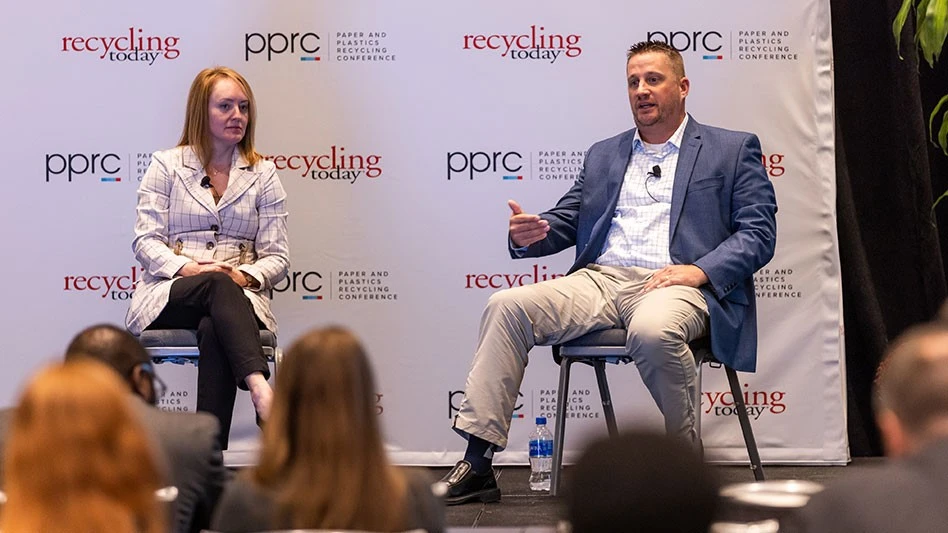
Photo by Mark Campbell Productions
Consumers of postconsumer resin (PCR) had the chance to weigh in on the steadfastness of their commitments and those of their customers to using recycled content given pricing volatility and supply concerns during the Paper & Plastics Recycling Conference, which the Recycling Today Media Group hosted Oct. 19-20 in Chicago.
“We just came off a two-year period where we hit all-time highs in price and all-time highs in demand,” said moderator Scott Saunders, general manager of KW Plastics, a Troy, Alabama-based recycler of high-density polyethylene (HDPE) and polypropylene (PP) and a manufacturer of paint cans made from recycled PP. “Now it seems like the world is tilted back to more normal pricing levels.”
Saunders was joined by panelists Diane Marret, sustainability director at Berry Global, and Brian Miller, regional sales manager at Cascade Engineering Family of Cos. Both panelists use PCR in a variety of applications, from consumer packaging to recycling carts and automotive parts.
As a converter primarily of plastics for packaging used in the food and beverage, personal care and food service sectors, Marret of Evansville, Indiana-based Berry described sustainability as a “team effort.” The company converts roughly 4 billion pounds of raw material every year into packaging, with the goal to transition 1 billion of those pounds to circular material. “We have a lot of challenges ahead of us, but we’re making great progress,” she said.
Miller described Grand Rapids, Michigan-based Cascade Engineering as a “multibusiness manufacturer” and injection molder serving a variety of industries, from Tier 2 automotive suppliers to the waste and recycling sector. “We have a corporate sustainability goal to use 25 percent alternate material in all our manufacturing,” he said. “That can be challenging at times, especially for us serving a variety of markets in some cases where brand owners will not allow for recycled content. And we have other industries where they’re certainly more accepting.”
Cascade uses roughly 75 million pounds of recycled HDPE annually in waste and recycling carts it manufactures for the solid waste and recycling industry, he added, as well as engineering grades, nylons and PP.
Marret said a variety of factors are driving Berry’s use of recycled plastics, with recycled-content mandates playing a role. “In Europe, we are already seeing some of that pull,” she said, adding that with the passage of recycled content legislation in New Jersey and Washington as well as in California, “it’s certainly becoming more of a common conversation” in the U.S. “Is it driving the demand? Not quite yet. There are pockets here and there. But certainly, that is a big factor. … I suspect we’ll see a pretty significant ramp-up in that demand here in the next few years.”
Miller said municipalities and haulers, including Waste Management and LRS, expected Cascade to use a certain level of PCR in the past, “but then they’d expect to see some sort of pricing discount.”
In the automotive sector, Miller said, “it really depends on what the part is. … Anything painted, the specifications won’t allow us to use [recycled content] at this point.”
Regarding shifting attitudes toward PCR content, Saunders said that 20 years ago, brands would require a nondisclosure agreement (NDA) from KW because they didn’t want to be known for using PCR. Now, they want an NDA because they don’t want their competitors to know where they’re getting their PCR from. “So, it’s a big shift,” he said.
Inflation is increasing prices for the raw materials brands use in their products, he continued, which is putting additional pressure on PCR pricing. “And, so, some of the largest companies in the industry that have made forward-reaching commitments, and a year or two ago, price was not a concern; it was can we get supply. We’ve seen them shift back now to price is a very big concern.”
“One of the things we’ve seen to help bridge the price conversation is taking steps to lightweight products,” Marret said. This can help to offset some of the cost of recycled content, she added. “But, of course, that comes with additional work of making sure that the design still meets all the performance specifications.”
Miller said in his experience some brands’ commitments to using PCR “outweighs the cost challenges. So, absolutely, we are seeing brand owners willing to pay more for parts with recycled content.”
“Mechanical and chemical recycling are complementary technologies, there’s not going to be a place in the future where one replaces or outstrips the other. I don’t see that ever happening,” Marret said regarding the tension between mechanically recycled plastic and chemically recycled plastic. “Mechanical recycling works really well in certain streams of materials, certain applications—that will always be the case.” She added that chemically recycled material makes sense in applications where either the processes or the products don’t tolerate the potential regulatory concerns around mechanically recycled material quality, such as the pharmaceutical industry.
Latest from Recycling Today
- Magnomer joins Canada Plastics Pact
- Electra names new CFO
- WM of Pennsylvania awarded RNG vehicle funding
- Nucor receives West Virginia funding assist
- Ferrous market ends 2024 in familiar rut
- Aqua Metals secures $1.5M loan, reports operational strides
- AF&PA urges veto of NY bill
- Aluminum Association includes recycling among 2025 policy priorities