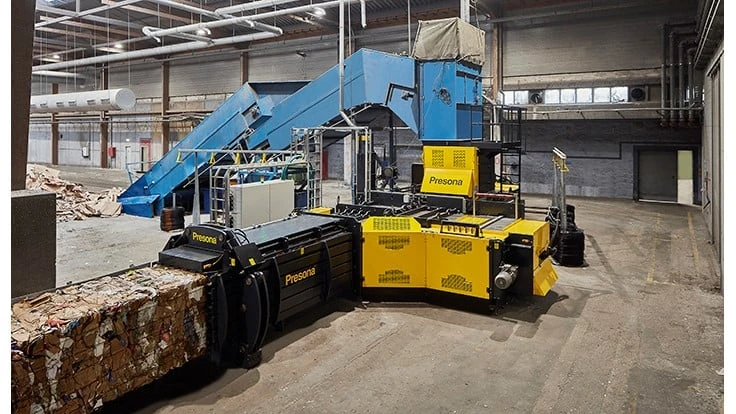
Photo courtesy of Presona.
Sweden-based Presona says it is launching a new baler design created to reduce recycling costs while increasing operational efficiency. The firm’s MP 270 MH baler is the first Presona baler built using what it calls “a revolutionary new design concept that creates super-high capacity while being very cost-effective. This means that a single MP 270 MH baler can replace several smaller balers at a significantly lower cost.”
The MP 270 MH features what Presona calls parallel processes and self-optimization. When material falls into the baler, its density is automatically measured and then the baler optimizes itself and proceeds to precompress the material to 200 kilograms (440 pounds) per cubic meter. The precompressed material is then moved to the main press which creates finished bales while new material is being precompressed, says the firm.
“Being able to precompress and make finished bales at the same time means the capacity will be much higher compared to other types of balers on the market,” says Stefan Ekström, CEO of Presona. “The precompression can be compared to a turbocharger – by increasing the density of the added material we get much higher output, i.e, more bales per hour. This means that the cost per bale will be lower.”
The new baler also is referred to as Presona’s Mega model, and the firm says it “is intended for recycling and sorting plants or other businesses that bale large quantities of material.”
Presona says the MP 270 MH “has a real capacity of 45 metric tons (49.6 short tons) of material per hour.” The firm says that’s 50 percent more than Presona’s second-largest baler, the LP 140, and three times as much as the smaller LP 60.
The MP 270 MH includes software designed to provide that Presona calls “self-optimization [that] ensures the machine is always running optimally. This function also reduces the need for staff to set up and change the baler’s programs. Less staff input decreases the risk of incorrect settings which can prevent the baler from being used to its full capacity.”
The Swedish firm says the MP 270 MH also has been designed to handle multiple materials, including old corrugated containers (OCC), plastic film, municipal solid waste (MSW) or old newspapers (ONP).
“This design’s super-high capacity means that it can replace several smaller balers at a significantly lower cost,” says Ekström. “The cost per baled ton drops significantly when you use an MP 270 MH.”
Two video clips about the new baler can be found on this web page.
Get curated news on YOUR industry.
Enter your email to receive our newsletters.
Latest from Recycling Today
- Republic Services, Blue Polymers open Indianapolis recycling complex
- Altilium produces EV battery cells using recycled materials
- Brightmark enters subsidiaries of Indiana recycling facility into Chapter 11
- Freepoint Eco-Systems receives $50M loan for plastics recycling facility
- PET thermoform recycling the focus of new NAPCOR white paper
- Steel Dynamics cites favorable conditions in Q1
- Hydro starts up construction in Spain
- Green Cubes unveils forklift battery line