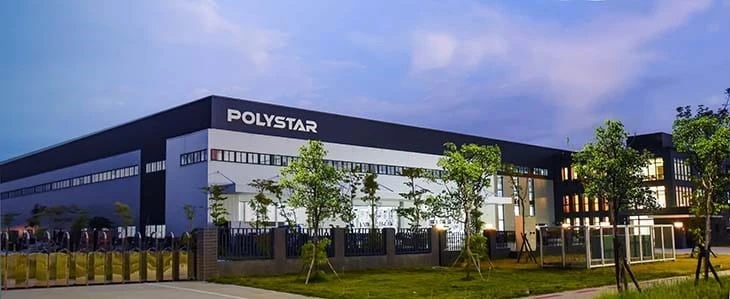
Photo courtesy of Polystar
Polystar, a plastic recycling machine manufacturer based in Tainan, Taiwan, has reported that equipment sales have doubled in 2021. The company says high demand for plastic recycling machines for postindustrial and postconsumer applications globally impacted sales.
According to a news release from Polystar, new regulations in various countries now require producers to use a higher percentage of recycled content in flexible and rigid packaging products. The company says the instability of raw material prices and supplies requires plastic producers to better recycle their byproducts.
In light of the increase in demand, Polystar says by the end of April 2022, more than 110 recycling machines will be shipped within 12 months. That figure is twice as many compared with last year.
Polystar says several reasons led to the increased drive sales in 2021, including increased demand for larger machines, product reliability and company services.
According to Polystar, the need for larger capacity machines and more machines has increased. The 800- to 1,000-kilograms-per-hour, or 1,700- to -2,200-pounds-per hour, pelletizing extruders have become a standard for postconsumer and some postindustrial recyclers.
Focus also has increased on reusing internally generated scrap by plastic producers, the company says. Businesses including packaging film and woven bag producers now require higher quality recycled content to reduce production costs as much as possible.
Polystar says its Repro-One recycling technology is a combination of shredder, extruder and pelletizer in one machine. This one-step process produces the best possible pellets quality at the lowest operation cost, according to the company, enabling producers to reuse pellets back in polypropylene tape extrusion lines.
The packaging film sector and plastic bag producers are required to use a much higher percentage of recycled pellets in the end products. For better quality control and to maximize the reusability back into the film extrusion lines, more producers have decided to recycle their production scrap internally instead of outsourcing it, the company says.
Recent installations of the Repro-Flex recycling machines, a cutter-compactor integrated model designed for recycling film scrap in Denmark, Italy and Switzerland, are equipped with features that minimize energy consumption and labor intervention.
The impact of COVID-19 continues to present various supply chain issues, resulting in high shipping costs and a shortage of supply. As demand for recycling machines remains strong, Polystar says it continues to prepare in-stock recycling machines to avoid long delivery times.
The company says it can better serve customers with faster machine delivery times and spare parts support by keeping machine components in stock. Polystar's manufacturing facility in Taiwan continues to operate at 100 percent during this time, ensuring customers receive the recycling machines within a short time.
Polystar says the delivery time for standard recycling machines like the Repro-Flex 85, Repro-One and Repro-Air is 30 to 45 days.
Latest from Recycling Today
- Paper recycling is focus of two January webinars
- Disruption likely for material flows in mid-January
- Blue Whale Materials to expand Oklahoma lithium-ion battery recycling plant
- CARI names new president and CEO
- Interzero revamps leadership structure
- Altilium secures $5M investment from Marubeni
- DOE report provides recommendations to increase recycling, reuse of wind energy equipment
- Sonoco makes leadership changes