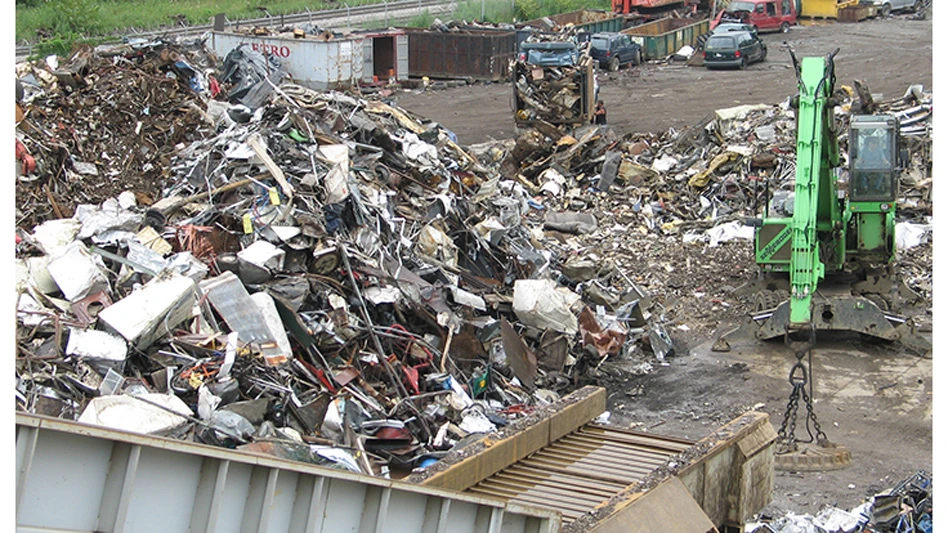
Recycling Today archives
Anthony Butchbaker founded Spartan Scanning Solutions in July 2020. The Indiana-based company offers technology solutions such as reality capture and digital twins that are designed to give auto shredder operators and steel mills high-quality data about their operations so they can better control them, improve safety and reduce energy use, to name a few benefits he says the company’s services can help users realize.
“Our mission is to revolutionize recycling on a global scale,” he says of Spartan Scanning Solutions. “We believe that this technology is the way forward for many, many industries … and I believe that steel and recycling can act as a catalyst for change and be the lighthouse for change.”
Butchbaker’s looking to start that revolution by educating the industry on reality capture and digital twin technology.
“It's tough with technology because there is a lot of smoke and mirrors and a lot of marketing fluff around it,” he says. “It's our job to be able to poke holes and in the fluff and find what is valuable and help our customers solve these problems. It's our job to bring these solutions to the table and align these technologies with our industry's challenges.”
Spartan Scanning is in discussions with recycling companies about piloting the company’s technology, he says.
“We're looking for early adopters, to push this forward. I think the psychology behind recycling is it's inherently been so hard for so long that I don't know that people are able to see that there is a better way. I want to improve everybody's safety, I want to improve their quality of life, I want to improve the quality of our planet. I want to just instill change and help people. This business doesn't have to be so hard.”
In the following interview, Butchbaker talks about the company’s services and how recyclers and steel mills can potentially benefit from these technologies. Those interested in downloading a copy of the "Decoding Digital Twin Technology Insight Report" by Spartan Scan can click here.
Recycling Today (RT): For those unfamiliar with the technologies, how would you describe them in a nutshell?
Anthony Butchbaker (AB): Reality capture is a term that encompasses many technologies. It is a tool that is capturing existing conditions or real-world conditions. So that could be a video camera all the way up to technologies like laser scanning, UAV (unmanned aerial vehicle), LiDAR (light detection and ranging, or a remote sensing method used to examine the surface of the earth), ground-penetrating radar and photogrammetry (techniques concerned with making measurements of real-world objects and terrain features from images). Basically, they create accurate digital representations of physical objects or environments. And then these digital representations can be used for planning, analysis and monitoring.
