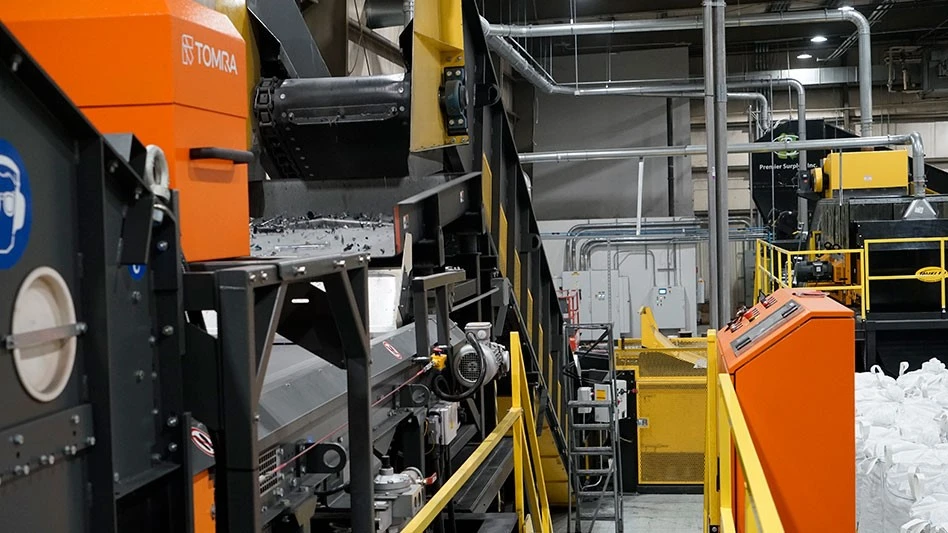
Photo courtesy of Tomra
Sensor-based sorting technology has secured a firm place in higher volume e-scrap shredding operations. The most popular application by far is the recovery of a nonferrous concentrate on the eddy current drop, which also includes the circuit boards. Using the best sensor-based sorting machines, even the thinnest copper wires can be recovered, leaving behind a plastic stream with very low metal concentration.
Making a circuit board plus wire concentrate mixture is the second-most-popular application in electronics recycling. This often happens as a secondary pass after the nonferrous concentrate has been made. To recover both of these material streams, an electronics recycler needs a sensor-based optical sorting machine that is multifunctional, which means it incorporates inductive and near-infrared/visible (NIR/VIS) sensors.
Plastics recovery often happens as a “negative sort,” meaning as it is what remains after all the valuable metals have been removed. These plastics often are shipped as a mix of polymers.
Read about how Premier Surplus of Georgia is employing optical sorting technology to process e-scrap.
Sorting plastics from shredded end-of-life electronics with sensor-based sorting is challenging: Only the nonblack plastics can be efficiently sorted using NIR-based sorters. While optical sorting technology is available commercially that can sort black plastics by polymers, it has its limitations. The variety of filler materials used in black plastics themselves makes it even harder to properly recycle the black with downstream processing. Still, with all these challenges on the plastics side, the success of sensor-based sorting on the nonferrous side has secured this technology a spot in any high-volume e-scrap shredding operation: They are often the machines that produce the highest revenue of the shredding plant.
Good material preparation is the key to make these sensor-based machines successful. The combination of machines used to do this preparation will depend on your system designer and its level of experience. The material needs to be liberated properly with the right shredding technology and presented in the right way to the machines so they can do their job optimally. That means ensuring the material is in a single layer and well-distributed on the belt and not clumped together. This improves the optical sorter’s ability to survey the belt and reduces “collateral damage,” or firing on unintended objects, when ejecting materials.
Latest from Recycling Today
- ReElement, Posco partner to develop rare earth, magnet supply chain
- Comau to take part in EU’s Reinforce project
- Sustainable packaging: How do we get there?
- ReMA accepts Lifetime Achievement nominations
- ExxonMobil will add to chemical recycling capacity
- ESAB unveils new cutting torch models
- Celsa UK assets sold to Czech investment fund
- EPA releases ‘National Strategy to Prevent Plastic Pollution’