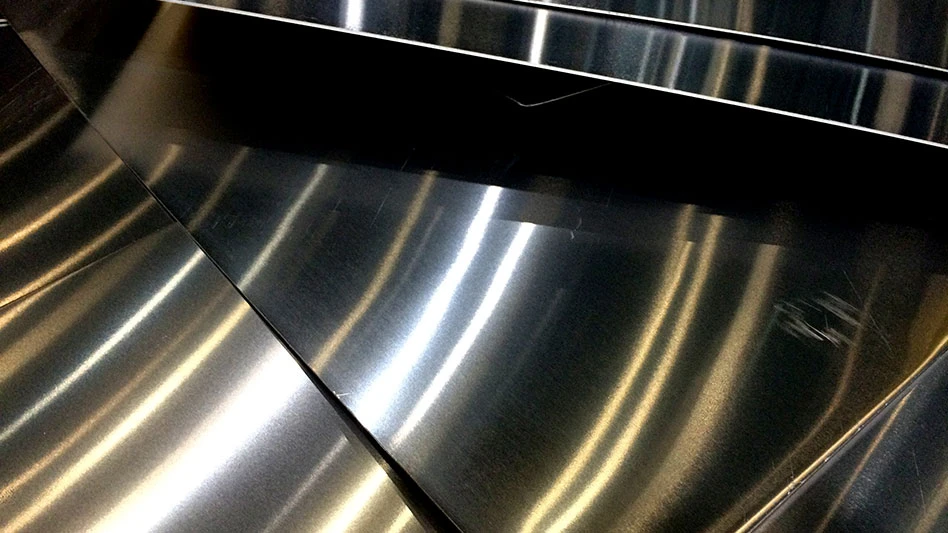
Photo courtesy of Novelis Inc.
Atlanta-based aluminum rolling and recycling company Novelis Inc. has announced a new sustainability initiative, Novelis 3x30, which sets carbon-related sustainability goals and identifies priorities to accelerate the company’s decarbonization and circularity efforts.
“This is a continuation of a direction we’ve been going in for quite some time," Derek Prichett, senior vice president of global metal at Novelis, tells Recycling Today.
With Novelis 3x30, the company is focusing on focusing on three objectives to reach by the end of 2030:
- increasing its average recycled content to 75 percent from today’s 63 percent;
- becoming the lowest-emissions, flat-rolled products aluminum provider at less than 3 metric tons of CO2e per metric ton of flat-rolled product (FRP) shipped; and
- continuing investments to lead the industry to circularity.
“Novelis 3x30 is our road map to going further, faster in our efforts to decarbonize our products and increase the circularity of aluminum,” Novelis President and CEO Steve Fisher says. “Novelis has long been a sustainability leader in our industry, but we need to accelerate our progress and help our customers achieve their own goals for decarbonization in a shorter timeframe. We are committed to innovating and implementing solutions that significantly decarbonize aluminum and make it the material of choice for the circular economy.”
“We’ve made tremendous progress toward creating a more circular economy for aluminum,” adds Pierre Labat, senior vice president and chief strategy and sustainability officer at Novelis. “The 3x30 vision strengthens our commitment to leading the industry toward decarbonization and is essential to our company purpose of Shaping a Sustainable World Together. As we look to the future, the success of Novelis 3x30 will be dependent on a companywide effort by our employees, along with meaningful collaborations with our customers, suppliers and research partners.”
Expanded use of recycled content
Novelis began increasing the recycled content in its products in 2011, making capital investments in the casting, recycling and melting, which includes a new integrated mill in Bay Minnette, Alabama, that is under construction, and the newly opened recycling center in Guthrie, Kentucky. That facility has a 240,000 metric ton casthouse that is coming online focused on recycling automotive scrap and producing automotive sheet products, Prichett says.