With digital twins, there are some discrepancies around that technology. Some people will call laser scans or the deliverable from reality capture a digital twin. We define that as a digital replica because at that point, there is no data exchange. Digital twin technologies take this many steps further by creating a dynamic real-time virtual twin of a physical asset, process or system. Now this virtual twin, it mirrors the real-world object in behavior and performance and allows for simulations, predictive maintenance and more efficient operations. And for it to be a true digital twin, there has to be a two-way data exchange, so the digital twin is receiving data from the physical assets and vice versa. You have to have that that two-way flow of information. The reason for that being the digital replica will represent the physical in real-time. So as the environment changes or changes are made in the physical assets in real time, those are reflected in the digital twin. And if any changes are inputted in the digital twin, those are reflected in the physical assets as well.
RT: It’s really that interconnectivity of data that makes it truly a digital twin?
AB: Yes, and it also has to be geo-referenced.
Our very first step is establishing a survey control. We do a full geodetic survey of the site (which accounts for the curvature of the surface). And that places that digital representation in its real-world coordinates. So, as you go to expand or scale this throughout your organization, if you have multiple locations, each of those digital replicas will be represented in its real-world coordinates as well.
RT: What is the advantage of that geo-referencing?
AB: It allows for more accurate simulations. When the data quality is one of the most important things, the more accurate the data, the higher quality outputs you will get. And it's vitally important for simulations. If you go to run a simulation with bad data or bad information, your results may not reflect reality.
RT: You mentioned that you're targeting the recycling and the steel industries. How can they benefit from this technology?
AB: Our goal is to eliminate unplanned downtime, but there are four pillars that we're targeting: reduce downtime, improve maintenance by switching from calendar-based maintenance programs to run-time-based maintenance programs—there's significant cost savings there, and it actually increases the asset lifetime and value—improve safety and then we get into virtual reality and simulations where we can simulate different breakdowns without putting employees or assets at risk.
The HSE (health, safety and environmental) is a huge component of this. And that aspect is more in the analyzing a high-level view of your facilities. You can analyze for slip, trip and fall hazards, any kind of compliance issues for lockout/tagout, tie-off points for equipment maintenance, and we do this in a controlled environment within an office. We can run through any scenario you can imagine. And that also is in line with trying to solve the labor shortage challenges. Using the newest tech and the latest tech shows the younger generation, that you have that early adopter mindset, you're reinvesting into yourself, you're not a dinosaur, and we use these tools to attract and help retain top talent.
Sustainability is the other key. We're targeting 30 percent to 60 percent energy reduction. That alone, year over year, would potentially add millions of dollars to the bottom line.
Our goal is to make these companies overall more profitable. We want them to produce more while spending less to do so.
RT: The energy savings, how do those come in? Can you give me some examples of that?
AB: It's just really going through and analyzing how everything's being run. We literally go through and optimize the entire system, so your electric motors are optimized for their optimal amp draw, stuff like that. And we can take a look at the actual manufacturing process as well, and make changes to that. Sometimes there are steps that don't need to be there, and we can omit those. We also have energy partners that we work with that come in and take a look at the entire operation overall, and they can give recommendations and buyout timelines for the ROI (return on investment) on these upgrades. And there is a lot of upside to this too, because there's a lot of grants and federal funding available for these programs. But our energy partners can go in and negotiate as well for off-peak-hour run times and stuff like that. We can also get them set up with renewable energy sources like solar and wind. And that's in the attempt to offset their carbon footprint and align with their ESG goals.
RT: What are some other ways companies can benefit from this technology?
AB: If you have a dust-collection system or any stacks where you're trying to clean air before it's released, we can basically automate that whole process to stay aligned with environmental regulations.
A lot of the larger shredder operations are using XRF technology to analyze the quality of their finished shred. A digital twin allows you to feed that data automatically to a mill, where they can see what your inventory levels are for any period of time, either in the past or projected into the future. They can make adjustments needed in their manufacturing process based on incoming raw materials. That is the big jump that will bring this technology into the mill.
