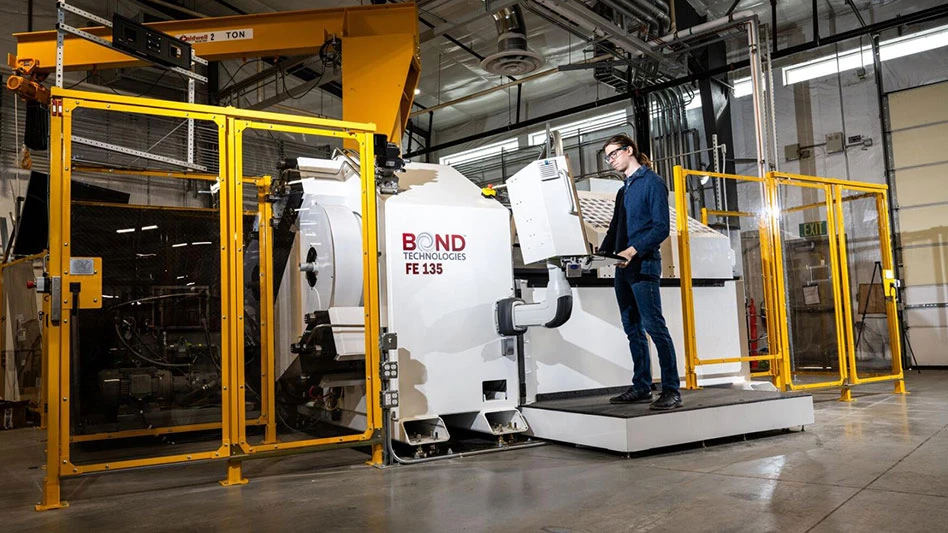
Photo courtesy of PNNL
Earlier this year, Pacific Northwest National Laboratory in Richland, Washington, announced that it took delivery of the second generation of its ShAPE, or Shear Assisted Processing and Extrusion, machine. “ShAPE 2” allows researchers to produce larger, more complex extrusions using billets made from postconsumer aluminum—a major step toward many real-world industrial applications for PNNL’s patented ShAPE technique, according to PNNL.
Bond Technologies, Elkhart, Indiana, designed and manufactured ShAPE 2.
RELATED: Reshaping the aluminum extrusion industry
Scott A. Whalen, co-developer of ShAPE and PNNL chief materials scientist, says the billets the lab is using to make its extrusions are produced from twitch, used beverage cans and other postconsumer scrap including gutters and downspouts as well as 6000 and 3000 series remelt scrap ingots.
“From a technical standpoint, one of the things that's really interesting is we can blend these scrap streams together to get compositions that are close to spec alloys like 6061, 6111 that are commonly used in industry," he says. "But even though we blend these scrap streams to get something close [to a specification alloy], it might have higher iron than the specification. And one of the really advantageous things about the process, because of all of this extreme shear deformation that goes on during extrusion because of the rotating part, those iron-bearing intermetallics really get broken down to a superfine scale and distributed throughout the aluminum matrix.
"So, although they're there, their effect is much more muted compared to if you just tried to extrude these on a conventional extruder. So, even though the composition may not be to an exact spec, it can be much more tolerant. And that's where the exciting part is for the process and the whole recycling space.”
Traditionally, aluminum extrusions are produced by using heat to soften a billet before pushing it through the die. However, with ShAPE, a rotating head near the die combines with a hydraulic press on the opposite end that forces the billet toward the die.
The rotating head produces friction that heats and softens the portion of the billet entering the die. The heat created by the machine’s high shear forces also act to pulverize impurities in the recycled aluminum billets into tiny particles that are uniformly dispersed within the aluminum microstructure, reducing the size of undesirable iron-rich compounds, for example. These particles can generate microfractures in recycled aluminum products manufactured using conventional methods, according to PNNL. Therefore, ShAPE aluminum extrusion offers considerable energy savings by eliminating the need to dilute impurities found in recycled aluminum with primary aluminum before processing.
The effect of the shearing force means the billets used to produce the extrusions do not need to be homogenized prior to extruding, further reducing carbon emissions.
Whalen says ShAPE 2 has 50 percent more ram force than the first generation of the machine as well as three times the motor power and four times the torque. He says additional controls on ShAPE 2 also allow PNNL to control the temperature during the extrusion process by modulating the rotational speed.
This added benefit of controlling the temperature of the extrusion process with ShAPE 2 has created additional possibilities with extrusions, Whalen says, by intentionally varying the process temperature. He offers an example with 6000 series aluminum where one portion of the extrusion can be processed at a higher temperature than another portion.
“Then when you go to heat treat it after the fact, you can get different regions with different mechanical response," he says. "So, we can actually make graded structures by having this ability to control the temperature during the extrusion.
“You could imagine something like a roof rail on a car that goes all the way from the front to up over your head and back behind you. The part near the passengers would like to be high strength, and the part that would be more upfront would like to have a high toughness, meaning more energy could be absorbed. You could have a single structure that can have locally modified properties to satisfy two different parameters, like strength in one spot and energy absorption somewhere else.”
That is not possible with traditional extrusion technology, he says, noting, "What ends up happening is a single part would be overdesigned in one area.”
PNNL plans to use ShAPE 2 to demonstrate more industry-relevant profiles.
“Our first machine could make extruded profiles of a half-inch diameter," Whalen says. "This new machine will allow us to make profiles that are on the order of a couple inches in diameter, with more complexity to them as well. It's just one more step toward showing that this process can actually scale to what would be a much larger industrial-scale machine.”
A machine for industrial production would require 2,000 to 3,000 tons of ram force, whereas ShAPE 2 has 130 to 150 tons of ram force, Whalen says, while the torque that's required on would be 150,000 Newton meters compared 12,000 Newton meters on ShAPE 2.
Despite the limitations on the size of the extrusions it can produce, he adds that PNNL has been able to achieve competitive production rates with its research scale machine.
“We’re excited to make larger components from aluminum scrap that we can then send out to finishing houses to see how our recycled material responds to anodizing, painting, powder coating and so on,” Whalen says. “For the building and construction industry, it will be important to show that these coatings perform just as well on ShAPE-extruded aluminum scrap as they do on conventionally extruded primary alloys.”
PNNL’s research in this area received support from the Department of Energy’s Office of Energy Efficiency & Renewable Energy, Vehicle Technologies Office, Lightweight Materials Consortium (LightMAT). ShAPE technology has been granted seven U.S. patents with 34 patents pending. The technology is available for licensing in various fields of use. For more information about licensing opportunities, contact PNNL’s Office of Commercialization.
Latest from Recycling Today
- ArcelorMittal wins legal round in GFG dispute
- Real Alloys partners with Enviri on residuals diversion project
- Registration Now Open for C&D World 2025
- The Scrap Show: Johnnie Jr., Roger and Marcie Rodriguez, Comal Iron & Metals
- ASTM releases textile circularity standards report
- Volvo adds two models to updated excavator line
- Eagle International tire balers create safer conditions
- Eagle International tire shears: Size matters