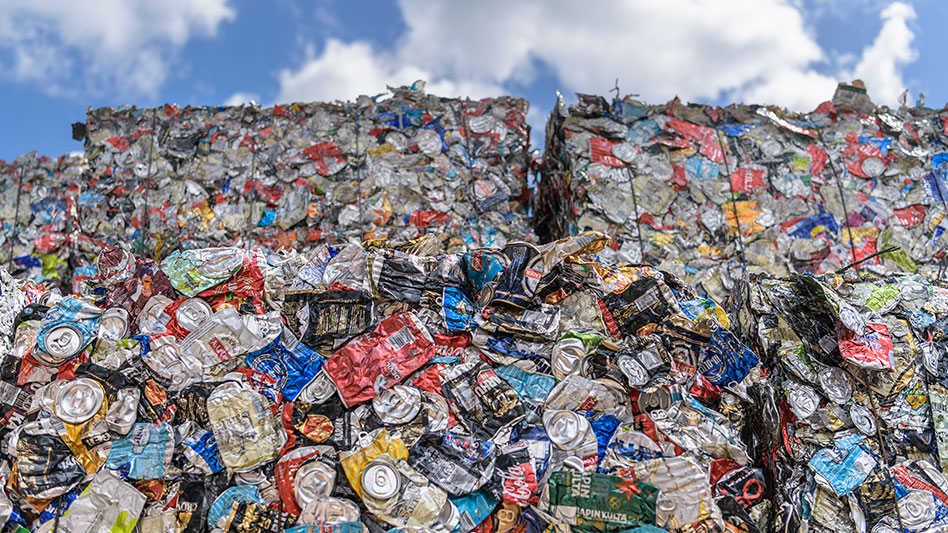
Outside the U.S., Novelis has announced the expansion of its Latchford, U.K., facility for used beverage can (UBC) processing in anticipation of improvements in collection rates related to the European Union’s Packaging Waste Directive, which Prichett says is leading many new jurisdictions in Europe to implement deposit return systems, which is expected to increase the flow and quality of UBC scrap in the U.K. and several other countries in the EU.
In addition to capacity investments, Novelis is developing high-recycled-content alloys.
“We've been redesigning a lot of our alloys to accept more recycled content without losing properties." Pritchett says.
He adds that Novelis continues to expand its closed-loop recycling systems for the scrap its consumers generate in production as well as its scrap buying capabilities, not only in terms of staffing but also the types of scrap it’s buying and the geographies it’s buying in.
“There's a continuous expansion of our commercial footprint to attract the scrap that we need in order to achieve our goals," he says.
While Novelis works with some brokers, Prichett says scrap buying largely is done internally.
“We are direct buyers of over 2 million tons a year of scrap today, and we will grow that by yet another million tons by the time we hit our 75 percent-recycled-content objective," he says.
While Novelis has established closed-loop systems to get automotive stamping scrap back, it’s now focusing on end-of-life vehicles, namely the zorba and twitch grades, which are the nonferrous outputs of automotive shredding.
The company has partnered with Sortera Technologies, a company working to separate those aluminum fractions into what Prichett says are “more useful” categories.
“Our principle is not only to recover aluminum back into aluminum wherever we can, but we want to recover it by alloy back into the original alloy as much as we possibly can," he says.
He adds that cast alloys comprise almost half of twitch by volume and are not suitable for producing rolled sheet.
“We need to do a separation of that material from the wrought fraction," he continues. "And then, in some cases, we're actually going further, and we're starting to separate the wrought fraction even by alloy. So, we try and cut it into a 3000-series fraction, a 5000-series fraction, and a 6000-series fraction, so that we can then recover those fractions back into their respective product alloys. And that's a much more efficient way for us to recycle and preserve the value of the material.”
In addition to Sortera, Novelis is working with multiple partners in North America and Europe on sorting aluminum scrap to put the material to its best use.
Novelis also has been working with the Can Manufacturers Institute and the Aluminum Association to increase aluminum can recycling, including by promoting deposit-return legislation. Prichett notes that the effort to pass such legislation in Washington state was not successful.
