to get into the packaging sector; we could expand our employee base and hire back people.
“We’ve rapidly grown in the packaging sector,” Simmons continues. “It was a bit of a shock to go from always making printing and writing grades to packaging grades, and it took some of our employees by shock. But we have a very highly capable group of operations and technical support.”
Getting into packaging also has helped the company to consume more recovered fiber. Simmons says NORPAC uses mostly mixed paper and OCC for its packaging products. This factor, he adds, has helped recyclers in the Pacific Northwest to find homes for scrap paper, as well. In particular, he says the NORPAC mill has helped to find new homes for mixed paper in the region.
“There have been announced capacity expansions in the Northwest,” Simmons says. “Port Townsend’s mill expanded, but [it’s] using OCC. The Port Angeles mill, which is slated for startup in early 2020, is slated to use OCC. [The Packaging Corp. of America] mill in Wallula, Washington, is slated to use OCC. And the Georgia-Pacific mill in Toledo, Oregon, is supposedly using mixed paper, but it’s industrial mixed paper.
“Everyone that’s expanding is expanding with OCC, not mixed paper,” he continues, adding that NORPAC’s mill is now helping to consume some of the overcapacity of residential mixed paper in addition to OCC.
Simmons says NORPAC’s mill is currently at full capacity. However, he adds that the company plans to continue growing in packaging and could require more recovered fiber in the future.
Latest from Recycling Today
- ReElement, Posco partner to develop rare earth, magnet supply chain
- Comau to take part in EU’s Reinforce project
- Sustainable packaging: How do we get there?
- ReMA accepts Lifetime Achievement nominations
- ExxonMobil will add to chemical recycling capacity
- ESAB unveils new cutting torch models
- Celsa UK assets sold to Czech investment fund
- EPA releases ‘National Strategy to Prevent Plastic Pollution’