One of the things that we are going to work on developing is inventory forecasting, which will take into account the historical data that this technology is collecting and use it to forecast inventory levels. Hypothetically, say you have 12 locations. Over the next year, based on how things are running right now, it will calculate what your projected inventories are going to be. I think that will be immensely valuable for organizations that trade on the open market. Imagine a purchaser who's maybe a little weary, you know, can you provide me this much material? The recycler can provide the customer with those insights with that transparency to their forecasting. I think that will be a huge advantage to supply chain resilience over time.
RT: I know the system's modular. Can you talk through the various modules and how they can complement one another?
AB: For the recycling digital twin, we use a few different modules. We start with reality capture as the first component. And that is actually capturing sight data in 3D, and that creates our digital replica of the physical assets. Our second module our ARVR, or extended reality platform. That will be used in tandem with HR departments and maintenance. So, for employee training, onboarding, recruiting, that will all be done through VR in the future. And we also will start immediately working with the maintenance teams to get them immersed in the 3D environment to start practicing routine maintenance, preventive maintenance, so on so forth, and the reason for that is to improve safety and reduce time-loss accidents. Then we start to introduce our real-time analytics, where we'll do an inventory. We get into the predictive analytics, which provide our immediate insights into their operational data. And we unify that, break down all silos, and that's where we really start to some cool results. From there, we get into our environmental impact analysis. We measure and analyze their environmental footprint and start to look at how we can optimize. That ties right in with their supply chain integrations where we can connect and optimize all your supply chain.
If we were going to do a digital twin, it would be before somebody upgrades its ERP (enterprise resource planning) system. The problem we see is with companies that do the ERP first, they don't know how their business is going to look after digital twins are implemented. So, what happens is you build the ERP for the business today instead of the business tomorrow. When we integrate the digital twin components, we have to basically rework the ERP again. But that is a very important integration step that gives us access to the entire supply chain for optimization and insight.
We then get into customer experience, and that is where in the future certain companies might request their products to be recycled in a certain way; they might want to have control over how their materials are processed. If you're Ford or GM and you have a bunch of stuff that's going to be recycled. If it's in your best interest to keep your carbon footprint low throughout your entire supply chain, you're going to want to select what process your materials are recycled in. I think, maybe a couple years down the road, that's where the big growth is going to happen.
And then we have our continuous learning and improvement module. We target three-to-six-month improvement cycles. Basically, we come in, we analyze, we optimize and we give a detailed action plan for our customers to execute on. The cadence of those improvement cycles is going to be per use case or per organization and depends on how fast they want to move. They might want to do one improvement cycle a year; they might want to do one every three months. It just depends on how quickly they can execute and adapt.
RT: Do they have to employ all of the modules, or can they pick and choose?
AB: There's no right or wrong way. Each module delivers significant benefits individually. And each individual module has already been proven in several relevant industries. The full potential of our system is realized when all modules are integrated. It's never been done before. So I don't have the exact numbers on how much that value compounds yet. We'll have those answers very soon. But it allows for a holistic approach to operational efficiency, predictive insights and continuous improvement. But, yes, businesses can start with one or a few modules. We would start typically with our foundational module of reality captured, and we can get them ROI pretty much from day one, just from the scanning itself.
There's a lot of interdepartmental competition. There are people fighting for budgets, and that's tough. What we're trying to do, the reason that we take the holistic approach, is we can align all of that with every department at one time, where nobody's left out; everybody has a seat at the table. And that significantly raises your odds of successful implementation—just having everybody on board from Day 1.
Latest from Recycling Today
- Radius to be acquired by Toyota subsidiary
- Algoma EAF to start in April
- Erema sees strong demand for high-volume PET systems
- Eastman Tritan product used in cosmetics packaging
- Canada initiates WTO dispute complaint regarding US steel, aluminum duties
- Indianapolis awards solid waste contract, updates recycling drop-off program
- Novelis produces first aluminum coil made fully from recycled end-of-life automotive scrap
- GPR’s hubbIT platform recognized in Georgia State University’s Marketing Awards for Excellence in Innovation