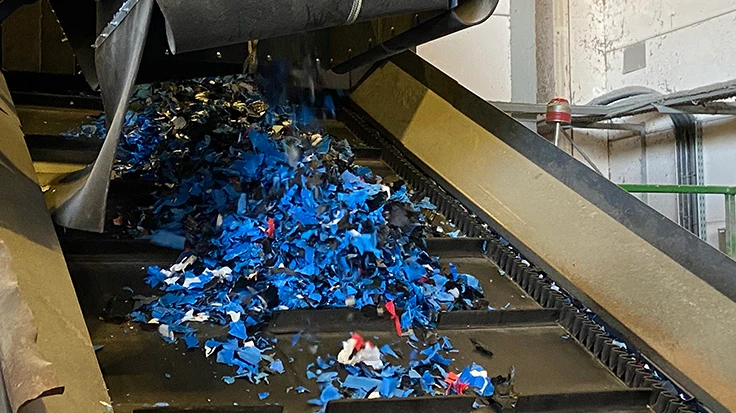
Recycling Today archvies
Analyses of chemical recycling, some of them critical, previously have focused on whether plants have been able to reach scale or, in some cases, whether they can handle mixed plastic feedstock as well as some initial advocates of the technology have claimed.
An report published in late June from ProPublica adds one more element of criticism in asserting that at least one process categorized as chemical recycling, also termed advanced recycling by some of its backers, do not convert much of their inbound feedstock back into plastic.
The report by Lisa Song cites several sources and portrays an attempt to gather data from numerous companies and organizations to determine what happens to a discarded piece of plastic when it enters either a mechanical recycling process or a chemical recycling process.
Song’s concludes that while anywhere from 55 percent to 85 percent of discarded plastic directed to a material recovery facility (MRF) and next-stage mechanical recycling becomes plastic again, pyrolysis-based chemical recycling processes convert just 15 to 20 percent of inbound material back into plastic.
The consensus of sources Song interviewed was that via pyrolysis, 80 to 85 percent of plastic scrap heading to a pyrolysis facility instead becomes diesel fuel, hydrogen, methane and other chemicals.
That result may be unsurprising to professionals within the recycling and polymers industries, but Song says the low-double-digit result may not be well received by people who construe the chasing arrows symbol on plastic objects as meaning the item can be turned back into plastic.
She also looked into dilution practices undertaken by users of mechanically and chemically recycled materials, again finding the pyrolysis process came up short.
Users of postconsumer recycled resins (PCR) in some applications may need to blend that material with virgin resins, with the PCR comprising 25 to 50 percent of the total product.
While a naphtha product that can be used in new plastic formulas is created via pyrolysis, Song says much of the naphtha created using recycled plastic is contaminated with chemical additives mixed in to make products bend or keep them from degrading in the sun.
Polymer makers who wish to use this naphtha can “overpower” those contaminants by diluting them with virgin naphtha made from crude oil. Song writes, however, that unlike the 25-to-50-percent blend common in mechanical recycling, at least 90 percent of the naphtha used in pyrolysis is fossil fuel naphtha and nothing that comes out of pyrolysis physically contains more than 10 percent recycled material.
Citing Steve Jenkins of energy and commodities industry consulting firm Wood Mackenzie, Song concludes that in three years, “At best, the world could replace 0.2 percent of new plastic churned out in a year with products made through pyrolysis.”
Get curated news on YOUR industry.
Enter your email to receive our newsletters.Latest from Recycling Today
- ICM to host co-located events in Shanghai
- Astera runs into NIMBY concerns in Colorado
- ReMA opposes European efforts seeking export restrictions for recyclables
- Fresh Perspective: Raj Bagaria
- Saica announces plans for second US site
- Update: Novelis produces first aluminum coil made fully from recycled end-of-life automotive scrap
- Aimplas doubles online course offerings
- Radius to be acquired by Toyota subsidiary