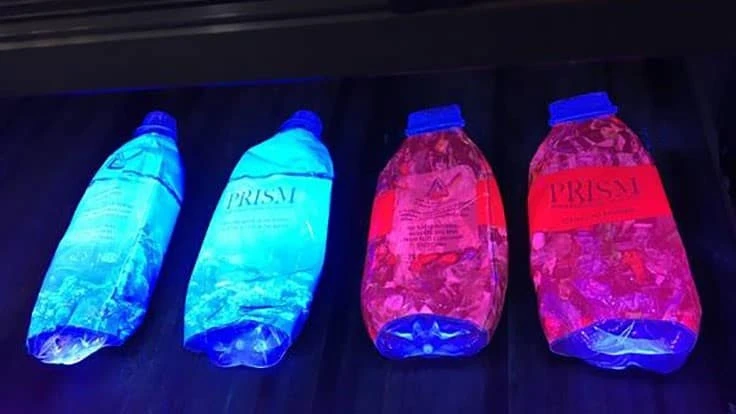
Nextek
While polypropylene (PP) is the most versatile and easiest to recycle polymer and one of the most widely used materials in packaging for consumer goods, this packaging is not widely recycled. Additionally, PP is virtually nonexistent as a food-grade recycled material because of the inability to separate food-grade PP from nonfood-grade PP.
Consequently, while polyethylene terephthalate (PET) bottles can be readily recycled back into PET bottles, PP often is recycled into nonfood-packaging applications, such as crates and bins, or ends up in landfills or incinerators.
Technological limitations
Current technologies limit recyclers from sorting plastic by polymer type. Identifying what the product once contained has been a nearly impossible task. With no effective way to differentiate between a bleach bottle and a milk bottle of the same polymer type, the plastic scrap sector has suffered from a severe lack of value creation and, therefore, investment.
As policymakers, governments and organizations around the world continue to explore ways to reduce or eliminate the amount of plastic packaging sent to landfills, the debate around food-grade recycled PP, which could easily be recycled otherwise, has been thwarted by this inability to properly identify it during the sorting process.
Food-grade plastic has been the most complex to obtain because of the risks associated with recycled plastics potentially containing toxic chemicals that could be dangerous to human health. Up until now, recyclers have not been able to differentiate and capture specific materials and separate food from nonfood packaging. However, a new technology could change this.
A bright idea
An identification technology for food-grade-quality material has the potential to transform the sorting process in recycling facilities.
The consortium’s members are Nextek Ltd., which is the PRISM project manager and an independent consultancy that provides recycling R&D services; Brunel University London – Wolfson Material Processing, which has provided luminescent expertise; CCL Label, a multinational label maker headquartered in Farmingham, Massachusetts; Enlightened Lamp Recycling, a fluorescent lamp recycling firm based in Surrey, England; Johnson Matthey, a specialty chemicals, catalysis and process technology company based in London; Mirage Inks, a Frome, England-based manufacturer for printing inks used on packaging; Tomra Sorting Solutions, a division of Norway-based Tomra that manufactures sensor-based sorting and processing technology for the recycling industries; and WRAP, the U.K.-based nonprofit that works with governments, businesses and communities to deliver solutions designed to improve resource efficiency.
The PRISM process is designed to be simple. Fluorescent markers that are produced from materials recovered from fluorescent lamp recycling, not rare-earth-based compounds, are printed on labels or plastic packaging sleeves.
As the mixed plastics run along a conveyor belt, the high-speed sorting system is illuminated by an ultraviolet (UV) light source that identifies and reads the coded PRISM label. Jets of air propel the plastic containers into the appropriate recycling category.
Complementary technology
.gif)
Following extensive trials, PRISM is now well-proven in material recovery facilities (MRFs) and is plug-and-play ready. It is complementary to existing near-infrared (NIR) optical sorting technology and can be adapted to most sorting facilities around the world to target specific recycling streams, such as food-contact plastic packaging.
This technology uses traditional labeling and branding methods that can be coded to specify the status of the package. The PRISM labels are designed so that whether they are flattened, crumpled or soiled, they will still be detected. The markers also are designed to be removed during recycling, leaving no traces for the next cycle of use.
Using this technology, plastic scrap can now be sorted in a single step at a speed of 3 meters per second (10 feet per second) and 2 metric tons per hour to more than 96 percent purity with a yield in excess of 95 percent. This meets the European Union’s stipulated 95 percent purity for PET food-grade plastic in a single sorting step at full sorting speed.
This innovation presents new opportunities for brand owners that want to recover their packaging as part of the circular economy.
Through Nextek, PRISM’s marker technology is set to launch for recycling food-grade PP packaging (as well as all other plastics), allowing recyclers to effectively sort and recycle used plastics into food and nonfood applications.
Sponsored Content
Labor that Works
With 25 years of experience, Leadpoint delivers cost-effective workforce solutions tailored to your needs. We handle the recruiting, hiring, training, and onboarding to deliver stable, productive, and safety-focused teams. Our commitment to safety and quality ensures peace of mind with a reliable workforce that helps you achieve your goals.
This technology has the potential to harness the untapped potential of postconsumer PP, revitalize plastics recycling and reduce our current dependence on virgin plastics in food packaging.
Edward Kosior’s expertise in the plastics recycling sector spans 46 years, split between 23 years as an academic and 23 years working in plastic packaging recycling. He has been instrumental in designing numerous modern recycling plants and has achieved a number of patented recycling breakthroughs. In 2004, Kosior founded U.K.-based Nextek Ltd. to provide consultancy services to assist in the strategic approaches to sustainable packaging, waste reduction and minimal life cycle impact. He is Nextek’s managing director and is involved with many industry associations, universities and research organizations and is a Fellow of the Society of Plastics Engineering and Fellow of the Institute of Materials, which awarded him the Prince Philip Medal for Polymers in the Service of Man in 2019. He can be contacted at edkosior@nextek.org.
Get curated news on YOUR industry.
Enter your email to receive our newsletters.
Latest from Recycling Today
- AF&PA report shows decrease in packaging paper shipments
- GreenMantra names new CEO
- Agilyx says Styrenyx technology reduces carbon footprint in styrene production
- SABIC’s Trucircle PE used for greenhouse roofing
- Hydro to add wire rod casthouse in Norway
- Hindalco to invest in copper, aluminum business in India
- Recycled steel price crosses $500 per ton threshold
- Smithers report looks at PCR plastic’s near-term prospects