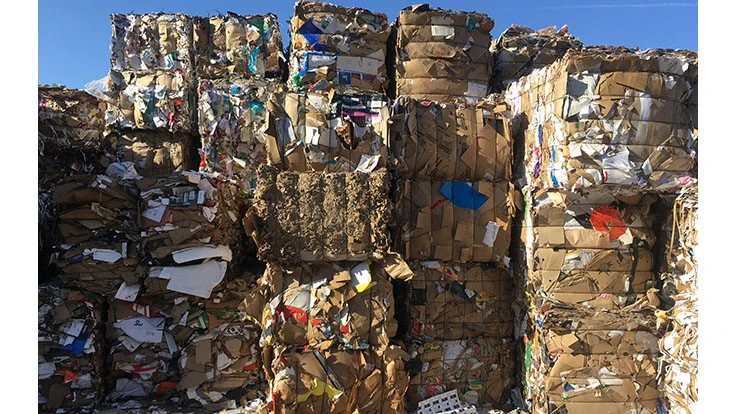
Photo by Recycling Today staff.
CVB Ecologistics, based in Tilburg, Netherlands, has a dozen balers operating at its nine recycling plants in Belgium, the Netherlands and the United Kingdom, says Wil van Dommelen, who has purchasing manager responsibilities for the firm.
While the firm processes plastic and textiles, baling recovered fiber represents a large portion of CVB’s recycling activity.
According to van Dommelen, he and his colleagues take several factors into consideration when determining when the company’s bottom line will benefit from replacing an existing baler with a new one.
Watching for signs
As portrayed by van Dommelen, CVB takes a proactive approach when assessing baler performance. The time to start shopping for a replacement baler, he says, “will be the moment that your baler can no longer deliver the performance which you were used to or which you need, such as the tonnage per hour.”
When output decreases, “also your cost calculation (price per ton) is no longer correct,” he adds.
Van Dommelen continues, “Such a reduction in performance is usually a combination of several defects in the baler, or when there is a risk of major costs for a baler. A baler has standard wear parts that need to be replaced periodically, such as guide strips, movable parts in the strapping system, hydraulic components and valves, oil filters, etc., but these are usually the smaller costs that have to be made to keep the baler productive.”
Beyond the accumulating smaller costs, “There can also be a large cost to a baler that makes it ever wiser to replace the baler with a new one,” the recycler says. “Examples of this [can be] the press channel has worn out in such a way that there is too much play on the ram, and therefore also play on the master cylinder, which could break off again as a result. At that moment, it is wise to opt for a new press.”
Fluid leaks can be another sign a baler is showing its age. “If the hydraulic seals in the valve block (the baler’s motor) are so worn that internal leaks occur and the baler can no longer build up its original pressure, then it is usually the time to replace it,” van Dommelen says. “Practice often shows that repairing never gives the same result as new.”
Maintenance plays a role in how long a baler can last, he notes, but so too can the design and fabrication quality of the baler itself. “A high-quality press [that] is also well maintained and that has been handling a fairly easy-to-process product can last for 20 to 30 years or longer,” van Dommelen says. He cautions, “There are also cheaper presses for sale with an expected lifespan—a lot less—possibly only 10 years.”
Making the right choice
The baler shopping process then creates a new decision tree, with considerations that include how much tonnage a baler will be asked to handle and what types of materials.
“The size and capacity of the press must be geared to the quantities that you want to process on it,” van Dommelen says. Even if old corrugated containers (OCC) are a predominant grade handled, recyclers still need machines that can handle varying infeeds, he adds.
“As a recycler, you have to ensure that you can process all sizes and qualities on it, and some qualities must first be changed in structure by means of a shredder or conditioner/ruffler before a sturdy stackable bale can be made,” van Dommelen says.
For OCC, he says it is “important to know the dimensions of the OCC to determine how big the conveyor belt and the hopper you need are and what size baler you need. In order to be able to process all incoming cardboard, a baler with a large filling opening (2 meters, or 6.5 feet) is recommended.”
The company’s steady intake of OCC means CVB seeks out several standard features. He says of the company’s 12 balers, “They all have about the same capacity, varying from 120 tons to 140 tons press force and press capacity up to 50 or 60 tons per hour (depending on the product).”
The CVB balers all are “equipped with the largest possible supply conveyor belt and filling funnel, and our balers can handle just about all qualities, regardless of which location or depot they arrive at,” van Dommelen says.
Baler manufacturers compete to offer new features, which van Dommelen says should be a due diligence factor in the shopping process. “If that new technology can contribute to increasing the tonnage per hour or make it possible to process difficult-to-process products more easily, then it is a matter of calculating how much time such an improvement or investment will take to have it earned back,” the recycler adds. “It could also be the reason to invest in a new faster or better baler.”
CVB Ecologistics has a baler fleet that varies in age, van Dommelen says, because the company does not retire a baler unless it shows clear signs of not maintaining its productivity.
“This includes balers that are only a year old, but there are also balers that are already 20 years old,” van Dommelen says of CVB’s balers. “So, the age of the baler is not a reason to process less tonnage on it. The capacity of a baler is not only judged by age but also by the defects that occur as they get older.”
Latest from Recycling Today
- BlueScope, BHP & Rio Tinto select site for electric smelting furnace pilot plant
- Magnomer joins Canada Plastics Pact
- Out of touch with reality
- Electra names new CFO
- WM of Pennsylvania awarded RNG vehicle funding
- Nucor receives West Virginia funding assist
- Ferrous market ends 2024 in familiar rut
- Aqua Metals secures $1.5M loan, reports operational strides