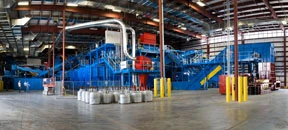
ReCommunity, headquartered in Charlotte, N.C., has started up its newest material recovery facility (MRF) in Tucson, Ariz. The MRF, designed, manufactured and installed by CP Group, San Diego, will be able to process 25 tons of recyclables per hour, according to ReCommunity. The installation was completed in July, and the facility is now in full operation.

“We are committed to leading the recovery revolution for forward-thinking communities by repositioning waste as a strategic community resource instead of a growing liability,” says Sean Duffy, ReCommunity president and COO. “Our ability to create significant positive gains for our community partners hinges on leveraging world-class operational and design expertise for our facilities.”
Duffy continues, “Tucson is a gleaming example of the end result of combining ReCommunity’s operational expertise and knowledge with CP Group’s design flexibility and experience. The result is a well-designed plant that will serve the Tucson community for years to come.”
The system includes advanced automated sorting capabilities that allow identification, separation and recovery of recyclables. The system features equipment and services from CP Manufacturing, MSS Inc., IPS Balers and Advanced MRF, all divisions of the CP Group.
Josh Wagner, CP Group project manager for the Tucson facility, says, “The Tucson plant runs on a dynamic mix of highly experienced ReCommunity operators and CP Group technology. The seamless plant startup was due to the cooperation and teamwork of both ReCommunity and the CP Group. We look forward to the continued successful operation of this system, which we are exceedingly proud of.”
The system features a three-deck scalping screen, a three-deck OCC screen, a three-deck glass breaker screen, a glass cleanup system, two new screens, a CP screen, an eddy-current separator as well as conveyors and platforms engineered and produced by CP Manufacturing.
MSS supplied Aladdin, its optical sorter that separates plastics by color and resin type and generates three output streams from one input stream.
IPS Balers supplied the multi-material two-ram baler. The TR-1388 has a patented pre-compression lid designed to increase bale density, minimize strokes and eliminate shearing, the company claims. The TR-1388 is able to process between 28 and 45 tons per hour.
Advanced MRF, which has been part of the CP Group team since January 2012, provided the entire electrical control platform and system integration.
The facility also features CP Group partners’ equipment, such as an air drum separator by Ken Mills Engineering and a film vacuum system by Impact Air.
Latest from Recycling Today
- Alpla calls 2024 year of recycling growth
- Altilium says agreement puts it on lithium recycling path
- NWRA, SWANA partner to address lithium-ion batteries
- Corinth, Texas, renews waste contract with CWD
- Fresh Perspective: Sarah Zwilsky
- Plastics Industry Association announces leadership changes
- QCC celebrates 50th anniversary
- Venture Metals acquires 2 nonferrous processors