“We're constantly evaluating the potential for us to improve the legislative framework, whether that's deposit or other approaches,” he says. “We're open to other approaches, as well, if they work,” noting that an extended producer responsibility-based solution seems to be gaining ground in Texas.
“We're not trying to be singularly focused on deposit. Deposit we know is effective, but there are lots of people that oppose it for good reasons. We recognize that it takes more than just one legislative tool to solve the problem. We are working openly with people on multiple different solutions.”
Engaging customers
Prichett says closed-loop recycling in the automotive sector benefits Novelis as well as the companies it supplies by increasing the recycled content of the next load of material that it ships to them. But they recognize a need to capture postconsumer material as well.
“Our automotive customers are increasingly interested in recovery of end-of-life scrap and incorporation of end-of-life scrap back into their products,” he says. “And this is part of the reason that we've been working hard on developing high recycled-content alloys that give us flexibility to incorporate that end-of-life scrap into our alloy mixtures.”
He explains this is done in cooperation with the company’s customers: “They need to evaluate the high-recycled content coils … to make sure they're fit for purpose.”
Prichett says Novelis has had success with companies like Mercedes in Europe, which has been able to successfully take its high-recycled-content alloys and manufacture advanced parts with some of their most difficult specifications.
“We can't do this alone, and it really needs the support of the entire supply chain” from sorting material to the development and production of the appropriate alloys, he says. “If we can show the OEMs [original equipment manufacturers] that we can meet the functional specification with a different alloy composition, then they're typically open to discuss that and then adjust the chemistries accordingly.”
Lower-carbon prime inputs
In addition to increasing its use of scrap, Novelis also is looking at the primary inputs into its process to lower its carbon footprint.
“There's always a certain amount of prime that is required in our alloys in order to bring the alloys back into chemistry,” Prichett says. “We've been focusing very hard on getting the carbon footprint down in the primary that we buy as well, so we're working with all the large global suppliers of primary to make sure that we can buy the lowest carbon content prime that we possibly can.”
Novelis says its Scope 1 emissions come from the energy it consumes at its operations and represent 9 percent of the company’s total emissions in its last fiscal year. Scope 2 emissions come from the energy Novelis source from utilities, comprising 6 percent of its total emissions in its last fiscal year, while Scope 3 emissions, which are related to the prime aluminum the company purchases, accounted for 85 percent of the company’s total emissions in its last fiscal year.
By buying metal directly from the primary producers, Prichett says, Novelis will be able to guarantee you where that metal is coming from.
“We have traceability back to exactly where that metal came from, what smelter came from, what bauxite it was made from," he says. "We can get a full carbon profile of that metal as it comes in, whereas, when you're buying from traders, the origins of the metal tend to change over time, and you don't always have full visibility of what they're providing to you.
“I'm not saying that we're moving completely away from traders, but we are trying to increase the amount that we're buying directly from a producer, and then we're focusing on producers that have large quantities of low-carbon metal available.”
Prichett adds that Novelis’ 3X30 objectives are challenging, requiring hard work, investment and partnerships with the entire supply chain.
“We can't do this on our own, so we are focused on having a large tent and bringing as many people into the tent as we possibly can to help us and to help the industry with our objectives,” he says. “We believe these objectives will not only support Novelis but support our customers and support aluminum as a material, and that is good for the industry longer term.”
Latest from Recycling Today
- Republic Services, Blue Polymers open Indianapolis recycling complex
- Altilium produces EV battery cells using recycled materials
- Brightmark enters subsidiaries of Indiana recycling facility into Chapter 11
- Freepoint Eco-Systems receives $50M loan for plastics recycling facility
- PET thermoform recycling the focus of new NAPCOR white paper
- Steel Dynamics cites favorable conditions in Q1
- Hydro starts up construction in Spain
- Green Cubes unveils forklift battery line